by Scott Bronstad | Aug 25, 2023 | Case Study, How To, News, Technology
Device Programming Pain Points for OEMs, and How BPM’s Solutions Make Device Programming Fast, Easy, and Affordable
Semiconductor device programming is a crucial step in the manufacturing process, one where Original Equipment Manufacturers (OEMs) often encounter significant hurdles. These challenges can impact everything from production timelines and costs to quality control and product compatibility. If you’re an OEM looking for innovative ways to transform these obstacles into competitive strengths, understanding these issues and the available solutions is essential. In this examination, we’ll explore the common pain points in device programming and highlight how emerging technologies and approaches are reshaping the landscape, offering OEMs new opportunities for efficiency, quality, and flexibility.
Manual and Time-Consuming Programming
In the traditional device programming environment, manual operations often form a critical part of the process. This manual programming methodology has far-reaching implications, impacting various aspects of production and overall efficiency.
Bottlenecks in Production
An OEM producing automotive controllers, for example, requires an efficient programming process for each component. Manually handling components can create a significant bottleneck, slowing down the entire production line. If an employee has to physically load, program, and then unload each component, the time and effort required quickly accumulate, leading to slow production throughput.
Human Errors and Quality Control
Many manufacturers have quality standards beyond Six Sigma. With manual programming, the risk of human error also increases. Whether it’s misalignment, incorrect data input, or inconsistency between batches, the errors can lead to functional defects in the final product. Quality control becomes a significant challenge, and the repercussions can be costly both in terms of time and resources.
Labor Costs and Scalability
Relying on human labor for programming tasks means that scaling up production might necessitate hiring more skilled personnel. This not only drives up labor costs but also adds complexity to the hiring and training processes. For growing businesses or those with fluctuating production needs, this can become a significant challenge.
BPM’s Solutions
BPM Microsystems’ automated programming systems provide a robust solution to these challenges. By integrating automation into the programming process, several key benefits emerge:
- Increased Throughput: Automation dramatically reduces the time taken for each programming cycle compared to manual programmers. When factoring in the time-savings in set-ups and inefficiencies of human handling, BPM automated programmers shave up to 83% compared to other competitive automated systems requiring a trained operator set-up. This means the BPM system is available for actual production for additional hours per shift.
- Consistent Quality: With automation, every programming task is performed with the same level of precision. The risk of human error is minimized, leading to consistent quality across every batch. Our machines handle components accurately, to within 15 microns each time.
- Reduced Labor Costs: Automation allows OEMs to scale up or down without a corresponding change in labor costs. This offers flexibility and can be a crucial advantage in competitive or rapidly changing markets. And, machines are intended to be set up to operate unattended for long periods of time.
- Faster Time-to-Market: With increased efficiency and reduced production times, products can reach the market faster, giving OEMs a competitive edge.
OEM Impact
The transformation from manual to automated programming is not just theoretical. BPM Microsystems’ solutions have proven applications across various industries, from automotive to consumer electronics. Companies that have adopted these automated systems have reported significant improvements in production speed, cost, efficiency, and overall product quality.
High Programming Costs
High programming costs have long been a concern for Original Equipment Manufacturers (OEMs), affecting their budget allocation, resource management, and overall profitability. Several factors contribute to these high costs, and BPM Microsystems has targeted solutions to address them.
In-House Programming Expenses
OEMs opting to handle programming in-house often face various costs that quickly add up. These may include:
- Equipment Costs: The hardware necessary for programming can be expensive, particularly if specialized or cutting-edge technology is required.
- Labor Costs: Skilled technicians are often needed to operate the equipment, leading to higher wage expenses.
- Maintenance and Upkeep: Regular maintenance and occasional upgrades are necessary to keep the equipment functioning optimally, incurring further costs.
- Scalability Challenges: In-house programming in-line or at test can also make it difficult to scale operations up or down efficiently as market demands change.
Outsourcing Programming
Alternatively, outsourcing programming tasks to third-party vendors can also be costly. This approach introduces its own challenges:
- Vendor Costs: Vendors might charge high fees for their specialized services, particularly for complex or large-scale tasks.
- Quality Control: Managing quality can be more challenging when outsourcing, potentially leading to costly mistakes or rework.
- Logistical Challenges: Shipping devices to and from vendors adds both time and expense to the process.
- Intellectual Property Concerns: Working with third-party vendors may introduce risks related to intellectual property theft or mishandling.
BPM’s Solutions
BPM Microsystems provides a multifaceted approach to combat these high programming costs that offers significant benefits:
- Cost-Effective Equipment: BPM’s solutions are designed with affordability in mind, providing state-of-the-art technology without the exorbitant price tag. More importantly, BPM equipment return on investment (ROI) is often measured in weeks, not years.
- Automation: Automated systems reduce the need for extensive manual labor, cutting down on labor costs.
- Quality Assurance: Advanced quality control features ensure accurate programming, reducing the risk of errors and rework.
- Scalable Solutions: BPM’s programming systems are designed to scale with your needs, offering flexibility without substantial incremental costs. Because programming is separated from the SMT line, production can scale without causing bottlenecks.
Consider a company producing smart home devices that must navigate constant updates and various programming tasks. By adopting BPM Microsystems’ cost-effective solutions, the manufacturer can minimize both equipment and labor costs, while maintaining quality control. This real-world application showcases how BPM’s systems support cost-saving strategies without compromising on performance or quality.
Limited Device Support
The issue of limited device support in semiconductor device programming is a complex and multifaceted problem. With the ever-growing range of programmable devices on the market, OEMs can find themselves struggling to maintain compatibility and integration with their existing systems. This challenge extends across various aspects of the manufacturing process, and BPM Microsystems’ solutions are poised to address them.
Compatibility Issues
- Multiple Standards and Formats: Devices come in various formats, standards, and technologies. This diversity can make it challenging for OEMs to maintain support for all devices, leading to integration difficulties.
- Vendor-Specific Limitations: Some programming systems might be restricted to specific manufacturers or device families, limiting flexibility in choosing components.
- Technology Evolution: As technology progresses, new devices are introduced with different requirements, making continuous support a moving target.
Impact on Manufacturing
- Production Delays: Limited support can cause significant delays in production if new or different devices are introduced that aren’t compatible with existing programming systems.
- Increased Complexity: Managing multiple programming systems for various devices adds complexity to the manufacturing process, potentially leading to mistakes or inefficiencies.
- Inability to Adapt: Limited device support might make it challenging for OEMs to adapt to new market demands or innovations, potentially leaving them behind the competition.
BPM’s Solutions
BPM Microsystems provides robust solutions to these challenges through its extensive library of supported devices and a commitment to continuous adaptation.
- Extensive Device Library: With over 70,000 supported devices, BPM Microsystems ensures broad compatibility across various standards and formats. This vast library simplifies integration and ensures that OEMs can work with a wide array of devices without concern for compatibility-related interruptions.
- Continuous Updates: BPM stays abreast of technology evolution by regularly updating its supported devices list. This ensures that the programming systems remain compatible with the latest devices and technologies.
- Customized Support: For unique or specialized requirements, BPM offers customization options, ensuring that specific device needs can be met without compromising efficiency or functionality.
Telecommunications Example
Imagine a telecommunications equipment manufacturer that needs to integrate various programmable components into its products. Different microcontrollers, flash memories, and FPGAs are sourced from multiple suppliers, each with its unique programming requirements. By leveraging BPM Microsystems’ solutions with an extensive device library, the manufacturer can smoothly integrate these different components without worrying about compatibility issues. This not only streamlines the manufacturing process but also offers the flexibility to innovate and adapt to market trends.
Inconsistent Programming Quality
Inconsistent programming quality can have serious ramifications for OEMs, affecting both the reliability of products and the reputation of the brand. This challenge encompasses various facets of the programming process, from algorithm efficiency to quality control mechanisms.
Causes of Inconsistent Quality
- Human Error: Manual processes may introduce variations in quality due to mistakes or inconsistencies in handling.
- Inadequate Algorithms: Subpar or outdated algorithms might lead to errors or inconsistencies during the programming phase.
- Lack of Quality Control Measures: Without proper quality control mechanisms, inconsistencies might go undetected until they lead to failures in the field.
- Environmental Factors: Fluctuations in temperature, humidity, or power supply can introduce variations in programming quality.
Consequences
- Device Failures: Inconsistent programming quality can lead to device malfunctions, reducing the reliability of the end products.
- Product Recalls: Serious inconsistencies may necessitate product recalls, an expensive and reputation-damaging process.
- Loss of Customer Trust: Repeated quality issues can erode customer trust, potentially leading to a decrease in market share.
- Increased Costs: Dealing with quality inconsistencies can introduce additional costs in terms of rework, testing, and support.
BPM’s Solutions
BPM Microsystems’ approach to ensuring consistent programming quality involves a combination of technological innovation and rigorous quality control:
- Advanced Algorithms: By employing cutting-edge algorithms, BPM ensures accurate and efficient programming, minimizing the risk of inconsistencies.
- Quality Control Features: BPM’s programming systems come with robust quality control features that automatically detect and reject parts that do not pass. 3D inspection, automotive-level detection of mechanical defects/errors, is also available on most systems. After programming, the 3D vision system measures the contacts of devices before placed in output media to ensure quality. Manufacturers achieve the highest production yield and process efficiency for programming mission-critical devices by integrating 3D coplanarity vision inspection.
- Environmentally Stable Systems: BPM’s solutions are designed to work efficiently across a range of environmental conditions, ensuring that external factors don’t affect programming quality. Systems need to be in climate-controlled environments but do not require clean room standards.
- End-to-End Monitoring: BPM provides tools to monitor the entire programming process, giving operators insight into the quality of the process and enabling timely intervention if needed.
Medical Device Example
Consider a medical equipment manufacturer where accurate programming is not just about efficiency; it’s a matter of patient safety. Inconsistent programming quality in a critical device like a pacemaker could lead to life-threatening malfunctions. By leveraging BPM Microsystems’ advanced algorithms and quality control features, this manufacturer can guarantee accurate and reliable programming. This ensures that the pacemakers are not only consistent in quality but also meet the stringent safety standards required in medical applications.
Inconsistent programming quality is a complex issue with the potential to affect nearly every aspect of a product’s life cycle. From manufacturing efficiency to customer satisfaction, the ripple effects of quality inconsistencies can be far-reaching. BPM Microsystems’ targeted solutions address this challenge head-on, providing the tools and technologies needed to ensure accurate, consistent, and reliable programming. Whether in safety-critical applications like medical devices or in highly competitive consumer markets, BPM’s commitment to quality turns a potential vulnerability into a consistent strength for OEMs. The comprehensive approach to quality assurance fosters trust, reliability, and success in today’s demanding manufacturing environment.
Complex and Rigid Software
In the dynamic world of device programming, complex and rigid software can be a substantial obstacle for OEMs. Traditional programming software might be challenging to learn, hard to customize, and inflexible in integrating with other systems like Manufacturing Execution Systems (MES). Let’s explore this issue in-depth and understand how BPM Microsystems’ solutions, including their Application Programming Interface (API), address these challenges.
Challenges with Traditional Programming Software
- Steep Learning Curve: Conventional programming software can be difficult to learn, especially for non-technical personnel, resulting in longer training periods and potential mistakes.
- Integration Difficulties: Connecting traditional programming systems to other essential platforms like MES can be a complex and time-consuming task.
- Incompatibility with New Technologies: Rigid software might not adapt well to technological advancements, leading to obsolescence or the need for costly upgrades.
Impact on Operations
These challenges translate into tangible operational problems:
- Delayed Onboarding: Training employees on complex systems can delay the onboarding process, affecting production schedules.
- Operational Inefficiencies: Lack of customization and integration can lead to disjointed workflows and inefficiencies in the manufacturing process.
- Increased Costs: Investing in training, customization, and integration can drive up costs.
BPM’s Solutions: Emphasizing Flexibility and Integration
BPM Microsystems offers solutions designed to overcome these challenges through user-friendly software and seamless integration capabilities:
- User-Friendly Interface: BPM’s software is designed with the user in mind, offering an intuitive and straightforward interface that minimizes training time and simplifies daily operations. For users of BPM manual systems, the transition to automated solutions is seamless. The same software, BPWin, is used for both platforms, with a few additional operations and customization.
- Customizable Workflows: The flexibility to tailor the programming process to specific needs enables OEMs to align the system with their unique requirements, enhancing efficiency.
- BPM’s API for MES Integration: BPM’s BPWin Application Programming Interface (API) makes it easy to connect to a company’s MES. This ensures that data flows smoothly between programming and manufacturing systems, facilitating real-time monitoring, quality control, and process optimization.
- Future-Proof Design: Designed with adaptability in mind, BPM’s solutions can grow and evolve with technological advancements, ensuring long-term value.
OEM Challenges
Consider a global electronics manufacturer that utilizes complex supply chain and manufacturing processes. Integration between programming systems and MES is vital for real-time monitoring and streamlined workflows. Traditional software’s rigidity was a bottleneck until they implemented BPM Microsystems’ solutions. Through BPM’s user-friendly interface and API, they were able to easily connect programming systems with their MES, enhancing process visibility and overall efficiency.
Complex and rigid software in device programming doesn’t just create technical challenges; it can impede an OEM’s agility, efficiency, and competitiveness. BPM Microsystems’ approach to software design addresses these pain points by emphasizing user-friendliness, customization, and seamless integration through its API. Connecting to the company MES becomes a straightforward process, breaking down barriers and fostering a more cohesive and efficient manufacturing environment. From reducing training time to enabling real-time data flow, BPM’s solutions transform what could be a constraint into an enabler of success in the ever-evolving manufacturing landscape. Whether an OEM is a large multinational corporation or a nimble startup, BPM’s focus on flexibility and integration offers tangible benefits that align with modern manufacturing needs.
Conclusion
BPM Microsystems has emerged as a problem-solver in the device programming industry by offering solutions to some of the most persistent challenges. Through automation, cost-efficient systems, extensive device support, quality assurance, and user-friendly interfaces, BPM is making device programming not just fast and affordable, but also more reliable and efficient. By aligning solutions with industry needs, BPM Microsystems is helping OEMs enhance their competitiveness and achieve greater success in today’s dynamic and demanding electronics manufacturing environment.
by Scott Bronstad | Aug 10, 2023 | Case Study, How To, Technology
Accelerating Progress: Transitioning from 7th to 9th Generation BPM Programmers – A Comprehensive Guide
Sun Sets on 7th Generation BPM Programmers
In an era of transformative technological advancement, it’s a common occurrence for some components to become obsolete due to scarcity or the evolution of technology. The same fate has befallen the 7th Generation BPM Programmers. These units, launched in 2003, have provided steadfast service for two decades. However, due to the critical parts necessary for their manufacture becoming unavailable, it’s no longer feasible to continue their production.
Despite the discontinuation of selling 7th Generation Manual Programmers, BPM Microsystems will continue to service existing 7th Generation programmers for as long as our stock of critical parts allows. BPM will continue to offer software updates, algorithms, and socket module development. Existing socket modules and replacement daughter cards will still be available for purchase.
Much like the Space Shuttles, which utilized 70’s technology well into the 2000s, the 7th Generation BPM Programmers have served far beyond their expected lifecycle. But as technology advances, so too must our tools and processes. To stay competitive, and to offer the best for our customers, an upgrade is more than necessary – it’s an inevitable part of technological evolution.
Turbocharging Efficiency: Vector Engine Technology
With the advent of the 8th Generation BPM Programmers, a significant leap was made in the form of Vector Engine™ with BitBlast technology. BitBlast offers the fastest programming speeds in the industry, vastly increasing throughput for high-density managed NAND devices that utilize the eMMC interface. The introduction of this feature resulted in drastically reduced programming times, similar to how a jet engine revolutionized travel times compared to a propeller-driven aircraft. The vector engine technology heralded a new age in programming efficiency, offering better service to our clients.
Vector Engine– Program and Verify Time Comparison:
SanDisk SDIN8DE4-64G (with DDR)
-
Without BitBlast- 2,699.0 Seconds
-
With BitBlast- 1279.8 Seconds
SanDisk SDIN8DE4-32G (with DDR)
-
Without BitBlast- 1,399 Seconds
-
With BitBlast- 618.5 Seconds
SanDisk SDIN8DE4-32G (with DDR)
-
Without BitBlast- 706.0 Seconds
-
With BitBlast- 329.5 Seconds
The Adapter Continuity: Seamless Transition from 7th to 9th Gen
One of the key considerations during any upgrade process is compatibility. The good news for users of 7th Generation BPM Programmers is that many 7th Gen adapters are forward-compatible with the 9th Gen units, usually requiring only minor algorithmic adjustments. This ensures a smooth transition and enables our customers to continue using their existing socket adapters, maximizing their investments.
|
|
Manual |
Automated |
Adapter Prefix**
|
Example
|
7th Gen
|
9th Gen
|
7th Gen
|
9th Gen
|
WSM |
WSM32PA |
No |
No |
No |
No |
LSM |
LSM2S676FGMSSOCB |
No |
No |
Yes |
Limited Support * |
LXSM |
LXSM28FLPZA |
No |
No |
Yes |
Limited Support * |
LX2SM |
LX2SM28FLPZB |
No |
No |
Yes |
Limited Support * |
LX4SM |
LX4SM40DIPLT |
No |
No |
Yes |
Limited Support * |
LASM |
LASM324BGV |
Yes |
Limited Support * |
Yes |
Limited Support * |
LXASM |
LXASM484BGAV |
Yes |
Limited Support * |
Yes |
Limited Support * |
LX2ASM |
LX2ASM473BGA |
Yes |
Limited Support * |
Yes |
Limited Support * |
LX4ASM |
LX4ASMR64QFPTB |
Yes |
Limited Support * |
Yes |
Limited Support * |
WASM |
WASM20MLFA |
Yes |
Limited Support * |
Yes |
Limited Support * |
WXASM |
WXASM100QE |
Yes |
Limited Support * |
Yes |
Limited Support * |
WX2ASM |
WX2ASML48UBG |
Yes |
Limited Support * |
Yes |
Limited Support * |
WX4ASM |
WX4ASMR08SJA |
Yes |
Limited Support * |
Yes |
Limited Support * |
The Rise of 9th Generation BPM Microsystems
The 9th Generation site technology from BPM Microsystems continues the legacy of backward compatibility, supporting many socket adapters from the 6th, 7th, and nearly all 8th generations. It provides comprehensive support for over 40,000 devices, extending the useful lifespan of previous-generation programmers. This extensive backward compatibility provides peace of mind to our clients, ensuring their investments continue to provide value for a longer period.
Embracing the Future: eMMC Devices and HS400 Programming Mode
With the technological landscape constantly shifting towards higher density and smaller package devices, the 9th Gen technology is ready to meet the challenge. It supports eMMC devices and the HS400 programming mode, capable of handling 400 MB per second. This allows manufacturers to keep up with the pace of modern production environments and meet market demands without compromising efficiency or throughput.
The transition from 7th to 9th Generation programmers signifies more than just an upgrade. It represents a transformative improvement in programming performance, ensuring our clients are well-equipped to navigate the challenges of the future. This commitment to progress and client satisfaction fuels our ongoing innovation and sets the stage for future advancements in BPM technology.
Navigating the Upgrade Path: Ensuring a Smooth Transition
Transitioning to newer technology often raises questions about compatibility, continuity, and support. To facilitate a smooth upgrade from 7th to 9th Generation BPM Programmers, we have established a well-defined upgrade path.
Firstly, users are asked to provide BPM with a list of their devices and legacy socket adapters. This allows us to evaluate which adapters can be reused and which ones, due to different pin interfaces, will no longer be compatible.
Once we’ve assessed your current setup, BPM will provide a detailed report, highlighting which socket adapters can still be used (possibly requiring a simple algorithm update) and which will need replacement (adapters with “old” pin connectors). We aim to maximize the use of your existing equipment where possible, ensuring your transition is both cost-effective and efficient.
Alongside this report, BPM will also provide a quote for 9th Gen socket and algorithm support, detailing any necessary purchases or services you may need. In an effort to help ease the transition, we’re offering up to 12 hours of algorithm development with the purchase of 4 socket adapters. This not only ensures you’re fully supported during the transition but also maximizes the efficiency of your new 9th Gen Programmers.
Despite ceasing sales of the 7th Generation Programmers, BPM remains committed to supporting our customers. We will continue to service, calibrate, and repair 7th Gen Programmers until they are officially declared end of life. Socket adapters and algorithms will also continue to be supported and developed, ensuring your operations can continue smoothly even during the upgrade process.
The transition from 7th to 9th Gen Programmers is more than just an upgrade– it’s a commitment to technological evolution, designed to ensure our clients are always ahead of the curve. We’re here to guide you through every step of this journey, ensuring the move is as seamless as possible.
Example Workflow for 7th to 9th Gen Transition
Time |
Event |
0.5 – 1.5 hours |
Customers list their devices and legacy socket adapters |
2 working days |
BPM evaluates the customers’ lists and provides a detailed report |
0.5 – 1 hour |
Customers review the report and decide on necessary purchases |
1-2 hours |
Customers place orders for necessary socket adapters and algorithm support |
2 – 4 weeks |
BPM conducts algorithm development (12 hours of development is complementary with the purchase of 4 socket adapters) |
1 working day |
BPM provides full support to customers during the transition |
3 working days |
The upgrade process is completed; customers are fully transitioned to 9th Gen Programmers |
by Scott Bronstad | Jul 19, 2023 | Case Study, How To
In an electronics manufacturing production environment where a factory has automated machines and people, how would you calculate the cost if the process stops, including lost profit and losses due to unproductive people, equipment, and overhead?
Calculating the cost of a process stoppage in an electronics manufacturing production environment requires considering various factors, including lost profit, unproductive labor costs, equipment downtime, and overhead expenses. Here’s a breakdown of the critical elements to consider when estimating the cost of a process stoppage:
- Unproductive Labor Costs: When the process stops, the labor force becomes unproductive, which leads to additional costs. Calculate the labor cost per hour or day, including wages, benefits, and other associated expenses. Multiply this by the number of employees affected by the stoppage and the duration of the stoppage. For example, if you have 50 employees and the labor cost is $25/hour, and the stoppage lasts for 16 hours, the unproductive labor cost would be $25/hour * 50 employees * 16 hours = $20,000.
- Calculating the cost of a process stoppage: The stoppage will likely result in equipment downtime, causing losses in terms of missed production output and potential repair or maintenance costs. Calculate the average revenue generated by the equipment per hour or day, and multiply it by the duration of the stoppage. Additionally, consider any repair or maintenance expenses incurred during the downtime. For example, if the equipment generates $2,000/hour and the stoppage lasts for 16 hours, the equipment downtime cost would be $2,000/hour * 16 hours = $32,000.
- Overhead Expenses: Overhead expenses, such as facility rental, utilities, administrative costs, and other fixed costs, continue even during a stoppage. Calculate the average daily overhead cost and multiply it by the duration of the stoppage. For instance, if the daily overhead expenses amount to $5,000 and the stoppage lasts for two days (16 hours), the overhead cost would be $5,000/day * 2 days = $10,000.
To calculate the total cost of the process stoppage, sum up the unproductive labor costs, equipment downtime costs, and overhead expenses. In the above examples, the total cost would be $20,000 (unproductive labor) + $32,000 (equipment downtime) + $10,000 (overhead expenses) = $62,000.
Example: 2 Days (16 hours) Down
Cost Category |
Description |
Calculation |
Cost Estimate |
Unproductive Labor |
Cost of unproductive labor during the stoppage |
Labor cost per hour * Number of employees * Duration of stoppage |
$20,000 |
Equipment Downtime |
Lost revenue and potential repair/maintenance costs |
Revenue generated by equipment per hour * Duration of stoppage |
$32,000 |
Overhead Expenses |
Fixed costs incurred during the stoppage |
Average daily overhead cost * Duration of stoppage |
$10,000 |
Total Cost |
The sum of all the cost categories |
|
$62,000 |
Remember that these calculations provide an estimate and may vary depending on the specific circumstances of the manufacturing environment. Adjust the calculations as needed to accurately reflect the costs associated with a process stoppage in your particular scenario.
As a rule of thumb support subscriptions or extended warranty agreements are 10% or more of the original value of the equipment. Given our realistic scenario above, having a complete support package in place for equipment with an initial purchase price of $200,000 is easily justifiable, considering a single downtime event can more than pay for the support.
How Much is Downtime Costing Your Electronics Manufacturing Business? | How Automated Programming Aligns with Your Vertical Manufacturing Strategy
by Scott Bronstad | Jul 14, 2023 | Case Study, How To, Service, Technology
The Importance of a Production-Level Support Agreement in Electronics Manufacturing
The rapidly evolving world of electronics manufacturing requires not only cutting-edge technology but also comprehensive support systems. Today’s advanced production environments hinge on precision, efficiency, and continuous uptime. A robust production-level support agreement is one of the most essential components of this streamlined operation. In essence, these agreements ensure that production operations receive the highest support possible, mitigating downtime and enhancing efficiency.
Industry leaders like BPM Microsystems offer support agreement subscriptions designed specifically for customers running critical operations. This approach allows for swift, efficient support while minimizing potential disruptions. Let’s delve deeper into why these support agreements are vital for electronics manufacturing and the potential consequences of neglecting this crucial component.
The Imperative Need for Production-Level Support
Today’s electronic devices have transformed from mere functional entities into complex systems of interconnected components. These innovations have led to increased demand for electronic manufacturing services. However, with this increased complexity, the need for expert support and swift troubleshooting has never been more significant.
Several reasons underline why a production-level support agreement is crucial in today’s fast-paced electronic manufacturing landscape:
- 24/7 Hotline: In an industry where downtime can lead to considerable losses, having immediate access to expert technical support is critical. BPM Microsystems, for instance, offers a hotline where customers can report device production issues outside of normal business hours, enabling the immediate commencement of debugging steps or case creation for resolution.
- Priority Case Handling: Production-level support agreements ensure that customers’ cases receive priority, reducing the time to resolution and minimizing potential disruptions to operations.
- Spare Parts: Rapid access to spare parts is another benefit of a robust support agreement. When a device fails, having the right parts available quickly can mean the difference between a minor hiccup and a significant production delay.
- On-Site Support: Some issues require expert attention on the spot. Having on-site support as part of your agreement can result in significant savings and more rapid issue resolution.
- Annual Preventative Maintenance: Regular, professional maintenance can catch potential problems before they result in downtime, keeping equipment up to date and performing optimally.
- Software Support: Keeping equipment up to date with the latest software and algorithms helps ensure the highest quality production yield.
The Potential Consequences of Downtime
Even a small glitch in the manufacturing process can have significant ramifications. It can not only halt production but also negatively impact delivery schedules, customer relationships, and, ultimately, profitability. For instance, consider a manufacturing plant that produces 5,000 electronic assemblies per hour. If the average profit per component is $1.00, even a half-day downtime can result in a loss of $60,000. (See Exhibit 1 below)
In addition to financial losses, extended downtime can strain customer relationships and potentially harm a company’s reputation. A production-level support agreement can help mitigate these risks by enabling more rapid problem resolution and minimizing downtime.
In conclusion, a production-level support agreement is a necessity in today’s complex and fast-paced world of electronics manufacturing. By partnering with a company like BPM Microsystems, manufacturers can receive a tailored production support structure that meets their specific needs, ensuring smooth operation and the timely delivery of high-quality products. Such proactive approaches can save manufacturers from the significant costs and stress of unexpected downtime and disruptions. To learn more about BPM’s production-level support, click here.
Exhibit 1: Cost of Downtime
Cost of Component ($) |
Hours Down |
Loss in Dollars ($) |
1.00 |
4 |
20,000 |
1.00 |
8 |
40,000 |
1.00 |
16 |
80,000 |
2.00 |
4 |
40,000 |
2.00 |
8 |
80,000 |
2.00 |
16 |
160,000 |
5.00 |
4 |
100,000 |
5.00 |
8 |
200,000 |
5.00 |
16 |
400,000 |
The ‘Loss in Dollars’ is calculated similarly to before by multiplying the cost of the component by the number of components produced in the specified number of hours. For instance, if the component costs $2 and the downtime is 4 hours, the loss would be $2 * 5,000 * 4 = $40,000.
Production-Level Support
by Scott Bronstad | May 5, 2023 | How To, Technology
How Automated Programming Aligns with Your Vertical Manufacturing Strategy
Why In-House Device Programming is the Future of Vertical Manufacturing
Learn how in-house programming can improve cost, time to market, and quality. See how an automated programming system can pay for itself compared to outsourcing.
Programmable devices power our modern world, from smartphones to computers to electric cars. But have you ever stopped to think about how these tiny chips are programmed and manufactured? In recent years, there has been a growing trend toward in-house offline device programming as part of the movement toward vertical manufacturing. In this article, we will explore the advantages of this approach, with a focus on cost per device, time to market, and quality.
Device Programming and Vertical Manufacturing
To understand the benefits of in-house programming and vertical manufacturing, let’s start with a real-world example. Imagine a company that designs and manufactures sensor assemblies for the automotive industry. The company relies on programmable devices to power its assembly, and it needs to program these devices with custom firmware before they can be integrated into the product.
In the past, the company outsourced the programming of these devices to a third-party supplier. This meant it had to wait for the supplier to program the devices and ship them back, which added time and cost to the manufacturing process. It also meant that the company had limited control over the quality of the programming and the security of its intellectual property. What’s worse, periodic and sometimes rapid design changes mean the devices in transit have to be reprogrammed, delaying production and ballooning costs.
Now, the company has invested in in-house off-line device programming. This means that it can program the devices themselves “just-in-time” using its own equipment and personnel, before integrating them into the sensor assembly. Let’s take a closer look at the advantages of this approach.
Cost per device
One of the biggest advantages of in-house off-line device programming is cost savings. By bringing the programming process in-house, companies can eliminate the markup third-party suppliers charge for their services. This can translate into significant savings, especially for companies that produce high volumes of devices.
In our example, the company can now program its own devices for a fraction of the cost of outsourcing the process. This has helped to improve its profit margins and make it more competitive in the market.
Time to market
Another critical advantage of in-house programming is faster time to market. By eliminating the need to wait for third-party suppliers, companies can speed up their manufacturing process and get their products to market more quickly. This can be especially important in fast-paced industries where timing is everything.
In our example, the company can now program its devices on demand, without having to wait for a supplier to do it for them. This has helped to reduce its lead times and ensure that it can meet customer demand in a timely manner. Plus, it reduces the likelihood of re-programming when designs change because the parts are programmed within days or hours before integration into the product.
Quality and Security
Finally, in-house programming can improve the quality of the programming and the security of the intellectual property. When a company outsources its programming to a third-party supplier, it loses some control over the quality of the programming and the security of its intellectual property. In-house programming, on the other hand, allows companies to maintain complete control over the process and ensure that their devices are programmed to the highest standards. And, they maintain complete traceability, controlling the exact quantity of devices programmed.
In our example, the company can now ensure that its devices are programmed to their exact specifications without relying on a third-party supplier. This has helped to improve the quality of its products and protect its intellectual property.
A system that pays for itself
Now, let’s take a closer look at how an offline automated programming system can pay for itself compared to outsourcing the device programming piece. An offline automated programming system can significantly reduce the cost of device programming while improving the quality and speed of the manufacturing process. By eliminating manual programming, an automated system can reduce the likelihood of human error and improve overall efficiency. In addition, the system can be programmed to automatically detect and correct errors, further reducing the likelihood of defects.
Furthermore, the advantages of vertically integrating device programming into your factory process extend beyond the cost savings and quality improvements. By having complete control over the programming process, companies can better protect their intellectual property and trade secrets. They can also more easily adapt to changes in customer demand or industry standards since they are not dependent on a third-party supplier.
In conclusion, in-house off-line device programming compliments the trend towards increased vertical manufacturing capability. Especially when paired with an automated programming system, this value-add process can offer significant advantages to companies in terms of cost savings, faster time to market, improved quality, and greater control over the manufacturing process. These benefits can help companies stay competitive in a rapidly changing market and continue to deliver innovative products to their customers while safeguarding their intellectual property.
by Scott Bronstad | Apr 28, 2023 | How To
In-House Programming: Crucial Process in Electronic Device Manufacturing
Semiconductor device programming is a crucial process in the manufacturing of electronic devices. It involves the creation of firmware that runs the device and enables it to perform various functions. The firmware is essentially the software that is installed on the device’s microcontroller or microprocessor, and it contains the code that controls the device’s operation.
Device programming is important because it determines how the device will function and how it will interact with other devices and systems. The firmware must be programmed correctly to ensure that the device operates as intended, and any errors in the programming can result in malfunctions or even device failure.
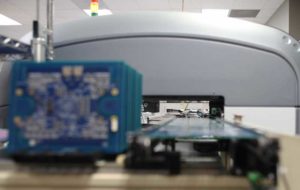
Circuit boards traveling down the SMT line at BPM Microsystems manufacturing facility in Houston Texas.
Why you should think about bringing device programming in-house
With the global supply chain becoming increasingly complex and vulnerable, many manufacturers are looking for ways to reduce their reliance on third-party providers. By bringing device programming in-house, manufacturers can have greater control over their supply chain and reduce the risk of delays or disruptions caused by external factors.
In-house programming facilities allow manufacturers to have complete control over the programming process, from design to testing and verification. This control can help manufacturers identify and resolve issues more quickly, reducing the risk of delays in the production process.
Additionally, by bringing semiconductor device programming in-house, manufacturers can reduce lead times and time-to-market. In-house programming facilities allow manufacturers to program devices on demand, reducing the need for large inventory stockpiles. This reduction in inventory can help manufacturers respond more quickly to changes in demand, ensuring that they can deliver products to market faster and with greater flexibility.
Challenges of In-House Device Programming
“I can’t afford to bring programming in-house”
For many years, outsourcing device programming has been the norm for most manufacturers. Outsourcing allows manufacturers to leverage the expertise of third-party providers with specialized equipment and personnel to perform programming services. Outsourcing can be a cost-effective option for small manufacturers who need to program only a few devices.
However, more manufacturers are now considering bringing semiconductor device programming in-house. In-house programming gives manufacturers more control over the programming process and allows them to tailor the programming to their specific needs. Additionally, in-house programming can be more cost-effective for larger manufacturers who need to program a large number of devices.
One way to overcome the challenges of in-house device programming is to use device programmers manufactured by BPM Microsystems. Their device programmers offer a range of benefits that can help manufacturers overcome the challenges of in-house programming.
BPM device programmers are designed to deliver consistent high-speed performance, accuracy, and speed, with on-the-fly alignment capabilities that guarantee fast, reliable programming. Additionally, their systems are designed to be easy to operate and maintain, maximizing uptime and productivity.
BPM programmers deliver return on investment in (usually) months, not years (see ROI article). One SMT manager described their BPM Automated Programming System (APS) as his “money printer.”
Outsourcing vs. In-House Programming
“I don’t have anyone with the technical expertise to run an in-house programmer”
In-house device programming offers numerous advantages, but manufacturers must also tackle certain challenges to establish a successful operation. Two primary concerns include costs and complexity. Establishing such an operation typically involves capital investment in specialized equipment and skilled personnel.
The programming setup process demands meticulousness and precision, as all input and output locations must be accurately “taught.” This can be a significant challenge even for experienced technicians, as an incorrect “teach” can result in wastage and failed operations.
BPM Microsystems: Transforming Challenges into Opportunities
For over three decades, BPM Microsystems has been a stalwart ally for manufacturers, helping them surmount these challenges and reap the benefits of in-house programming. Over the last three years, there has been a notable increase in smaller electronics manufacturers leveraging automated programmers, demonstrating the effectiveness of BPM’s solutions.
BPM Microsystems’ systems stand out for their efficiency and quick setup, thanks to their unique, patented WhisperTeach™ auto Z-teach technology. This innovation enables perfect setups in under 15 minutes, allowing you to start programming with the highest real-world throughput. Additionally, their universal site technology guarantees exceptional programming speeds with a single Generation of site technology, adeptly meeting your production demands.
When considering the Return on Investment (ROI), the value of BPM’s solutions becomes clear. While other systems require the expense of hiring and retaining a skilled technician, BPM Microsystems’ systems are designed for ease of use. They significantly reduce the need for specialist personnel, which translates to substantial cost savings over time. Although the initial investment in high-quality equipment might seem steep, the long-term benefits, including reduced labor costs and increased productivity, can offset these expenses.
BPM device programmers offer versatility and are upgrade-compatible with future device technology, ensuring your investment is future-proof. This access to cutting-edge programming capabilities, coupled with their award-winning support for systems, software, and sockets, delivers industry-leading assistance whenever needed. By choosing BPM Microsystems, manufacturers are not only overcoming the initial capital investment hurdle but also positioning themselves for considerable returns over time.
In conclusion, the robust design, ease of use, and upgrade compatibility of BPM’s device programmers provide a compelling solution for manufacturers looking to navigate the challenges of in-house device programming. Their investment in BPM Microsystems’ solutions not only safeguards their operations against future technological advancements but also promises a significant return on investment, making it a wise and profitable choice in the long run.