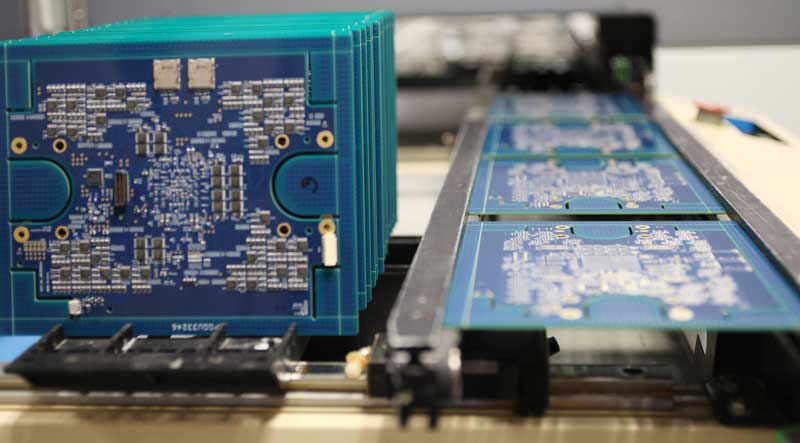
Which Programming Method is Right for You?
Semiconductor devices are used in a wide range of electronic applications, from smartphones to industrial machinery. Programming these devices is a crucial step in their manufacturing process, allowing them to perform specific functions. There are several methods to program semiconductor devices, each with its own advantages and disadvantages.
In-System Programming (ISP)
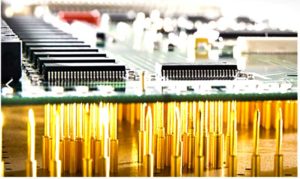
Bed-of-Nails fixture connects the PCB to the final test
In-system programming (ISP) is a method that enables semiconductor devices to be programmed after installation on a circuit board, without requiring removal. This programming method allows for easy updates, and flexibility in the programming process, and avoids device disruption. However, ISP requires dedicated programming hardware or software to interface with the device, which may be slower than other methods. Moreover, when the programming process exceeds a few seconds, it can create bottlenecks, slowing down the production line and making it harder to scale. Learn more here.
In-Circuit Programming (ICP)
In-circuit programming (ICP) is a method that enables semiconductor devices to be programmed while they are in use, without requiring removal. This programming method allows for updates without disrupting device operation, flexibility in the programming process, and avoids device removal. However, ICP requires dedicated programming hardware or software to interface with the device, which may be slower than other methods. Learn more here.
Offline Parallel Programming
Offline programming is a method that enables multiple semiconductor devices to be programmed simultaneously. This programming method is faster than ISP and ICP, allows for a high volume of devices to be programmed at once, and can be easily scaled up. Offline programming requires a dedicated socket adapter with a custom algorithm for each device type. For instance, a socket receptacle can accept similar device types from different manufacturers (for example, a BGA(153), but will require a custom algo for each device to ensure it meets the specs for that device).
Automated Offline Programming
Automated programming is a subset of offline programming that uses automated equipment to program semiconductor devices. This programming method is faster than development kits and allows for a high volume of devices to be programmed simultaneously. Moreover, automated programming allows for individual device programming, and is more easily scaled by adding additional resources and shifts.
Development Kits
Device programming kits are tools used to program individual semiconductor devices. This programming method allows for individual device programming and prototyping. However, development kits can be slower than other methods and require manual device handling, which can be time-consuming and error-prone. If a prototype goes into full production, other methods should be explored, which will require first article proofing for the production programmer.
In conclusion, choosing the right programming method for your programmable devices depends on your specific needs and requirements. Consider the pros and cons of each method before making a decision. Ultimately, selecting the right programming method can save you time and costs while ensuring your devices function properly.
Programming Method |
Definition |
Advantages |
Disadvantages |
Approx. Usage |
In-System Programming (ISP) | Programming a device after it has been installed on a circuit board, without needing to remove it | Allows for easy updates in the field, avoids device removal, and provides flexibility in the programming process | Requires dedicated programming hardware or software to interface with the device, which may be slower than other methods | 40% |
In-Circuit Programming (ICP) | Programming a device while it is in use, without needing to remove it | Allows for updates without disrupting device operation, avoids device removal, and provides flexibility in the programming process | Requires dedicated programming hardware or software to interface with the device, which may be slower than other methods. | 20% |
Offline Parallel Programming | Simultaneously programming multiple devices with the same programming sequence using specialized equipment | Efficient for large-scale production, automated to increase throughput, and reduces programming errors | Requires specialized equipment that may be relatively expensive, and less flexible for smaller production runs | 25% |
Development Kits | Dedicated hardware and software used to program a single device at a time, typically used for low-volume production or prototyping | Provides a high degree of control and flexibility over the programming process, can program a wide range of devices, suitable for low-volume production or prototyping | Requires dedicated hardware and software that is typically inexpensive, and time-consuming for large-scale production or programming of multiple devices with different programming sequences | 15% |
Note: The percentages provided are rough estimates and may vary depending on the specific industry and application.