How Automated Programming Aligns with Your Vertical Manufacturing Strategy
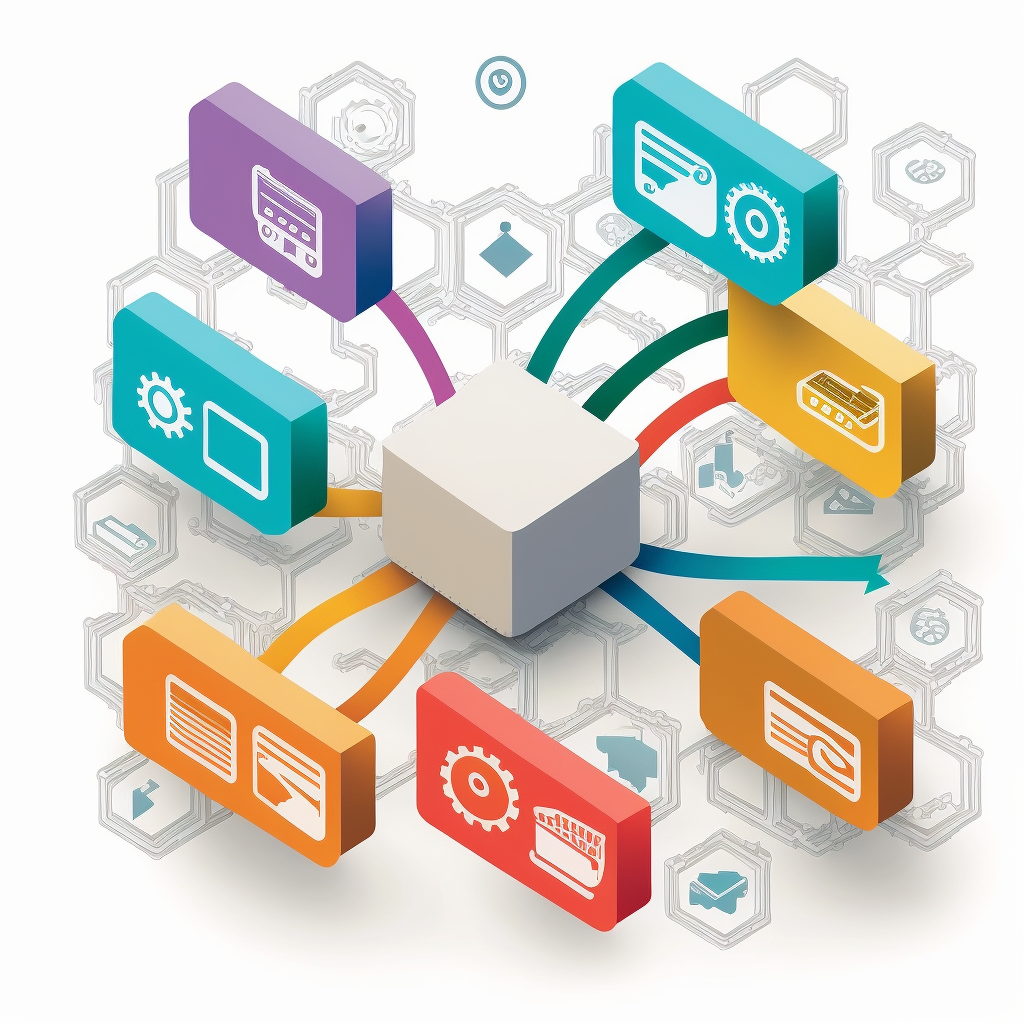
Why In-House Device Programming is the Future of Vertical Manufacturing
Learn how in-house programming can improve cost, time to market, and quality. See how an automated programming system can pay for itself compared to outsourcing.
Programmable devices power our modern world, from smartphones to computers to electric cars. But have you ever stopped to think about how these tiny chips are programmed and manufactured? In recent years, there has been a growing trend toward in-house offline device programming as part of the movement toward vertical manufacturing. In this article, we will explore the advantages of this approach, with a focus on cost per device, time to market, and quality.
Device Programming and Vertical Manufacturing
To understand the benefits of in-house programming and vertical manufacturing, let’s start with a real-world example. Imagine a company that designs and manufactures sensor assemblies for the automotive industry. The company relies on programmable devices to power its assembly, and it needs to program these devices with custom firmware before they can be integrated into the product.
In the past, the company outsourced the programming of these devices to a third-party supplier. This meant it had to wait for the supplier to program the devices and ship them back, which added time and cost to the manufacturing process. It also meant that the company had limited control over the quality of the programming and the security of its intellectual property. What’s worse, periodic and sometimes rapid design changes mean the devices in transit have to be reprogrammed, delaying production and ballooning costs.
Now, the company has invested in in-house off-line device programming. This means that it can program the devices themselves “just-in-time” using its own equipment and personnel, before integrating them into the sensor assembly. Let’s take a closer look at the advantages of this approach.
Cost per device
One of the biggest advantages of in-house off-line device programming is cost savings. By bringing the programming process in-house, companies can eliminate the markup third-party suppliers charge for their services. This can translate into significant savings, especially for companies that produce high volumes of devices.
In our example, the company can now program its own devices for a fraction of the cost of outsourcing the process. This has helped to improve its profit margins and make it more competitive in the market.
Time to market
Another critical advantage of in-house programming is faster time to market. By eliminating the need to wait for third-party suppliers, companies can speed up their manufacturing process and get their products to market more quickly. This can be especially important in fast-paced industries where timing is everything.
In our example, the company can now program its devices on demand, without having to wait for a supplier to do it for them. This has helped to reduce its lead times and ensure that it can meet customer demand in a timely manner. Plus, it reduces the likelihood of re-programming when designs change because the parts are programmed within days or hours before integration into the product.
Quality and Security
Finally, in-house programming can improve the quality of the programming and the security of the intellectual property. When a company outsources its programming to a third-party supplier, it loses some control over the quality of the programming and the security of its intellectual property. In-house programming, on the other hand, allows companies to maintain complete control over the process and ensure that their devices are programmed to the highest standards. And, they maintain complete traceability, controlling the exact quantity of devices programmed.
In our example, the company can now ensure that its devices are programmed to their exact specifications without relying on a third-party supplier. This has helped to improve the quality of its products and protect its intellectual property.
A system that pays for itself
Now, let’s take a closer look at how an offline automated programming system can pay for itself compared to outsourcing the device programming piece. An offline automated programming system can significantly reduce the cost of device programming while improving the quality and speed of the manufacturing process. By eliminating manual programming, an automated system can reduce the likelihood of human error and improve overall efficiency. In addition, the system can be programmed to automatically detect and correct errors, further reducing the likelihood of defects.
Furthermore, the advantages of vertically integrating device programming into your factory process extend beyond the cost savings and quality improvements. By having complete control over the programming process, companies can better protect their intellectual property and trade secrets. They can also more easily adapt to changes in customer demand or industry standards since they are not dependent on a third-party supplier.
In conclusion, in-house off-line device programming compliments the trend towards increased vertical manufacturing capability. Especially when paired with an automated programming system, this value-add process can offer significant advantages to companies in terms of cost savings, faster time to market, improved quality, and greater control over the manufacturing process. These benefits can help companies stay competitive in a rapidly changing market and continue to deliver innovative products to their customers while safeguarding their intellectual property.