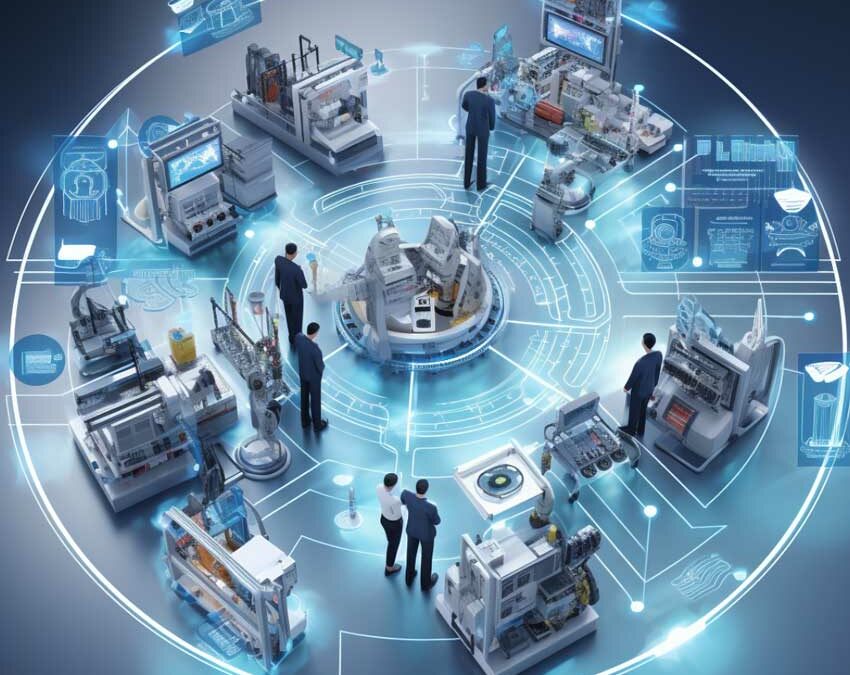
Revolutionizing Device Programming: How BPM Microsystems Tackles OEM Challenges
Device Programming Pain Points for OEMs, and How BPM’s Solutions Make Device Programming Fast, Easy, and Affordable
Semiconductor device programming is a crucial step in the manufacturing process, one where Original Equipment Manufacturers (OEMs) often encounter significant hurdles. These challenges can impact everything from production timelines and costs to quality control and product compatibility. If you’re an OEM looking for innovative ways to transform these obstacles into competitive strengths, understanding these issues and the available solutions is essential. In this examination, we’ll explore the common pain points in device programming and highlight how emerging technologies and approaches are reshaping the landscape, offering OEMs new opportunities for efficiency, quality, and flexibility.
Manual and Time-Consuming Programming
In the traditional device programming environment, manual operations often form a critical part of the process. This manual programming methodology has far-reaching implications, impacting various aspects of production and overall efficiency.
Bottlenecks in Production
An OEM producing automotive controllers, for example, requires an efficient programming process for each component. Manually handling components can create a significant bottleneck, slowing down the entire production line. If an employee has to physically load, program, and then unload each component, the time and effort required quickly accumulate, leading to slow production throughput.
Human Errors and Quality Control
Many manufacturers have quality standards beyond Six Sigma. With manual programming, the risk of human error also increases. Whether it’s misalignment, incorrect data input, or inconsistency between batches, the errors can lead to functional defects in the final product. Quality control becomes a significant challenge, and the repercussions can be costly both in terms of time and resources.
Labor Costs and Scalability
Relying on human labor for programming tasks means that scaling up production might necessitate hiring more skilled personnel. This not only drives up labor costs but also adds complexity to the hiring and training processes. For growing businesses or those with fluctuating production needs, this can become a significant challenge.
BPM’s Solutions
BPM Microsystems’ automated programming systems provide a robust solution to these challenges. By integrating automation into the programming process, several key benefits emerge:
- Increased Throughput: Automation dramatically reduces the time taken for each programming cycle compared to manual programmers. When factoring in the time-savings in set-ups and inefficiencies of human handling, BPM automated programmers shave up to 83% compared to other competitive automated systems requiring a trained operator set-up. This means the BPM system is available for actual production for additional hours per shift.
- Consistent Quality: With automation, every programming task is performed with the same level of precision. The risk of human error is minimized, leading to consistent quality across every batch. Our machines handle components accurately, to within 15 microns each time.
- Reduced Labor Costs: Automation allows OEMs to scale up or down without a corresponding change in labor costs. This offers flexibility and can be a crucial advantage in competitive or rapidly changing markets. And, machines are intended to be set up to operate unattended for long periods of time.
- Faster Time-to-Market: With increased efficiency and reduced production times, products can reach the market faster, giving OEMs a competitive edge.
OEM Impact
The transformation from manual to automated programming is not just theoretical. BPM Microsystems’ solutions have proven applications across various industries, from automotive to consumer electronics. Companies that have adopted these automated systems have reported significant improvements in production speed, cost, efficiency, and overall product quality.
High Programming Costs
High programming costs have long been a concern for Original Equipment Manufacturers (OEMs), affecting their budget allocation, resource management, and overall profitability. Several factors contribute to these high costs, and BPM Microsystems has targeted solutions to address them.
In-House Programming Expenses
OEMs opting to handle programming in-house often face various costs that quickly add up. These may include:
- Equipment Costs: The hardware necessary for programming can be expensive, particularly if specialized or cutting-edge technology is required.
- Labor Costs: Skilled technicians are often needed to operate the equipment, leading to higher wage expenses.
- Maintenance and Upkeep: Regular maintenance and occasional upgrades are necessary to keep the equipment functioning optimally, incurring further costs.
- Scalability Challenges: In-house programming in-line or at test can also make it difficult to scale operations up or down efficiently as market demands change.
Outsourcing Programming
Alternatively, outsourcing programming tasks to third-party vendors can also be costly. This approach introduces its own challenges:
- Vendor Costs: Vendors might charge high fees for their specialized services, particularly for complex or large-scale tasks.
- Quality Control: Managing quality can be more challenging when outsourcing, potentially leading to costly mistakes or rework.
- Logistical Challenges: Shipping devices to and from vendors adds both time and expense to the process.
- Intellectual Property Concerns: Working with third-party vendors may introduce risks related to intellectual property theft or mishandling.
BPM’s Solutions
BPM Microsystems provides a multifaceted approach to combat these high programming costs that offers significant benefits:
- Cost-Effective Equipment: BPM’s solutions are designed with affordability in mind, providing state-of-the-art technology without the exorbitant price tag. More importantly, BPM equipment return on investment (ROI) is often measured in weeks, not years.
- Automation: Automated systems reduce the need for extensive manual labor, cutting down on labor costs.
- Quality Assurance: Advanced quality control features ensure accurate programming, reducing the risk of errors and rework.
- Scalable Solutions: BPM’s programming systems are designed to scale with your needs, offering flexibility without substantial incremental costs. Because programming is separated from the SMT line, production can scale without causing bottlenecks.
Consider a company producing smart home devices that must navigate constant updates and various programming tasks. By adopting BPM Microsystems’ cost-effective solutions, the manufacturer can minimize both equipment and labor costs, while maintaining quality control. This real-world application showcases how BPM’s systems support cost-saving strategies without compromising on performance or quality.
Limited Device Support
The issue of limited device support in semiconductor device programming is a complex and multifaceted problem. With the ever-growing range of programmable devices on the market, OEMs can find themselves struggling to maintain compatibility and integration with their existing systems. This challenge extends across various aspects of the manufacturing process, and BPM Microsystems’ solutions are poised to address them.
Compatibility Issues
- Multiple Standards and Formats: Devices come in various formats, standards, and technologies. This diversity can make it challenging for OEMs to maintain support for all devices, leading to integration difficulties.
- Vendor-Specific Limitations: Some programming systems might be restricted to specific manufacturers or device families, limiting flexibility in choosing components.
- Technology Evolution: As technology progresses, new devices are introduced with different requirements, making continuous support a moving target.
Impact on Manufacturing
- Production Delays: Limited support can cause significant delays in production if new or different devices are introduced that aren’t compatible with existing programming systems.
- Increased Complexity: Managing multiple programming systems for various devices adds complexity to the manufacturing process, potentially leading to mistakes or inefficiencies.
- Inability to Adapt: Limited device support might make it challenging for OEMs to adapt to new market demands or innovations, potentially leaving them behind the competition.
BPM’s Solutions
BPM Microsystems provides robust solutions to these challenges through its extensive library of supported devices and a commitment to continuous adaptation.
- Extensive Device Library: With over 70,000 supported devices, BPM Microsystems ensures broad compatibility across various standards and formats. This vast library simplifies integration and ensures that OEMs can work with a wide array of devices without concern for compatibility-related interruptions.
- Continuous Updates: BPM stays abreast of technology evolution by regularly updating its supported devices list. This ensures that the programming systems remain compatible with the latest devices and technologies.
- Customized Support: For unique or specialized requirements, BPM offers customization options, ensuring that specific device needs can be met without compromising efficiency or functionality.
Telecommunications Example
Imagine a telecommunications equipment manufacturer that needs to integrate various programmable components into its products. Different microcontrollers, flash memories, and FPGAs are sourced from multiple suppliers, each with its unique programming requirements. By leveraging BPM Microsystems’ solutions with an extensive device library, the manufacturer can smoothly integrate these different components without worrying about compatibility issues. This not only streamlines the manufacturing process but also offers the flexibility to innovate and adapt to market trends.
Inconsistent Programming Quality
Inconsistent programming quality can have serious ramifications for OEMs, affecting both the reliability of products and the reputation of the brand. This challenge encompasses various facets of the programming process, from algorithm efficiency to quality control mechanisms.
Causes of Inconsistent Quality
- Human Error: Manual processes may introduce variations in quality due to mistakes or inconsistencies in handling.
- Inadequate Algorithms: Subpar or outdated algorithms might lead to errors or inconsistencies during the programming phase.
- Lack of Quality Control Measures: Without proper quality control mechanisms, inconsistencies might go undetected until they lead to failures in the field.
- Environmental Factors: Fluctuations in temperature, humidity, or power supply can introduce variations in programming quality.
Consequences
- Device Failures: Inconsistent programming quality can lead to device malfunctions, reducing the reliability of the end products.
- Product Recalls: Serious inconsistencies may necessitate product recalls, an expensive and reputation-damaging process.
- Loss of Customer Trust: Repeated quality issues can erode customer trust, potentially leading to a decrease in market share.
- Increased Costs: Dealing with quality inconsistencies can introduce additional costs in terms of rework, testing, and support.
BPM’s Solutions
BPM Microsystems’ approach to ensuring consistent programming quality involves a combination of technological innovation and rigorous quality control:
- Advanced Algorithms: By employing cutting-edge algorithms, BPM ensures accurate and efficient programming, minimizing the risk of inconsistencies.
- Quality Control Features: BPM’s programming systems come with robust quality control features that automatically detect and reject parts that do not pass. 3D inspection, automotive-level detection of mechanical defects/errors, is also available on most systems. After programming, the 3D vision system measures the contacts of devices before placed in output media to ensure quality. Manufacturers achieve the highest production yield and process efficiency for programming mission-critical devices by integrating 3D coplanarity vision inspection.
- Environmentally Stable Systems: BPM’s solutions are designed to work efficiently across a range of environmental conditions, ensuring that external factors don’t affect programming quality. Systems need to be in climate-controlled environments but do not require clean room standards.
- End-to-End Monitoring: BPM provides tools to monitor the entire programming process, giving operators insight into the quality of the process and enabling timely intervention if needed.
Medical Device Example
Consider a medical equipment manufacturer where accurate programming is not just about efficiency; it’s a matter of patient safety. Inconsistent programming quality in a critical device like a pacemaker could lead to life-threatening malfunctions. By leveraging BPM Microsystems’ advanced algorithms and quality control features, this manufacturer can guarantee accurate and reliable programming. This ensures that the pacemakers are not only consistent in quality but also meet the stringent safety standards required in medical applications.
Inconsistent programming quality is a complex issue with the potential to affect nearly every aspect of a product’s life cycle. From manufacturing efficiency to customer satisfaction, the ripple effects of quality inconsistencies can be far-reaching. BPM Microsystems’ targeted solutions address this challenge head-on, providing the tools and technologies needed to ensure accurate, consistent, and reliable programming. Whether in safety-critical applications like medical devices or in highly competitive consumer markets, BPM’s commitment to quality turns a potential vulnerability into a consistent strength for OEMs. The comprehensive approach to quality assurance fosters trust, reliability, and success in today’s demanding manufacturing environment.
Complex and Rigid Software
In the dynamic world of device programming, complex and rigid software can be a substantial obstacle for OEMs. Traditional programming software might be challenging to learn, hard to customize, and inflexible in integrating with other systems like Manufacturing Execution Systems (MES). Let’s explore this issue in-depth and understand how BPM Microsystems’ solutions, including their Application Programming Interface (API), address these challenges.
Challenges with Traditional Programming Software
- Steep Learning Curve: Conventional programming software can be difficult to learn, especially for non-technical personnel, resulting in longer training periods and potential mistakes.
- Integration Difficulties: Connecting traditional programming systems to other essential platforms like MES can be a complex and time-consuming task.
- Incompatibility with New Technologies: Rigid software might not adapt well to technological advancements, leading to obsolescence or the need for costly upgrades.
Impact on Operations
These challenges translate into tangible operational problems:
- Delayed Onboarding: Training employees on complex systems can delay the onboarding process, affecting production schedules.
- Operational Inefficiencies: Lack of customization and integration can lead to disjointed workflows and inefficiencies in the manufacturing process.
- Increased Costs: Investing in training, customization, and integration can drive up costs.
BPM’s Solutions: Emphasizing Flexibility and Integration
BPM Microsystems offers solutions designed to overcome these challenges through user-friendly software and seamless integration capabilities:
- User-Friendly Interface: BPM’s software is designed with the user in mind, offering an intuitive and straightforward interface that minimizes training time and simplifies daily operations. For users of BPM manual systems, the transition to automated solutions is seamless. The same software, BPWin, is used for both platforms, with a few additional operations and customization.
- Customizable Workflows: The flexibility to tailor the programming process to specific needs enables OEMs to align the system with their unique requirements, enhancing efficiency.
- BPM’s API for MES Integration: BPM’s BPWin Application Programming Interface (API) makes it easy to connect to a company’s MES. This ensures that data flows smoothly between programming and manufacturing systems, facilitating real-time monitoring, quality control, and process optimization.
- Future-Proof Design: Designed with adaptability in mind, BPM’s solutions can grow and evolve with technological advancements, ensuring long-term value.
OEM Challenges
Consider a global electronics manufacturer that utilizes complex supply chain and manufacturing processes. Integration between programming systems and MES is vital for real-time monitoring and streamlined workflows. Traditional software’s rigidity was a bottleneck until they implemented BPM Microsystems’ solutions. Through BPM’s user-friendly interface and API, they were able to easily connect programming systems with their MES, enhancing process visibility and overall efficiency.
Complex and rigid software in device programming doesn’t just create technical challenges; it can impede an OEM’s agility, efficiency, and competitiveness. BPM Microsystems’ approach to software design addresses these pain points by emphasizing user-friendliness, customization, and seamless integration through its API. Connecting to the company MES becomes a straightforward process, breaking down barriers and fostering a more cohesive and efficient manufacturing environment. From reducing training time to enabling real-time data flow, BPM’s solutions transform what could be a constraint into an enabler of success in the ever-evolving manufacturing landscape. Whether an OEM is a large multinational corporation or a nimble startup, BPM’s focus on flexibility and integration offers tangible benefits that align with modern manufacturing needs.
Conclusion
BPM Microsystems has emerged as a problem-solver in the device programming industry by offering solutions to some of the most persistent challenges. Through automation, cost-efficient systems, extensive device support, quality assurance, and user-friendly interfaces, BPM is making device programming not just fast and affordable, but also more reliable and efficient. By aligning solutions with industry needs, BPM Microsystems is helping OEMs enhance their competitiveness and achieve greater success in today’s dynamic and demanding electronics manufacturing environment.