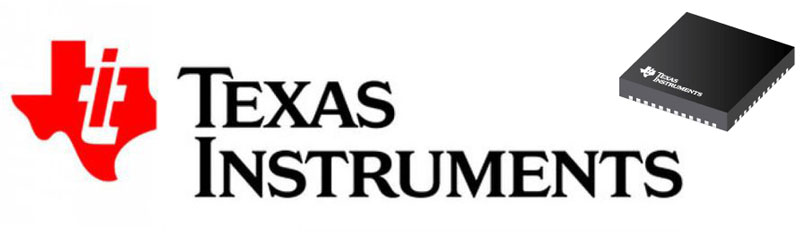
TI Bluetooth MCU Released in Latest BPWin Update
TI Bluetooth MCU Released in Latest BPWin Update
First-in-Family Support for Texas Instruments CC2640R2LRHBR Bluetooth 2.4 GHz wireless microcontroller (MCU)
BPM is pleased to announce 9th Generation support for the Texas Instruments Bluetooth microcontroller CC2640R2LRHBR. It is an ideal candidate for automation, industrial, medical, sports, and gaming applications. The socket used to program the device, FVE4ASMR32QFNZD, is fully compatible with BPM’s 9th Gen manual programmers (2900 and 2900L) and automated programming systems (3901, 3928, and 4910).
Applications
-
Home and Building Automation
- Electronic Point Of Sale (EPOS)
- Health and Medical
- Sports and Fitness
- Gaming
The CC2640R2L Family
CC2640R2L family of devices is a 2.4 GHz wireless microcontroller (MCU) supporting Bluetooth ® 5.1 Low Energy and Proprietary 2.4 GHz applications. The device is optimized for low-power wireless communication and advanced sensing in medical, asset tracking, personal electronics, retail automation, and building automation markets, and applications where industrial performance is required. The highlighted features of this device include:
- Support for Bluetooth ® 5.1 features: LE Coded PHYs (Long Range), LE 2-Mbit PHY (High Speed), Advertising Extensions, Multiple Advertisement Sets, as well as backward compatibility and support for key features from the Bluetooth ® 5.0 and earlier Low Energy specifications.
- Fully-qualified Bluetooth ® 5.1 software protocol stack included with the SimpleLink™ CC2640R2 Software Development Kit (SDK) for developing applications on the powerful Arm® Cortex®-M3 processor.
- Flash-based architecture with Cryptographic Accelerators and provision for on-chip and off-chip OAD.
- Dedicated software-controlled radio controller (Arm® Cortex®-M0) providing flexible low-power RF transceiver capability to support multiple physical layers and RF standards.
- Excellent radiosensitivity and robustness (selectivity and blocking) performance for Bluetooth ® Low Energy (-97 dBm for 1Mbps PHY).
The CC2640R2L device is part of the SimpleLink™ microcontroller (MCU) platform, which consists of Wi-Fi, Bluetooth Low Energy, Thread, ZigBee, Sub-1 GHz MCUs, and host MCUs that all share a common, easy-to-use development environment with a single core software development kit (SDK) and rich toolset. A one-time integration of the SimpleLink™ platform enables you to add any combination of the portfolio’s devices into your design, allowing 100 percent code reuse when your design requirements change. For more information, visit the SimpleLink™ MCU platform.
Bluetooth MCU Specifications:
Manufacturer: Texas Instruments
- Part Number: CC2640R2LRHBR
- 8-bit Bytes: 131072
- Memory Regions: 0h-1 EFFFh; 1 F000h-1 FFFFh
- Vcc(program): 3.3
- Electrical Erase: Yes
- Set programming: Yes
- Package: QFN(32)
- Security: Cryptographic acceleration, Debug security, Device identity, Software IP protection
- 9th Gen Socket Solution: FVE4ASMR32QFNZD
- Available on BPM’s Process software BPWin Versions released after 05/13/2021
TI Support
As of publication, BPM has the only supported solution for this particular device. Texas Instruments devices supported by BPM Programmers are currently 1,423*.
Supported* | Socket | Price | |
Data I/O | No | ||
Elnec | No | ||
DediProg | No | ||
Xeltek | No | ||
BPM | Yes | FVE4ASMR32QFNZD | $657.00 |
*As of publication
9th Gen
9th Generation Site Technology delivers the fastest programming times, 2 to 9 times faster for flash devices. Vector Engine™ Co-processing with BitBlast offers the fastest programming speeds in the industry, vastly increasing throughput for automotive MCUs.
BPWin Software Support
In order to fully take advantage of new device support from BPM Microsystems, you’ll need a version of BPWin after 05/13/2021. New programmers come with one year of software support; if your software contract has lapsed, please contact Inside Sales to take advantage of daily additions and improvements in device support.