Universal Hardware/Software
Each device has specific programming parameters. It is not just a matter of sending an electrical signal to a specific pin—each device requires a unique algorithm to ensure it is programmed correctly.
For instance, for a device programmer to support a NAND flash device, two algorithms are needed. The first is the conventional device programming algorithm as specified by the semiconductor manufacturer. The second is the BBM algorithm. The BBM algorithm is a user-selectable software module that interfaces with the device programming algorithm. Its implementation depends upon the target system, not just the NAND device. The challenge is in obtaining a well-defined BBM algorithm specification. See White Paper Here.
Algos “translate” the data into a specific pattern based on the specs from the semi-house. It also sends the correct electrical signal to the correct pin. See Signal Integrity Article Here.
In 1996, BPM introduced the 4100, the first universal fine-pitch automated pick-and-place programming system. Finally, there was a solution to program, at scale, a variety of devices. Again, prior to the 4100, pick-and-place programmers could only program-specific families of devices.
Fast-forward to Today
BPM Microsystems pioneered universal device programming, but nowadays, most device programming solutions are “universal,” right? While it’s true that the days of single-use programmers (except for some extremely high-volume machines) died 25 years ago, that doesn’t mean that all “universal” programmers are truly universal.
Take, for instance, Data I/O. They make automated and manual device programmers in the US and China; they promote their programmers as “universal,” but that depends on your device programming requirements. Data I/O uses two different programming site technologies. Their FlashCORE III sites were developed in 2009; their newer LumenX sites came out in 2016. Let’s say you have a mix of eMMC, MCU, and EPROM devices to program. Their “universal” solution would require two sets of sites; LumenX sites for faster programming with eMMC devices and FlashCORE III to program the others. Are they, in fact, “universal?” Sounds like “not really.”
BPM’s 9th Generation Technology launched in 2016. 9th Gen sites with Vector Engine™ Co-Processor accelerate flash memory waveforms for programming near the theoretical limits of silicon design. The faster the device, the faster it’s programmed. With data transfer rates to 50 Gb per second, and verify rates up to 200 MB per second, 9th Gen sites offer the industry’s fastest times with even more capacity compared to other systems in its class. This is up to 9 times faster than competing “universal” programmers, offering the Largest Memory Support in the industry―256 GB, upgradeable to 512 GB. Plus, by downloading image files up to 25 MB per second to all programmers simultaneously, the system rapidly produces devices at maximum achievable throughput.
PSV5000 vs BPM 3928
Comparing the two platforms (Data I/O vs. BPM) with similar specifications in a typical configuration, a Data I/O PSV5000 would require two FlashCORE III sites, plus one LumenX site (total of 3), while a BPM 3928 would require two 9th Gen sites (which is included in the basic machine configuration). The BPM 3928 is upgradable to five more sites (a total of seven); The PSV5000 can add three additional sites for a total of 6 sites. But only three or four could be used at a time (depending on which site technology is added). The BPM solution is much less expensive because it is actually universal, and allows you to utilize all the connected sites simultaneously.
One could argue that the PSV5000 could be set up with six FlashCORE III sites or six LumenX sites (for a total of 12 sites)– you would only have to switch out the sites when you set-up for the specific job. Realistically, that’s not a viable option. The price for just the sites would cost more than double the original PSV5000 and would take many additional hours to do each change-over.
In the case of a site failure (it happens), with BPM’s universal sites and fault-tolerant hardware/software, the “dead” site can be automatically bypassed; thus, production still goes on (albeit, at reduced capacity). Recall the mix of eMMC, MCU, and EPROM devices to program. Their “universal” solution would require two sets of sites; LumenX sites for faster programming with eMMC devices and FlashCORE III to program the others. if the single LumenX site goes out on the PSV5000, your programming on the LumenX site is stopped until you can get the site replaced or repaired.
It’s always a good idea to plan for failures (they happen) by having a spare site available on-site (all APS manufacturers can provide you with spare kits). With BPM’s single-site technology, you only need one spare, which saves thousands of dollars. When getting a quote on an APS, make sure to ask for spares (and if you’ll need just one or two).
Universal could also mean “future-proof.” Knowing that 9th Gen sites can program legacy devices as well as the newest flash devices means your investment is not soon obsolete. BPM has customers that are still programming on ten- to 15-year-old (and older) 8th and 7th Gen machines. BPM continues to provide support for these legacy systems, and plan to for the foreseeable future.
Sockets
Socket modules and socket cards are the electro-mechanical interfaces between the programmable semiconductor device and the programmer. It’s one of the secrets to BPM’s Universal Programming. The robust design is ideal for manufacturing and design environments where high signal integrity and reliable performance are critical.
The sophisticated technology of BPM Microsystems’ active circuitry delivers the cleanest waveform signals to the device by eliminating noise, ground bounce, and overshoot, which allows for the most reliable vector testing available to ensure the highest quality and overall yield.
Signal Integrity designed into the socket card allows for high quality/high-speed communication between the programmer and the device under test (DUT). High-quality communication allows for high-speed data transfer. How?
- Multiple layer PCBs
- Ground plane
- Controlled impedance
- Active circuit
- High-quality, gold-plated Samtec connectors on all 9th Gen Sites and Sockets
BPM Microsystems offers a substantial number of socket modules and socket cards to support thousands of devices from over 218 semiconductor manufacturers. Currently, there are over 39,000 devices supported on 9th Gen (three times greater than BPM’s nearest competitor).
New socket module and socket card designs are continuously added and can be requested to meet your programming needs (you can request support here).
“Universal” also means many of our older sockets (7th and 8th Gen) work with 9th Gen sites. When you upgrade to 9th Gen’s much faster programming protocol, it’s possible you can use your existing sockets (see if your socket is compatible here).
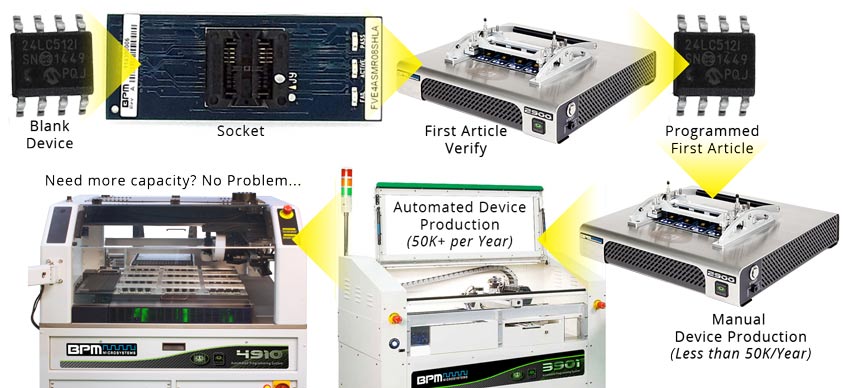
First Article to automated device production, use the same software, same sockets, same algos, same results.
Finally, universal means using the same software (BPWin), and sockets/algos on all 9th Gen programmers, from manual to automated (the only additional thing needed on the automated programmers are pressure plates which are inexpensive and last forever). No matter if it’s the first article to final production, nearly everything is compatible.
Conclusion
BPM’s universal device programmers are truly universal, in every sense of the word. In an uncertain world during uncertain times, it’s comforting to know a BPM solution will deliver years of reliably programmed devices, and that “universal” actually means “universal.”