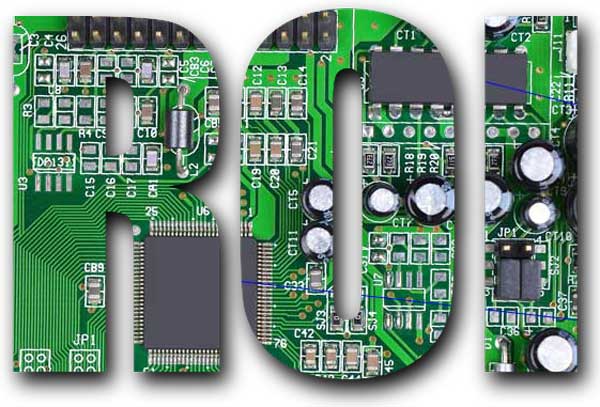
Protected: How to Program In-House, Part II
Password Protected
To view this protected post, enter the password below:
To view this protected post, enter the password below:
Some things to consider in a Disaster Plan
- Hardware/Software contracts are up-to-date
- Ensures the fastest response in line-down situations
- Spares are on-site and/or available overnight
- Schedule deliveries for consumables, especially sockets
- Sockets are consumable items
- The schedule ensures they are manufactured/delivered based on your requirements
- Lead time to build a socket can vary, from days to weeks
- Multiple prequalified vendors
- Pre-qualify First Articles ahead of time from your partner supplier
- Negotiate price per device before the disaster takes place
Some problems are good. It’s important for the modern manufacturing operation to prepare for the worst, and the best. There are lots of things that can go wrong. Add this to the list: what happens if one or more people on your line come down with Covid-19? You still have parts to program and production lines to supply. And as things rebound, what will you do if you are hit with an increase in orders? You (no doubt) have built-in capacity; but what if it doubles, or triples (or more)? BPM Microsystems builds systems and accessories that make it easy and cost-effective to make device programming a viable (and profitable) option in-house. Their line of programmers is universal, meaning they utilize the same software and accessories, from the smallest to the largest systems. From the first article (the initial first approved programmed device) to production, the only difference is throughput. Manual systems are perfect for starting out and/or smaller lot sizes (up to 50,000 parts per year). They also come in handy to augment the automated system’s capacity, or for programming short-run parts. BPM’s automated systems are the fastest and easiest to set-up of any programming systems. They are made for programming large data devices, such as eMMC HS400, NAND, NOR, and Serial Flash devices, and other nonvolatile memory devices such as MCUs, PLDs, and FPGAs. High-speed signals support devices up to 200 Mhz and the latest eMMC HS400 modes with data transfer rates of 2.5 nanoseconds per byte. With data transfer rates to 50 Gb per second, and verify rates up to 200 MB per second, BPM’s Automated Systems offer the industry’s fastest times. This is up to 9 times faster than competing “universal” programmers, offering the Largest Memory Support in the industry―256 GB, upgradeable to 512 GB.
WhisperTeach™ is patented hardware/software that automates the critical z-height measurement, which reduces set-up times by as much as 83%. More importantly, it improves yield and job performance compared to manual teaching methods. CyberOptics™ vision component auto measure delivers on-the-fly alignment to maximum device reliability and throughput.
Learn more about WhisperTeach™ auto Z-height teach system here.
Adding capacity is fairly straightforward. The first option is to add overtime and/or add shifts. BPM’s set-ups don’t require extensive training, so quality and throughput won’t decline after 5 pm. Next, add programming sites and sockets to existing workflows. If utilizing manual systems, additional programmers can be “daisy-chained” to a single workstation (up to 12 total). For automated programmers, additional sites may be added. Each site has the ability to add up to 4 additional sockets (a socket is the electrical interface of hardware/software to program a specific device). Adding sites can double, triple (up to 10X) capacity, depending on which system is used. BPM’s universal sites mean you don’t need two different site technologies for programming different classes of devices. BPM supports more than triple the number of devices as their nearest competitor (36K vs 12K). Some BPM systems, such as the low-cost 3901 or 8th Generation automated systems, can be upgraded for higher throughput, with more devices per hour and/or additional sites or peripherals. When you experience a line-down (for whatever reason), you need solutions that allow you to quickly shift production without skipping a beat. For programming devices, contact your nearest programming center, such as Arrow, Avnet, or A&J. The set-up files can be securely transmitted; if they don’t have the sockets, simply overnight the sockets used on your production. Utilizing programming centers is another way to balance out your work-flow; when a temporary need overwhelms your workflow, you can outsource for extra capacity.
It’s not a matter of “if” things go wrong. It’s a mathematical certainty. If 2020 has taught us anything, it’s prudent to be ready for just about anything. With a little forward planning, you should keep production moving. BPM’s systems are built to grow with your business; they have programmers that are still operating daily after 15 years or more. Contact your preferred Programming Center and BPM Microsystems to develop a disaster plan in advance.
See “Market Forces” Article here
Job changeovers can be a major hassle, but they don’t have to be. In this live demonstration, the Sales Guy (Colin Harper) does a job changeover in 3 minutes (and almost half of that he’s talking and not working). BPM automated programmer job changeovers are fast and easy and require no tools. This overview is a portion of a virtual demo. To see more, check out https://www.bpmmicro.com/3901-virtual-demo/
Since about 2010, the strongest market segment for Automated Programmers has been Automotive suppliers. Automotive suppliers have an ever-increasing need for programming as cars become more complex and technology-driven. They also often require 3D inspection and laser marking to ensure consistent quality and to track inventory. Big projects, with millions of programmed devices, make device programming in-house a no-brainer.
Smaller OEMs, while perhaps having many of the same needs as the Automotive guys, were constrained by limited resources. As their programming needs outgrew their ability to produce on manual systems, the only option was to outsource to the programming houses or ship their component manufacturing off-shore.
Then came the perfect storm of 2019: a crippling trade war, followed by a growing pandemic.
Read more Here
Moore’s law (Moore’s law is the observation that the number of transistors in a dense integrated circuit doubles about every two years (see https://en.wikipedia.org/wiki/Moore%27s_law) )states integrated circuits double in both speed and number of circuits roughly every two years. As programmable devices become smaller, denser, and more complex, most machines that program those devices have become more expensive, and require experienced technicians to operate, maintain and troubleshoot.
The downside to outsourcing programming are legion: added cost, minimum orders, long lead time, and reprogramming or scrap when data files change. Another danger is protecting your intellectual property. Once your source code leaves the vault in your factory, it is vulnerable to theft (This is not a concern if you’re using a reputable programming house in your home country or region. If your source code crosses a border, you’re putting your company at risk. ) Due to current market conditions, companies are increasingly concerned about interruptions in the supply chain, especially for components sourced from Asia.
Until recently, it wasn’t feasible for most Original Equipment Manufacturers (OEMs) with significant programmed device requirements (A good ball-park for an automated programmer is in excess of 50K devices per month. ) to justify the cost of bringing programming in-house. Automated Programming Systems (APS) were expensive and complex to set-up, run and maintain. That’s when BPM changed the game.
BPM Microsystems started making EPROM programmers in the mid-80s. BPM’s Founder Bill White was a student at Rice University, working on his degree in Electrical Engineering. He needed a way to get his code on a read-only chip, and discovered there just wasn’t a good way to do it. So, he built his own programmer. While he was still living in the dorm, he started selling his programmer, the EP-1, by mail order, and BPM Microsystems was born. BPM has a history of simple-to-operate, reliable systems that deliver the industry’s best results.
BPM launched its first automated programmer in the mid-90s: the BPM 4100 was the only universal fine-pitch automated pick-and-place programming system. Compared to today’s machines, it was slower and more difficult to set up (and operated in DOS). Compared to the single-purpose machines of that day, the 4100 revolutionized device programming by combining universal programming technology with universal fine-pitch handling capability.
The “holy grail” of consistent automated programming results is the Z-axis teach. There are three axes on an automated handler: X, Y, and Z (Theta is the 4th “axis” which determines the precise orientation of the device (rotation)). X (horizontal) and Y (vertical) are easy; a downward camera with a bomb site allows for precise placement on the center of a device. The Z (up/down) is, by far, the most difficult and the most important. Both the pick and place locations, if off by less than the width of a human hair, can cause major problems. Manually-adjusted z-teach can go badly two ways: pick (or place) too high can cause misalignment of the device; place (or pick) too low, where the nozzle comes in contact with the device, can cause micro-cracks. Devices with micro-cracks usually pass the initial test (green light), but can oxidize the sensitive metal film causing devices to fail in the field.
BPM is the first to solve the Z-axis conundrum with a patented solution called WhisperTeach. It utilizes hardware and software to turn the device nozzle into a sensor. Without coming in contact with the device, the automated system detects the height of the device to within 15 microns (4 times finer than a human hair) and automatically completes the “teach” in less than 8 seconds. A trained technician, although not as accurate as WhisperTeach, can teach a single location in about a minute. On a single job set-up, the difference in time is dramatic: WhisperTeach set-up is usually around 5 minutes; manual teach can take up to 45 minutes to an hour. When you add the loss of productivity to the reduction in precision, things can quickly get dicey. Regardless of which programmer, pick-and-place systems are incredibly repeatable: if the teach is off by a little, the pick/place will be consistently off as well.
WhisperTeach is available on all BPM automated systems, not just on its high-end systems.
Since about 2010, the strongest market segment for Automated Programmers has been Automotive suppliers. Automotive suppliers have an ever-increasing need for programming as cars become more complex and technology-driven. They also often require 3D inspection and laser marking to ensure consistent quality and to track inventory. Big projects, with millions of programmed devices, make device programming in-house a no-brainer.
Smaller OEMs, while perhaps having many of the same needs as the Automotive guys, were constrained by limited resources. As their programming needs outgrew their ability to produce on manual systems, the only option was to outsource to the programming houses or ship their component manufacturing off-shore.
Then came the perfect storm of 2019: a crippling trade war, followed by a growing pandemic.
OEMs recognize the risk in outsourcing critical components, such as programmed devices, to off-shore suppliers. They are looking more closely at options that reduce their reliance on forces beyond their control in a way that reduces costs and speeds go-to-market.
BPM has a history of innovation; they also have a reputation as the “luxury brand” in device programming– feature-rich, and pricy, especially when compared to low-cost Asian machines. That changed with the launch of the 3901, the lowest cost full-featured automated system with vision centering (Precisely center the device (even if the operator is slightly off) and affect the theta spin while traveling to the site location, which delivers incredibly precise placement without the need to slow down) and true universal support (Only BPM has the same site technology, same software, same sockets and algorithms in all of their 9th Generation programmers. With over 35,000 supported devices, including the most difficult and mission-critical, no one in the industry comes close.). The 3901 starts at under $90,000 with a maximum configuration of 16 device sockets (Sockets are specific to the device they program and act as the bridge between the device and the programmer).
Within 10 days of the 3901 launch in October of 2019, the first machine sold to a telecommunications OEM in the Northeast US. The second soon sold to a Midwest heavy equipment manufacturer. Both companies needed an affordable system that can supply their catalog of programmed devices to their lines. The 3901 quickly became the fastest-selling automated system in BPM’s 35-year history. Equipment manufacturers, especially those in North America and Europe/Middle East, finally have a lower-cost option for their device programming needs without sacrificing quality and capability.
With the launch of the seven-site 3928 in November 2019, companies have access to automotive-level quality (available 3D inspection) with up to 28 sockets in a fully-loaded system that starts at just under $110,000.
You can’t control world events– what you can do is provide your manufacturing team with an uninterrupted supply of high-quality, low cost programmed devices. To find out more about how BPM is changing device programming for OEMs, please call us at +1 (713) 688-4600, or Toll-Free in the US: (855) SELL BPM. Ask us about the industry’s only self-installation for APS that’s fast, easy, and free.
Automotive Programming by Volume of Devices (The charts in this article are based on feedback from BPM Microsystem’s automotive customers )
Just as an example, automotive OEMs use a variety of methods to get the job done. There’s an advantage to programming at the In-Circuit Test (ICT) where all of the components are already soldered on the board. By doing programming and testing in one step, you can combine several steps and save a lot of time. This only works when the programming time is very low (less than a few seconds); if not, you could end up with a huge bottleneck, and in the event of an error you likely have to scrap the whole board or remove and re-solder the bad device and do it all again.
Consider this: the majority of devices programmed for automotive applications are done offline (50%). Both in-house off-line and outsourcing to a programming house are programmed on the same equipment using off-line automated programming systems, such as BPM’s 3901.
The chart presented here represents the correlation between data density and programming times on a Surface-Mount Technology (SMT) line. As the density of data, the complexity of devices, and the number of devices per car increase, the need for cost-effective programming solutions becomes imperative. The beat rate, defined as the total throughput on the SMT line, must be considered to ensure that the programming times do not exceed it.
In this survey, off-line programming accounts for 80% of programming, with in-house off-line and outsourced programming contributing. Off-line programming is a feasible solution that can keep pace with the production line through shifts or machine additions and strategic outsourcing. In-system, in-circuit, and in-line programming methods may no longer be feasible due to increased costs and longer lead times.
In-house off-line programming offers several benefits over traditional in-system, in-circuit, and in-line programming methods. Firstly, in-house off-line programming is more efficient, reducing the cost per device and lead times compared to outsourcing. Secondly, the source code can be updated more frequently, ensuring that the latest version is used on the line and securing your intellectual property. (IP Theft: See 2018 Bloomberg article )
BPM’s team can assist in identifying the best solution for your specific needs. We provide a comprehensive analysis of your project, including benchmarks and return on investment, and offer recommendations. Our team of experts will guide you in asking the right questions to make an informed decision.
We take into account several factors when evaluating the best solution for your needs. Quality, ease of use, throughput, cost-per-device, and long shelf-life are just a few of the factors considered in our evaluations. With many of our machines still operational after 10+ years, BPM should be considered as a potential solution in your decision-making process.
At BPM, we strive to be a valuable resource for our clients. However, we may not always be the best option for every project. In such cases, we are transparent and honest about it. Our goal is to provide our clients with the best possible solution, even if that means referring them to another provider.
The charts presented here represent the correlation between data density and programming times. Off-line programming is a feasible solution that can keep pace with the production line through shifts or machine additions and strategic outsourcing. In-house off-line programming offers several benefits over traditional in-system, in-circuit, and in-line programming methods, including improved efficiency, reduced costs, and the ability to update the source code frequently.
BPM’s team can assist in identifying the best solution for your specific needs, considering factors such as quality, ease of use, throughput, cost-per-device, and long shelf-life. We strive to be a valuable resource, but may not always be the best option. In such cases, we are transparent and honest about it. Contact BPM today to learn more about how we can help you with your programming needs.
Off-line programming is the process of programming the device (either by a manual or automated process) prior to SMT or manual soldering of the device to the board.
Surface-mount technology (SMT) is a method for producing electronic circuits in which the components are mounted or placed directly onto the surface of printed circuit boards (PCBs). An electronic device so made is called a surface-mount device (SMD).
In-system programming (ISP), also called in-circuit serial programming (ICSP), is the ability of devices to be programmed while installed in a complete system. The primary advantage of this feature is that it allows manufacturers of electronic devices to integrate programming and testing into a single production phase, and save money, rather than requiring a separate programming stage prior to assembling the system.