by Scott Bronstad | Jun 26, 2023 | Case Study, Technology
Part 5 – Unveiling the Power of Offline In-Socket Programming
As we delve further into the advantages of offline in-socket programming, having scrutinized aspects of quality assurance (Part I), flexibility (Part II), ease of troubleshooting (Part III), and efficiency (Part IV), it’s time to turn our gaze to yet another vital feature– versatility. Offline programming boasts an impressive capacity to handle diverse device types, sizes, and programming requirements, a feature not limited by the constraints of the assembly process. This versatility stems from several key factors.
Universal Device Compatibility
Offline programming systems are typically engineered to work with an extensive range of non-volatile memory devices. This includes Flash, EEPROM, Microcontrollers, PLD, CPLD, FPGA, and Antifuse devices. This broad compatibility allows the same system to cater to different device types, significantly enhancing flexibility.
Smooth Change Management
Offline programmers facilitate the easy implementation of changes in firmware or programming data. Any necessary update can be executed without disrupting the assembly line, a feature especially beneficial when needing to frequently switch between different products or versions.
Adaptable Socket Adapter Designs
Offline programming systems often support an array of adapter designs and sizes, making them capable of handling an extensive range of packages. These systems can be quickly adapted to various device requirements, offering a high degree of versatility.
Concurrent Programming
Offline programming systems contain multiple independent programmers and socket adapters that add fault tolerance to the system and can process multiple devices concurrently. If the programming time is short, only a few adapters are used. This capability further extends the versatility of offline programming by allowing the user to scale the system to meet the requirements of each unique job.
For an OEM producing a range of devices, from home automation gadgets to wearables, the versatility of offline programming is invaluable. With support for a wide range of non-volatile memory devices and easy handling of firmware changes, offline programming allows them to swiftly adapt to varying device requirements and changes in product versions.
Support for Advanced Programming Protocols
Offline programmers often accommodate various advanced programming protocols. This adaptability allows them to be fit for a wide range of programming tasks. Further, a range of common file types are also supported.
Reduced Production Line Dependency
Offline programming operates independently of the assembly line’s operations, making it adaptable to varying production demands and schedules.
Contrastingly, other programming methods such as in-line programming, in-circuit testing (ICT), or functional test programming may face limitations in their adaptability, ability to handle a variety of devices, or managing multiple tasks simultaneously. They are directly reliant on the production line’s schedule and must be able to meet or exceed the production line’s “beat rate.” Plus, there is downtime, labor, and a higher level of skill required to change to different device types or programming jobs..
In essence, the versatility offered by in-socket programming makes it a robust tool for electronics manufacturers, enabling them to be more flexible and responsive in their operations.
Stay tuned for the final part of our series, where we will discuss how offline programming can maximize assembly line uptime.
Read Part I | Read Part II | Read Part III | Read Part IV
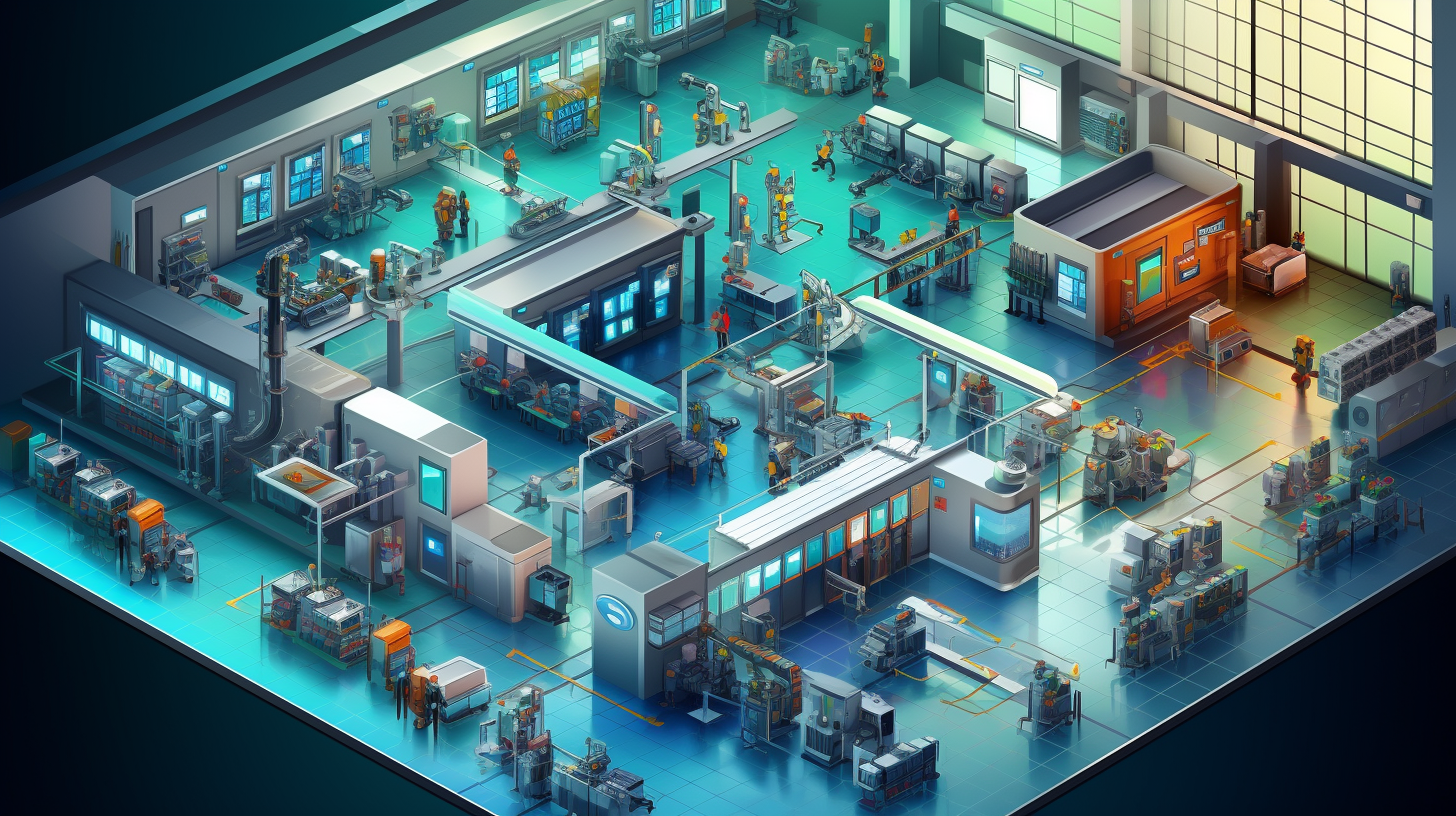
by Scott Bronstad | Jun 22, 2023 | Case Study, Technology
Part 4 – Unveiling the Power of Offline In-Socket Programming
Having journeyed through the advantages of high-quality assurance (part I), flexibility (part II), and simplified troubleshooting (part III) offered by offline in-socket programming, we now turn our attention to another salient feature – efficiency. This pivotal aspect of the offline methodology promises potential time and cost savings, alongside a range of other benefits that significantly contribute to the productivity of device programming.
Capitalizing on Scalability
A single automated programming system can program millions of devices annually. This impressive capacity often equates to supporting multiple production lines with just one machine and a part-time operator per shift.
Leveraging Batch Programming
Offline programming systems have the ability to program multiple devices concurrently, a stark contrast to in-line methods that program devices sequentially. This parallel programming approach dramatically enhances throughput, allowing more devices to be programmed within a reduced timeframe.
Minimizing Downtime
As offline programming operates independently from the main assembly line, it prevents assembly line downtime. Any arising issue during programming can be addressed independently, sparing the entire production line from interruption.
Adapting Work Schedules
The decoupling of programming from the overall production process offers greater flexibility in scheduling. This permits programming to be carried out during off-peak hours or when the assembly line is inactive, maximizing resource utilization.
Suppose a Contract Manufacturer (EMS company) operates multiple production lines producing a variety of products for various clients. Using an automated offline programming system, they can program millions of devices per year and dozens or more different “ICs,” supporting several production lines with only a part-time operator per shift. This dramatically increases throughput and reduces overall operational costs.
Reducing Rework and Scrap
Offline programming assures individual programming and verification of each chip before assembly. This approach reduces the cost and time associated with rework and scrap, thereby improving the overall efficiency of the manufacturing process.
Improving Inventory Management
The capability to program chips in advance facilitates better inventory management and smoother production scheduling. This proactive strategy can diminish stockouts and overages, boosting operational efficiency and adaptability to demand changes.
Optimizing Resource Allocation
Offline programming facilitates a more effective allocation of human and equipment resources. While programming occurs, other assembly, testing, and packaging tasks can continue in parallel, optimizing the entire manufacturing process.
Boosting Energy Efficiency
In many instances, offline programmers are more energy-efficient than their in-line counterparts. They program multiple chips simultaneously and are operational only when needed, as opposed to running continuously alongside the assembly line.
In essence, the efficiency benefits from offline in-socket programming translate into substantial cost savings and productivity improvements. This makes it an invaluable asset for electronic manufacturing companies. Join us for the next part of our series, where we will explore the versatility that offline in-socket programming brings to semiconductor manufacturing.
Read Part I | Read Part II | Read Part III
by Scott Bronstad | Jun 20, 2023 | Case Study, Technology
Part 3 – Unveiling the Power of Offline In-Socket Programming
In our exploration of device programming thus far (See Part I, See Part II), we’ve addressed how it ensures high quality and offers unparalleled flexibility in streamlining production workflows. Now, we transition to another distinct advantage – troubleshooting. In an industrial setup, resolving problems promptly and effectively is crucial for maintaining efficiency and productivity. Let’s examine how offline in-socket programming augments this vital task.
Isolation of Issues
A significant advantage of offline programming is the individual handling of each chip, separate from the main assembly line. This approach ensures that if an issue arises, it can be traced to a specific chip or batch, preventing a bottleneck in the overall assembly process, unlike in-line programming, where a single snag might trigger considerable delays as the source of the problem is tracked and rectified.
Direct Access and Control
Offline programming provides engineers with direct access to the devices being programmed. This proximity facilitates a closer inspection of issues, enabling the identification of root causes and the application of appropriate solutions. Engineers can observe the programming process in real-time, run tests, and iterate solutions within a controlled environment, thereby optimizing the troubleshooting process.
Production Line Continuity
An extraordinary benefit of offline programming is its ability to maintain production line continuity even during troubleshooting. In the event of a faulty chip, it can be extracted and replaced or reprogrammed, all without halting the assembly line. This ability to minimize disruptions plays a critical role in maintaining operational efficiency and reducing downtime.
The Power of Advanced Diagnostics
Modern offline programming systems often come equipped with advanced diagnostic tools. These provide detailed insights into potential issues, like problems within specific memory sectors or programming steps, thereby accelerating the troubleshooting process. First Articles can be produced well in advance of production volume to qualify the programming process.
Risk Mitigation as a Priority
Offline programming also plays a crucial role in risk mitigation. If a programming error surfaces or a chip proves faulty, the issue can be intercepted and addressed early in the process, preventing its propagation down the assembly line or into the final product. This early intervention saves valuable time, and resources, and can shield the company’s reputation from potential damage.
Let’s consider an automotive component manufacturer programming microcontroller devices for an advanced driver-assistance system (ADAS). If a programming issue arises during in-line production, it could disrupt the whole assembly line. However, with offline programming, any such issues can be isolated and resolved without affecting the assembly process, allowing for efficient troubleshooting.
In a nutshell, offline programming greatly enhances the efficiency and effectiveness of troubleshooting. This capability empowers manufacturers to uphold high-quality standards and minimize the fallout from any issues that might arise. Stay tuned as we delve into the fourth part of our series, where we’ll discuss how this method bolsters efficiency in the next chapter of our journey through the advantages of offline in-socket programming.
Read Part I | Read Part II
by Scott Bronstad | Jun 14, 2023 | Case Study, Technology
Unveiling the Power of Offline In-Socket Programming to Maximize Assembly Line Uptime
Part 2 – Embracing Flexibility: Unleashing the Power of Offline Programming in Streamlining Workflows
In Part I, we appreciated how offline in-socket programming offers high-quality assurance, adding significant value to the production process. Let’s now focus on another key advantage of this technique: flexibility. This vital attribute allows for seamless integration with variable production timelines and tasks, creating a harmonious production ecosystem.
Navigating Production Schedules
Unlike inline and on-board methods, offline programming does not require synchronization with the Surface Mount Technology (SMT) assembly process. This allows programming tasks to align with the existing workflow, facilitating efficient use of resources and time, whether that’s overnight or during operational downtime.
Efficiency through Batch Processing
Offline in-socket programming often supports batch processing, enabling simultaneous programming of multiple devices. This capability markedly enhances throughput and efficiency, outperforming inline or on-board methods that commonly require sequential, one-by-one processing. Other programming methods can also program multiple parts simultaneously but are limited compared to in-socket programming.
Adapting to Changes
If firmware or programming data needs updates, offline programming makes the transition smoothly, without disrupting the assembly process. This adaptability extends to device types, as offline programmers can handle a diverse range of devices.
Reducing Production Impact
Any programming issue can be resolved independently, minimizing the impact on the broader production line. This decoupling of processes ensures swift troubleshooting without compromising overall productivity.
Expanding Versatility
The capability of offline programmers to cater to different types and sizes of devices adds a layer of versatility to the production process. This means that a single offline programming system can support a variety of chips, enhancing the flexibility of production workflows.
In the case of a Contract Manufacturer (CM) serving multiple clients with diverse product lines, the programming requirements may change frequently, from microcontrollers for one client to PLDs for another. Offline programming provides the flexibility to swiftly adapt to these changes, allowing them to switch between different types of devices, firmware, or programming data with ease.
Refining Supply Chain Management
Offline programming facilitates preprogramming of devices, creating a stockpile that ensures a steady supply of programmed components. This improves the capacity to manage production schedules and respond to demand fluctuations.
Leveraging Media Transfer
Beyond programming, BPM’s Automated Programming Systems (APS) can also perform media transfers of non-programmable components. This functionality allows for the seamless transitioning of parts from JEDEC trays to smaller reels for shipping or assembly line integration, further enhancing the system’s flexibility.
In summary, the flexibility of in-socket programming provides notable operational and strategic advantages, aiding electronics manufacturers in better resource management, swift response to changes, and workflow optimization. In the next installment of our series, we’ll delve into how this method simplifies troubleshooting, bringing even more resilience and efficiency to the assembly process.
Read Part I | Enhance Supply Chain Security
by Scott Bronstad | Jun 12, 2023 | Case Study, Technology
In an era where online connectivity is increasingly becoming a staple in our day-to-day life, the concept of offline programming, specifically offline in-socket programming, can seem somewhat unconventional. However, this proven process holds significant potential to revolutionize industries, bringing numerous advantages that outshine other programming methods. This six-part article series will delve deep into the benefits of offline programming, unearthing how it paves the way for superior quality, unbridled flexibility, simplified troubleshooting, heightened efficiency, remarkable versatility, and maximal assembly line uptime.
In this comprehensive exploration, we will unfold each benefit in dedicated articles, highlighting real-world examples, dissecting relevant principles, and presenting practical insights for implementation. Regardless of whether you’re a seasoned professional seeking fresh insights or a beginner intrigued by the prospect of offline in-socket programming, this series is designed to illuminate this technique’s transformative potential. Join us as we journey through the fascinating landscape of offline programming, uncovering how this innovative approach can unlock unprecedented operational advantages in a myriad of industries.
Part 1 – Elevating Quality: How Offline Programming Mitigates Cost and Ensures Authenticity
In the world of electronic assembly, quality control is a paramount concern. Offline programming offers a revolutionary approach to guarantee the highest standard of quality, promising impeccable individual programming and verification of each chip. This sophisticated technology enables thorough validation and factory device ID checking, effectively verifying the device’s authenticity. The quality assurance this technique offers doesn’t merely serve as a reassuring stamp of approval. It’s a proactive method that not only ensures each chip’s correct functionality prior to installation but also significantly minimizes the Cost of Poor Quality (COPQ). The ripple effect of this high-quality assurance can be felt in various domains, and here is the tale it weaves:
Rework
Consider a scenario where a chip, already nestled in its place on the board, shows signs of malfunction. The consequential rework process is akin to delicate surgery. It necessitates the careful extraction and reprogramming of the chip, followed by its reinstallation. Each of these steps incurs cost, demands time, and requires the expertise of skilled technicians. Moreover, this surgical process brings with it the risk of unintentional damage to adjacent components.
In some unfortunate circumstances, the balance of cost and feasibility may tilt unfavorably, rendering rework unviable. This necessitates a hard choice – consigning the entire board to the scrap pile. Such a decision carries with it the weight of substantial material and labor costs and the regret of wasting perfectly good components sharing the same board.
The narrative deepens as we recognize the potential cascading effect of these challenges. Delays in production birthed by rework and scrap can ripple outwards, leading to missed delivery deadlines, potential financial penalties, and a blow to customer trust.
The final act in this cautionary tale involves poor quality programming rearing its head as product failures in the field. Such incidents can trigger a chain of undesirable outcomes: costly product returns, warranty claims, and perhaps most damagingly, a tarnished company reputation.
In weaving together these scenarios, it’s clear how offline in-socket programming’s quality assurance can dramatically curb the Cost of Poor Quality (COPQ). While there’s a modest rise in upfront costs due to enhanced testing and validation, the long-term fiscal savings, achieved by curtailing rework, scrap, delays, and warranty claims, are significant. In essence, device programming isn’t merely a process; it’s a forward-thinking strategy for superior quality control and cost-effective production.
Consider an Original Equipment Manufacturer (OEM) for smartphones. They need to ensure the microcontrollers embedded in their devices are programmed correctly to function optimally. By utilizing offline in-socket programming, they are able to test and verify the programming of each microcontroller before it is assembled into a smartphone, thereby reducing the risk of faulty devices and enhancing overall product quality.
As we’ve seen, offline programming’s quality assurance plays a pivotal role in cost minimization and maintaining product authenticity. Yet, this is just one facet of its potential. The next installment in our series will delve into another compelling advantage of offline programming – its inherent flexibility.
In our upcoming discussion, we will explore how this technique accommodates an array of chips and applications, readily adapts to changes, and how it empowers organizations to swiftly respond to evolving market needs. So, stay tuned for Part 2 as we dissect the flexibility of offline in-socket programming and its implications for modern electronic assembly.
Read Part II | Programming and Vertical Manufacturing | BPM API Delivers Quality and Traceability
by Scott Bronstad | May 18, 2023 | Case Study, News, Technology
Device programming has never been more essential in this digital age. These tiny chips are the brains of almost every device we use today, from smartphones to cars, and even to the most advanced medical and industrial equipment. Programming these devices, however, can be a complex and time-consuming process. That’s where BPM Microsystems comes into play, making device programming easier and more efficient than ever before. This article explores how BPM Microsystems outperforms other types of programming and brands in the market.
Device Programming: A Brief Overview
Device programming, at its core, involves loading data into a semiconductor device such as a microcontroller, programmable logic device (PLD), or memory chip. This allows the device to perform its specific functions.
There are various methods of device programming, including in-line, onboard (programming at ICT or Functional Test), and offline programming. Each of these methods has its own set of advantages and disadvantages. In-line programming, for instance, integrates directly into the manufacturing line but might slow down the production process, and is very expensive to scale up. Onboard programming can be faster once it’s set up, but it may not support all types of devices.
Offline programming, while providing flexibility in the programming process, can often be perceived as more complex due to the need for setting up and managing individual programmers. However, with the right solutions like those provided by BPM Microsystems, this process can be simplified, reducing the risk of errors and boosting efficiency.
BPM Microsystems: Simplifying Device Programming
BPM Microsystems has revolutionized the device programming process by introducing innovative, efficient, and easy-to-use solutions that stand out from the competition. Here’s how:
- Broad Device Support: BPM Microsystems’ broad device support makes it easy for businesses to program an extensive range of semiconductor devices. This means less time sourcing different programming solutions for each device type, streamlining the production process, and saving valuable resources.
- Advanced Algorithms: The advanced programming algorithms developed by BPM Microsystems not only ensure high-speed, error-free programming but also simplify the process. By continually updating their algorithms to accommodate the latest devices, BPM Microsystems removes the need for users to constantly adapt to new programming requirements, allowing for a straightforward, hassle-free programming experience.
Automated Programming Systems: The automated programming systems offered by BPM Microsystems significantly reduce manual labor; in many cases making it possible to produce several thousand devices per shift, without intensive human intervention. A single machine can often support multiple SMT lines. This not only increases efficiency but also drastically reduces the chance of human error, making the process more reliable and less stressful for operators.
- Ease of Use: BPM Microsystems’ user-friendly interface makes device programming easy even for those without extensive technical knowledge. With intuitive controls and clear instructions, users can quickly learn to navigate the system, reducing training time and enabling a faster start to production.
- Automated Z-Height Teach: A standout feature of BPM Microsystems’ solutions is the automated Z-height teach, WhisperTeach™. This greatly streamlines the job set-up process, making it up to 83% faster than traditional human + machine processes. This not only speeds up production with greater uptime but also reduces the possibility of setup errors, ensuring more accurate and efficient programming with a high first-pass yield. BPM was the first company to patent this process and is the only one that provides this game-changing technology on all of its 9th and 10th Generation automated programmers.
- Reliability and Quality: The reliability and high-quality programming of BPM Microsystems’ systems reduce the frequency of errors, making the programming process smoother and easier. Fewer errors mean less time spent troubleshooting and more time dedicated to productive tasks, enhancing overall workflow efficiency.
- Superior Customer Support: With exceptional customer support, BPM Microsystems makes it easy for clients to resolve any issues that may arise during device programming. This means that help is always readily available, reducing downtime and ensuring that the programming process can continue without significant interruptions.
In conclusion, the ease of use provided by BPM Microsystems’ solutions– whether through time savings, improved efficiency, reduced errors, or readily available support– positions them as a leading choice in the device programming industry. Their offerings make device programming not just possible, but straightforward and efficient, allowing businesses to focus on what they do best: creating innovative products powered by expertly programmed devices.
EEEEEEEEEEE AAA SSSSSSSSS YYYYYYY YYYYYY
E:::::::::E A:::A SS:::::::::S Y:::::Y Y:::::Y
E:::::::::E A:::::A S:::::SSSS:::::S Y:::::Y Y:::::YY
EE::::EEEEE A:::::::A S:::::S SSSSS Y::::::Y Y::::::Y
E:::::E A:::::::::A S::::S Y:::::Y Y::::YY
E:::::E A:::::A:::::A S:::::S Y:::::Y Y:::::Y
E:::::EEEEE A:::::A A:::::A S::::SSSS Y:::::Y:::::Y
E:::::::::E A:::::A A:::::A SS::::::SSSSS Y:::::::::Y
E:::::::::E A:::::A A:::::A SSS::::::::SS Y:::::::Y
E:::::EEEEEA:::::AAAAAAAAA:::::A SSSSSS::::S Y:::::Y
E:::::E A:::::::::::::::::::::A S::::S Y:::::Y
E:::::E A::::::AAAAAAAAAAAAA:::::AS S:::::S Y:::::Y
EE::::EEEEE:::::A A:::::ASSSSSSSSS:::::S Y:::::Y
E:::::::::E::::A A:::::AS::::::SSSSSS Y:::::Y
EEEEEEEEEEEAAAA AAAAAAASSSSSSSSSS YYYYYYY
EEEEE AA SSSSS YY YY
EE AAAA SS YY YY
EEEEE AA AA SSSSS YYY
EE AAAAAAAA SS YYY
EEEEE AA AA SSSSS YYY