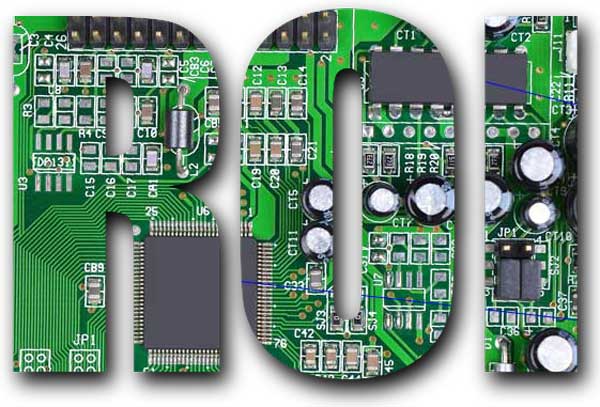
Run an ROI Calculator to Determine Feasibility of Automated Programmer Purchase
Run an ROI Calculator to Determine Feasibility of Automated Programmer Purchase
Request ROI Analysis
Provide us with a device list, with approximate programming data upload, and the number of devices needed per month, and we’ll provide you with an ROI Analysis.
Example Calculation
In this real-world example, we’ll break down the numbers to bring device programming in-house:
Total Devices per Year to program | 1,000,000 |
Average Lot Size (Quantity of devices per Job) | 1,000 |
Factory Burdened Hourly Labor Rate (Direct labor + Overhead) | $15 |
Estimated APS Solution Price | $89,999 |
Capital Equipment Amortization | 5 |
Machine Utilization Rate | 85% |
Estimated Consumable cost per device (sockets, carrier tape, cover tape) | $0.01 |
Expected Machine Throughput | 1088 |
Programming Cost per Device (if outsourced or other programming process) | $0.15 |
Estimated Job Chageover Hours | 333 |
Production Hours Required | 1415 |
Equipment Operation Cost per Year | $39,220 |
Estimated Cost per Device to program | $0.0492 |
System Payback Calculation | |
Devices Programmed per Day (250 days per year) | 4000 |
Savings per Device | $0.10 |
Savings per Day | $403.12 |
Work Days until System Purchase Payback | 223.3 |
*BPM can help you with some of these numbers. If you provide us with a device list, how much data is to be programmed, and how many devices you need per month, we can give you a minimum configuration of a recommended system. Changeover hours are determined by how many changeovers per shift.
Payback in a few months
In the example above, it would take a few months (not years) to make device programming in-house a profit center! Once paid for, it’s almost all profit. Many customers use these systems for 10+ years and achieve 5-10X ROI.