by Scott Bronstad | Jul 7, 2023 | Technology, Video
Video: 3D Inspection System on BPM Automated Programmers
Transcript: Hi, Chip here! Introducing the revolutionary 3D Vision Inspection System. Measure critical parameters like coplanarity, pitch, bent leads, XY error, width, diameter, standoff, and tip offset with our state-of-the-art system.
Integrated with BPWin software, this system ensures higher yields and efficiency by avoiding human and manufacturing errors before production.
Customize, analyze, control, and trace your inspection process with ease using our software. Ensure optimal quality every time.
Eliminate soldering errors caused by bent leads and coplanarity issues. Our 3D Vision Inspection System precisely measures device contacts, ensuring exceptional quality control.
Seamlessly integrated into the BPM 3928 (and the BPM310) Automated Programmer, our system maximizes production yield and efficiency for programming mission-critical devices.
BPM is the only supplier of device programming solutions made exclusively in the USA, providing automotive-level 3D inspection capabilities in a smaller platform system.
Ensure the highest quality of your electronic devices, eliminate errors, and achieve unparalleled efficiency with our 3D Vision Inspection System.
BPM – Your trusted partner in advanced device programming and 3D inspection solutions.
by Scott Bronstad | Jun 28, 2023 | Case Study, Technology
Part 6 – Unveiling the Power of Offline In-Socket Programming
In the grand finale of our series examining offline in-socket programming, we delve into its profound impact on maximizing assembly line uptime, enhancing inventory management, reducing cost per device, and offering higher first-pass yield. Offline programming has the potential to avert issues that could halt the assembly line, prevent faulty devices from reaching assembly, and reduce rework, thereby ensuring continuous operation and efficient inventory management.
Maximizing Assembly Line Uptime
Offline programming separates the programming process from the assembly line, ensuring that any issues arising during programming don’t impact the assembly line directly. By preventing faulty devices from reaching the assembly process and reducing rework due to programming errors, offline programming allows the assembly line to run more smoothly. This separation enables the assembly line to continue operations even if programming needs to pause, buffering against fluctuations in demand and maximizing productivity.
Efficient Inventory Management
Offline programming allows common “blank chips” to be purchased in bulk and programmed in just-in-time to meet production requirements. If a buffer is desired, devices can be produced in advance and stored; and if necessary, to be reprogrammed for code changes. This ensures a steady supply of programmed devices, smoothing production flows, and reducing the amount of work-in-progress inventory. By guaranteeing each chip is correctly programmed before it enters assembly, offline programming also mitigates the risk of having to scrap or rework finished goods.
Reducing Cost Per Device
The cost per device, a key metric in the programming and manufacturing industries, evaluates the efficiency and cost-effectiveness of programming methods. Offline programming often allows for higher throughput, better equipment utilization, energy efficiency, minimized downtime, and reduced dependency on skilled labor, all contributing to a potentially lower cost per device.
Superior First-Pass Yield
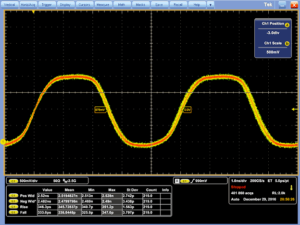
High-quality signals, Examples: Free-Running Clock (200MHz)
Programming in-socket on a dedicated system using clean waveforms leads to very high first-pass yields, reducing scrap and lowering cost per device. Bad devices can be identified upstream and returned to component suppliers for replacement or credit.
A Contract Manufacturer programming microcontrollers for an automotive client can benefit from offline programming. Preprogramming and storing chips enable them to maintain assembly line uptime, manage inventory efficiently, and buffer against sudden demand surges. The parallel programming feature also allows them to reduce the cost per device by programming multiples of the same devices concurrently.
The superior first-pass yield of offline programming can be crucial for an OEM manufacturing advanced drones. These drones use sophisticated chips that need to function perfectly. By programming in-socket on a dedicated system, they ensure very high first-pass yields, reducing the chance of scrapped units and lowering the overall cost per device.
In conclusion, this six-part series has comprehensively explored the multifaceted benefits of in-socket programming. From superior quality assurance, flexibility, and ease of troubleshooting to notable efficiency gains, exceptional versatility, and impacts on assembly line uptime and inventory management, offline programming offers significant advantages. These benefits, along with the potential for reduced costs and improved first-pass yield, make offline in-socket programming a powerful tool for electronics manufacturing.
Read Part I | Read Part II | Read Part III | Read Part IV | Read Part V
by Scott Bronstad | Jun 26, 2023 | Case Study, Technology
Part 5 – Unveiling the Power of Offline In-Socket Programming
As we delve further into the advantages of offline in-socket programming, having scrutinized aspects of quality assurance (Part I), flexibility (Part II), ease of troubleshooting (Part III), and efficiency (Part IV), it’s time to turn our gaze to yet another vital feature– versatility. Offline programming boasts an impressive capacity to handle diverse device types, sizes, and programming requirements, a feature not limited by the constraints of the assembly process. This versatility stems from several key factors.
Universal Device Compatibility
Offline programming systems are typically engineered to work with an extensive range of non-volatile memory devices. This includes Flash, EEPROM, Microcontrollers, PLD, CPLD, FPGA, and Antifuse devices. This broad compatibility allows the same system to cater to different device types, significantly enhancing flexibility.
Smooth Change Management
Offline programmers facilitate the easy implementation of changes in firmware or programming data. Any necessary update can be executed without disrupting the assembly line, a feature especially beneficial when needing to frequently switch between different products or versions.
Adaptable Socket Adapter Designs
Offline programming systems often support an array of adapter designs and sizes, making them capable of handling an extensive range of packages. These systems can be quickly adapted to various device requirements, offering a high degree of versatility.
Concurrent Programming
Offline programming systems contain multiple independent programmers and socket adapters that add fault tolerance to the system and can process multiple devices concurrently. If the programming time is short, only a few adapters are used. This capability further extends the versatility of offline programming by allowing the user to scale the system to meet the requirements of each unique job.
For an OEM producing a range of devices, from home automation gadgets to wearables, the versatility of offline programming is invaluable. With support for a wide range of non-volatile memory devices and easy handling of firmware changes, offline programming allows them to swiftly adapt to varying device requirements and changes in product versions.
Support for Advanced Programming Protocols
Offline programmers often accommodate various advanced programming protocols. This adaptability allows them to be fit for a wide range of programming tasks. Further, a range of common file types are also supported.
Reduced Production Line Dependency
Offline programming operates independently of the assembly line’s operations, making it adaptable to varying production demands and schedules.
Contrastingly, other programming methods such as in-line programming, in-circuit testing (ICT), or functional test programming may face limitations in their adaptability, ability to handle a variety of devices, or managing multiple tasks simultaneously. They are directly reliant on the production line’s schedule and must be able to meet or exceed the production line’s “beat rate.” Plus, there is downtime, labor, and a higher level of skill required to change to different device types or programming jobs..
In essence, the versatility offered by in-socket programming makes it a robust tool for electronics manufacturers, enabling them to be more flexible and responsive in their operations.
Stay tuned for the final part of our series, where we will discuss how offline programming can maximize assembly line uptime.
Read Part I | Read Part II | Read Part III | Read Part IV
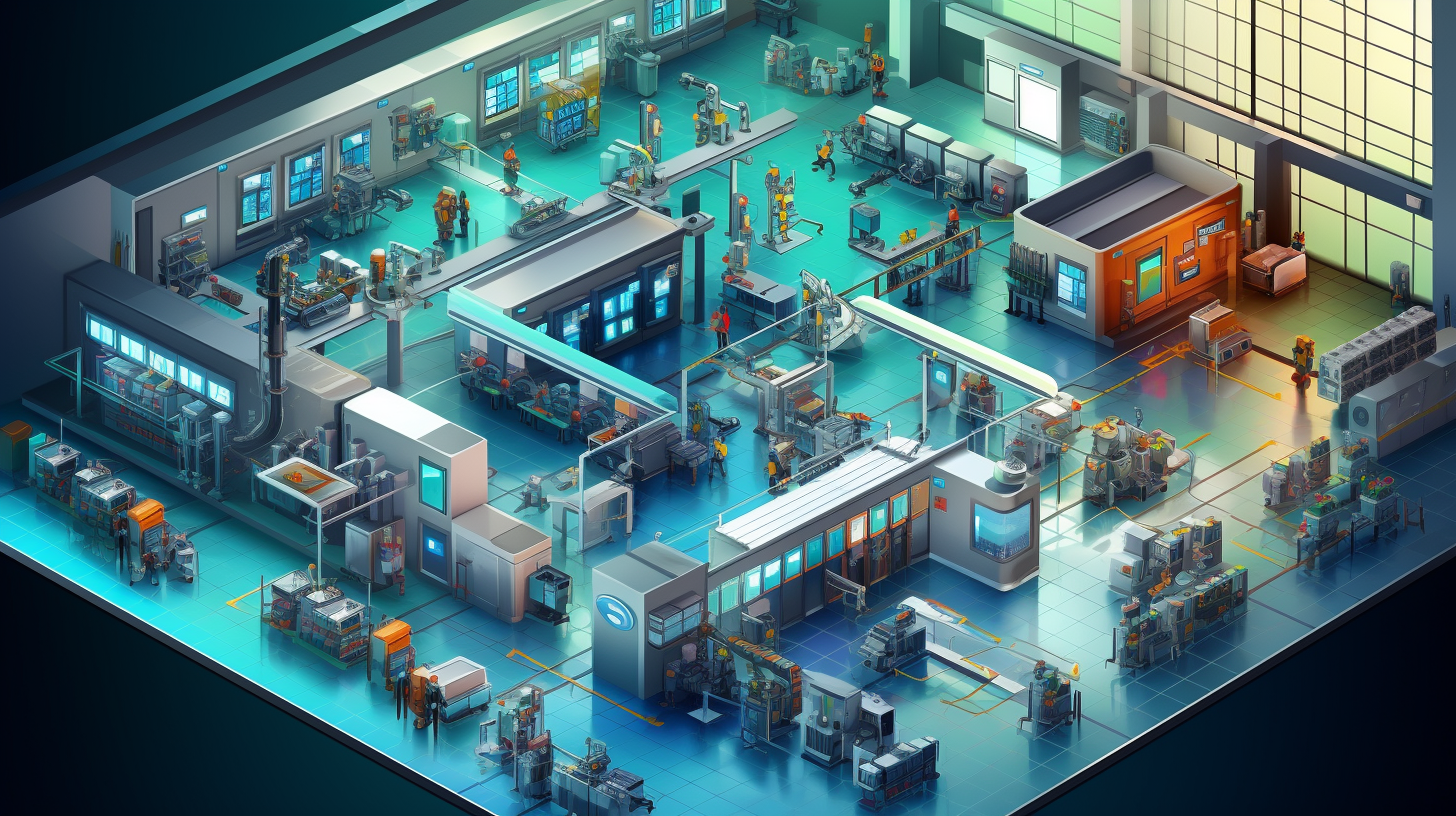
by Scott Bronstad | Jun 22, 2023 | Case Study, Technology
Part 4 – Unveiling the Power of Offline In-Socket Programming
Having journeyed through the advantages of high-quality assurance (part I), flexibility (part II), and simplified troubleshooting (part III) offered by offline in-socket programming, we now turn our attention to another salient feature – efficiency. This pivotal aspect of the offline methodology promises potential time and cost savings, alongside a range of other benefits that significantly contribute to the productivity of device programming.
Capitalizing on Scalability
A single automated programming system can program millions of devices annually. This impressive capacity often equates to supporting multiple production lines with just one machine and a part-time operator per shift.
Leveraging Batch Programming
Offline programming systems have the ability to program multiple devices concurrently, a stark contrast to in-line methods that program devices sequentially. This parallel programming approach dramatically enhances throughput, allowing more devices to be programmed within a reduced timeframe.
Minimizing Downtime
As offline programming operates independently from the main assembly line, it prevents assembly line downtime. Any arising issue during programming can be addressed independently, sparing the entire production line from interruption.
Adapting Work Schedules
The decoupling of programming from the overall production process offers greater flexibility in scheduling. This permits programming to be carried out during off-peak hours or when the assembly line is inactive, maximizing resource utilization.
Suppose a Contract Manufacturer (EMS company) operates multiple production lines producing a variety of products for various clients. Using an automated offline programming system, they can program millions of devices per year and dozens or more different “ICs,” supporting several production lines with only a part-time operator per shift. This dramatically increases throughput and reduces overall operational costs.
Reducing Rework and Scrap
Offline programming assures individual programming and verification of each chip before assembly. This approach reduces the cost and time associated with rework and scrap, thereby improving the overall efficiency of the manufacturing process.
Improving Inventory Management
The capability to program chips in advance facilitates better inventory management and smoother production scheduling. This proactive strategy can diminish stockouts and overages, boosting operational efficiency and adaptability to demand changes.
Optimizing Resource Allocation
Offline programming facilitates a more effective allocation of human and equipment resources. While programming occurs, other assembly, testing, and packaging tasks can continue in parallel, optimizing the entire manufacturing process.
Boosting Energy Efficiency
In many instances, offline programmers are more energy-efficient than their in-line counterparts. They program multiple chips simultaneously and are operational only when needed, as opposed to running continuously alongside the assembly line.
In essence, the efficiency benefits from offline in-socket programming translate into substantial cost savings and productivity improvements. This makes it an invaluable asset for electronic manufacturing companies. Join us for the next part of our series, where we will explore the versatility that offline in-socket programming brings to semiconductor manufacturing.
Read Part I | Read Part II | Read Part III
by Scott Bronstad | Jun 20, 2023 | Case Study, Technology
Part 3 – Unveiling the Power of Offline In-Socket Programming
In our exploration of device programming thus far (See Part I, See Part II), we’ve addressed how it ensures high quality and offers unparalleled flexibility in streamlining production workflows. Now, we transition to another distinct advantage – troubleshooting. In an industrial setup, resolving problems promptly and effectively is crucial for maintaining efficiency and productivity. Let’s examine how offline in-socket programming augments this vital task.
Isolation of Issues
A significant advantage of offline programming is the individual handling of each chip, separate from the main assembly line. This approach ensures that if an issue arises, it can be traced to a specific chip or batch, preventing a bottleneck in the overall assembly process, unlike in-line programming, where a single snag might trigger considerable delays as the source of the problem is tracked and rectified.
Direct Access and Control
Offline programming provides engineers with direct access to the devices being programmed. This proximity facilitates a closer inspection of issues, enabling the identification of root causes and the application of appropriate solutions. Engineers can observe the programming process in real-time, run tests, and iterate solutions within a controlled environment, thereby optimizing the troubleshooting process.
Production Line Continuity
An extraordinary benefit of offline programming is its ability to maintain production line continuity even during troubleshooting. In the event of a faulty chip, it can be extracted and replaced or reprogrammed, all without halting the assembly line. This ability to minimize disruptions plays a critical role in maintaining operational efficiency and reducing downtime.
The Power of Advanced Diagnostics
Modern offline programming systems often come equipped with advanced diagnostic tools. These provide detailed insights into potential issues, like problems within specific memory sectors or programming steps, thereby accelerating the troubleshooting process. First Articles can be produced well in advance of production volume to qualify the programming process.
Risk Mitigation as a Priority
Offline programming also plays a crucial role in risk mitigation. If a programming error surfaces or a chip proves faulty, the issue can be intercepted and addressed early in the process, preventing its propagation down the assembly line or into the final product. This early intervention saves valuable time, and resources, and can shield the company’s reputation from potential damage.
Let’s consider an automotive component manufacturer programming microcontroller devices for an advanced driver-assistance system (ADAS). If a programming issue arises during in-line production, it could disrupt the whole assembly line. However, with offline programming, any such issues can be isolated and resolved without affecting the assembly process, allowing for efficient troubleshooting.
In a nutshell, offline programming greatly enhances the efficiency and effectiveness of troubleshooting. This capability empowers manufacturers to uphold high-quality standards and minimize the fallout from any issues that might arise. Stay tuned as we delve into the fourth part of our series, where we’ll discuss how this method bolsters efficiency in the next chapter of our journey through the advantages of offline in-socket programming.
Read Part I | Read Part II
by Scott Bronstad | Jun 14, 2023 | Case Study, Technology
Unveiling the Power of Offline In-Socket Programming to Maximize Assembly Line Uptime
Part 2 – Embracing Flexibility: Unleashing the Power of Offline Programming in Streamlining Workflows
In Part I, we appreciated how offline in-socket programming offers high-quality assurance, adding significant value to the production process. Let’s now focus on another key advantage of this technique: flexibility. This vital attribute allows for seamless integration with variable production timelines and tasks, creating a harmonious production ecosystem.
Navigating Production Schedules
Unlike inline and on-board methods, offline programming does not require synchronization with the Surface Mount Technology (SMT) assembly process. This allows programming tasks to align with the existing workflow, facilitating efficient use of resources and time, whether that’s overnight or during operational downtime.
Efficiency through Batch Processing
Offline in-socket programming often supports batch processing, enabling simultaneous programming of multiple devices. This capability markedly enhances throughput and efficiency, outperforming inline or on-board methods that commonly require sequential, one-by-one processing. Other programming methods can also program multiple parts simultaneously but are limited compared to in-socket programming.
Adapting to Changes
If firmware or programming data needs updates, offline programming makes the transition smoothly, without disrupting the assembly process. This adaptability extends to device types, as offline programmers can handle a diverse range of devices.
Reducing Production Impact
Any programming issue can be resolved independently, minimizing the impact on the broader production line. This decoupling of processes ensures swift troubleshooting without compromising overall productivity.
Expanding Versatility
The capability of offline programmers to cater to different types and sizes of devices adds a layer of versatility to the production process. This means that a single offline programming system can support a variety of chips, enhancing the flexibility of production workflows.
In the case of a Contract Manufacturer (CM) serving multiple clients with diverse product lines, the programming requirements may change frequently, from microcontrollers for one client to PLDs for another. Offline programming provides the flexibility to swiftly adapt to these changes, allowing them to switch between different types of devices, firmware, or programming data with ease.
Refining Supply Chain Management
Offline programming facilitates preprogramming of devices, creating a stockpile that ensures a steady supply of programmed components. This improves the capacity to manage production schedules and respond to demand fluctuations.
Leveraging Media Transfer
Beyond programming, BPM’s Automated Programming Systems (APS) can also perform media transfers of non-programmable components. This functionality allows for the seamless transitioning of parts from JEDEC trays to smaller reels for shipping or assembly line integration, further enhancing the system’s flexibility.
In summary, the flexibility of in-socket programming provides notable operational and strategic advantages, aiding electronics manufacturers in better resource management, swift response to changes, and workflow optimization. In the next installment of our series, we’ll delve into how this method simplifies troubleshooting, bringing even more resilience and efficiency to the assembly process.
Read Part I | Enhance Supply Chain Security