by Scott Bronstad | Aug 25, 2023 | Case Study, How To, News, Technology
Device Programming Pain Points for OEMs, and How BPM’s Solutions Make Device Programming Fast, Easy, and Affordable
Semiconductor device programming is a crucial step in the manufacturing process, one where Original Equipment Manufacturers (OEMs) often encounter significant hurdles. These challenges can impact everything from production timelines and costs to quality control and product compatibility. If you’re an OEM looking for innovative ways to transform these obstacles into competitive strengths, understanding these issues and the available solutions is essential. In this examination, we’ll explore the common pain points in device programming and highlight how emerging technologies and approaches are reshaping the landscape, offering OEMs new opportunities for efficiency, quality, and flexibility.
Manual and Time-Consuming Programming
In the traditional device programming environment, manual operations often form a critical part of the process. This manual programming methodology has far-reaching implications, impacting various aspects of production and overall efficiency.
Bottlenecks in Production
An OEM producing automotive controllers, for example, requires an efficient programming process for each component. Manually handling components can create a significant bottleneck, slowing down the entire production line. If an employee has to physically load, program, and then unload each component, the time and effort required quickly accumulate, leading to slow production throughput.
Human Errors and Quality Control
Many manufacturers have quality standards beyond Six Sigma. With manual programming, the risk of human error also increases. Whether it’s misalignment, incorrect data input, or inconsistency between batches, the errors can lead to functional defects in the final product. Quality control becomes a significant challenge, and the repercussions can be costly both in terms of time and resources.
Labor Costs and Scalability
Relying on human labor for programming tasks means that scaling up production might necessitate hiring more skilled personnel. This not only drives up labor costs but also adds complexity to the hiring and training processes. For growing businesses or those with fluctuating production needs, this can become a significant challenge.
BPM’s Solutions
BPM Microsystems’ automated programming systems provide a robust solution to these challenges. By integrating automation into the programming process, several key benefits emerge:
- Increased Throughput: Automation dramatically reduces the time taken for each programming cycle compared to manual programmers. When factoring in the time-savings in set-ups and inefficiencies of human handling, BPM automated programmers shave up to 83% compared to other competitive automated systems requiring a trained operator set-up. This means the BPM system is available for actual production for additional hours per shift.
- Consistent Quality: With automation, every programming task is performed with the same level of precision. The risk of human error is minimized, leading to consistent quality across every batch. Our machines handle components accurately, to within 15 microns each time.
- Reduced Labor Costs: Automation allows OEMs to scale up or down without a corresponding change in labor costs. This offers flexibility and can be a crucial advantage in competitive or rapidly changing markets. And, machines are intended to be set up to operate unattended for long periods of time.
- Faster Time-to-Market: With increased efficiency and reduced production times, products can reach the market faster, giving OEMs a competitive edge.
OEM Impact
The transformation from manual to automated programming is not just theoretical. BPM Microsystems’ solutions have proven applications across various industries, from automotive to consumer electronics. Companies that have adopted these automated systems have reported significant improvements in production speed, cost, efficiency, and overall product quality.
High Programming Costs
High programming costs have long been a concern for Original Equipment Manufacturers (OEMs), affecting their budget allocation, resource management, and overall profitability. Several factors contribute to these high costs, and BPM Microsystems has targeted solutions to address them.
In-House Programming Expenses
OEMs opting to handle programming in-house often face various costs that quickly add up. These may include:
- Equipment Costs: The hardware necessary for programming can be expensive, particularly if specialized or cutting-edge technology is required.
- Labor Costs: Skilled technicians are often needed to operate the equipment, leading to higher wage expenses.
- Maintenance and Upkeep: Regular maintenance and occasional upgrades are necessary to keep the equipment functioning optimally, incurring further costs.
- Scalability Challenges: In-house programming in-line or at test can also make it difficult to scale operations up or down efficiently as market demands change.
Outsourcing Programming
Alternatively, outsourcing programming tasks to third-party vendors can also be costly. This approach introduces its own challenges:
- Vendor Costs: Vendors might charge high fees for their specialized services, particularly for complex or large-scale tasks.
- Quality Control: Managing quality can be more challenging when outsourcing, potentially leading to costly mistakes or rework.
- Logistical Challenges: Shipping devices to and from vendors adds both time and expense to the process.
- Intellectual Property Concerns: Working with third-party vendors may introduce risks related to intellectual property theft or mishandling.
BPM’s Solutions
BPM Microsystems provides a multifaceted approach to combat these high programming costs that offers significant benefits:
- Cost-Effective Equipment: BPM’s solutions are designed with affordability in mind, providing state-of-the-art technology without the exorbitant price tag. More importantly, BPM equipment return on investment (ROI) is often measured in weeks, not years.
- Automation: Automated systems reduce the need for extensive manual labor, cutting down on labor costs.
- Quality Assurance: Advanced quality control features ensure accurate programming, reducing the risk of errors and rework.
- Scalable Solutions: BPM’s programming systems are designed to scale with your needs, offering flexibility without substantial incremental costs. Because programming is separated from the SMT line, production can scale without causing bottlenecks.
Consider a company producing smart home devices that must navigate constant updates and various programming tasks. By adopting BPM Microsystems’ cost-effective solutions, the manufacturer can minimize both equipment and labor costs, while maintaining quality control. This real-world application showcases how BPM’s systems support cost-saving strategies without compromising on performance or quality.
Limited Device Support
The issue of limited device support in semiconductor device programming is a complex and multifaceted problem. With the ever-growing range of programmable devices on the market, OEMs can find themselves struggling to maintain compatibility and integration with their existing systems. This challenge extends across various aspects of the manufacturing process, and BPM Microsystems’ solutions are poised to address them.
Compatibility Issues
- Multiple Standards and Formats: Devices come in various formats, standards, and technologies. This diversity can make it challenging for OEMs to maintain support for all devices, leading to integration difficulties.
- Vendor-Specific Limitations: Some programming systems might be restricted to specific manufacturers or device families, limiting flexibility in choosing components.
- Technology Evolution: As technology progresses, new devices are introduced with different requirements, making continuous support a moving target.
Impact on Manufacturing
- Production Delays: Limited support can cause significant delays in production if new or different devices are introduced that aren’t compatible with existing programming systems.
- Increased Complexity: Managing multiple programming systems for various devices adds complexity to the manufacturing process, potentially leading to mistakes or inefficiencies.
- Inability to Adapt: Limited device support might make it challenging for OEMs to adapt to new market demands or innovations, potentially leaving them behind the competition.
BPM’s Solutions
BPM Microsystems provides robust solutions to these challenges through its extensive library of supported devices and a commitment to continuous adaptation.
- Extensive Device Library: With over 70,000 supported devices, BPM Microsystems ensures broad compatibility across various standards and formats. This vast library simplifies integration and ensures that OEMs can work with a wide array of devices without concern for compatibility-related interruptions.
- Continuous Updates: BPM stays abreast of technology evolution by regularly updating its supported devices list. This ensures that the programming systems remain compatible with the latest devices and technologies.
- Customized Support: For unique or specialized requirements, BPM offers customization options, ensuring that specific device needs can be met without compromising efficiency or functionality.
Telecommunications Example
Imagine a telecommunications equipment manufacturer that needs to integrate various programmable components into its products. Different microcontrollers, flash memories, and FPGAs are sourced from multiple suppliers, each with its unique programming requirements. By leveraging BPM Microsystems’ solutions with an extensive device library, the manufacturer can smoothly integrate these different components without worrying about compatibility issues. This not only streamlines the manufacturing process but also offers the flexibility to innovate and adapt to market trends.
Inconsistent Programming Quality
Inconsistent programming quality can have serious ramifications for OEMs, affecting both the reliability of products and the reputation of the brand. This challenge encompasses various facets of the programming process, from algorithm efficiency to quality control mechanisms.
Causes of Inconsistent Quality
- Human Error: Manual processes may introduce variations in quality due to mistakes or inconsistencies in handling.
- Inadequate Algorithms: Subpar or outdated algorithms might lead to errors or inconsistencies during the programming phase.
- Lack of Quality Control Measures: Without proper quality control mechanisms, inconsistencies might go undetected until they lead to failures in the field.
- Environmental Factors: Fluctuations in temperature, humidity, or power supply can introduce variations in programming quality.
Consequences
- Device Failures: Inconsistent programming quality can lead to device malfunctions, reducing the reliability of the end products.
- Product Recalls: Serious inconsistencies may necessitate product recalls, an expensive and reputation-damaging process.
- Loss of Customer Trust: Repeated quality issues can erode customer trust, potentially leading to a decrease in market share.
- Increased Costs: Dealing with quality inconsistencies can introduce additional costs in terms of rework, testing, and support.
BPM’s Solutions
BPM Microsystems’ approach to ensuring consistent programming quality involves a combination of technological innovation and rigorous quality control:
- Advanced Algorithms: By employing cutting-edge algorithms, BPM ensures accurate and efficient programming, minimizing the risk of inconsistencies.
- Quality Control Features: BPM’s programming systems come with robust quality control features that automatically detect and reject parts that do not pass. 3D inspection, automotive-level detection of mechanical defects/errors, is also available on most systems. After programming, the 3D vision system measures the contacts of devices before placed in output media to ensure quality. Manufacturers achieve the highest production yield and process efficiency for programming mission-critical devices by integrating 3D coplanarity vision inspection.
- Environmentally Stable Systems: BPM’s solutions are designed to work efficiently across a range of environmental conditions, ensuring that external factors don’t affect programming quality. Systems need to be in climate-controlled environments but do not require clean room standards.
- End-to-End Monitoring: BPM provides tools to monitor the entire programming process, giving operators insight into the quality of the process and enabling timely intervention if needed.
Medical Device Example
Consider a medical equipment manufacturer where accurate programming is not just about efficiency; it’s a matter of patient safety. Inconsistent programming quality in a critical device like a pacemaker could lead to life-threatening malfunctions. By leveraging BPM Microsystems’ advanced algorithms and quality control features, this manufacturer can guarantee accurate and reliable programming. This ensures that the pacemakers are not only consistent in quality but also meet the stringent safety standards required in medical applications.
Inconsistent programming quality is a complex issue with the potential to affect nearly every aspect of a product’s life cycle. From manufacturing efficiency to customer satisfaction, the ripple effects of quality inconsistencies can be far-reaching. BPM Microsystems’ targeted solutions address this challenge head-on, providing the tools and technologies needed to ensure accurate, consistent, and reliable programming. Whether in safety-critical applications like medical devices or in highly competitive consumer markets, BPM’s commitment to quality turns a potential vulnerability into a consistent strength for OEMs. The comprehensive approach to quality assurance fosters trust, reliability, and success in today’s demanding manufacturing environment.
Complex and Rigid Software
In the dynamic world of device programming, complex and rigid software can be a substantial obstacle for OEMs. Traditional programming software might be challenging to learn, hard to customize, and inflexible in integrating with other systems like Manufacturing Execution Systems (MES). Let’s explore this issue in-depth and understand how BPM Microsystems’ solutions, including their Application Programming Interface (API), address these challenges.
Challenges with Traditional Programming Software
- Steep Learning Curve: Conventional programming software can be difficult to learn, especially for non-technical personnel, resulting in longer training periods and potential mistakes.
- Integration Difficulties: Connecting traditional programming systems to other essential platforms like MES can be a complex and time-consuming task.
- Incompatibility with New Technologies: Rigid software might not adapt well to technological advancements, leading to obsolescence or the need for costly upgrades.
Impact on Operations
These challenges translate into tangible operational problems:
- Delayed Onboarding: Training employees on complex systems can delay the onboarding process, affecting production schedules.
- Operational Inefficiencies: Lack of customization and integration can lead to disjointed workflows and inefficiencies in the manufacturing process.
- Increased Costs: Investing in training, customization, and integration can drive up costs.
BPM’s Solutions: Emphasizing Flexibility and Integration
BPM Microsystems offers solutions designed to overcome these challenges through user-friendly software and seamless integration capabilities:
- User-Friendly Interface: BPM’s software is designed with the user in mind, offering an intuitive and straightforward interface that minimizes training time and simplifies daily operations. For users of BPM manual systems, the transition to automated solutions is seamless. The same software, BPWin, is used for both platforms, with a few additional operations and customization.
- Customizable Workflows: The flexibility to tailor the programming process to specific needs enables OEMs to align the system with their unique requirements, enhancing efficiency.
- BPM’s API for MES Integration: BPM’s BPWin Application Programming Interface (API) makes it easy to connect to a company’s MES. This ensures that data flows smoothly between programming and manufacturing systems, facilitating real-time monitoring, quality control, and process optimization.
- Future-Proof Design: Designed with adaptability in mind, BPM’s solutions can grow and evolve with technological advancements, ensuring long-term value.
OEM Challenges
Consider a global electronics manufacturer that utilizes complex supply chain and manufacturing processes. Integration between programming systems and MES is vital for real-time monitoring and streamlined workflows. Traditional software’s rigidity was a bottleneck until they implemented BPM Microsystems’ solutions. Through BPM’s user-friendly interface and API, they were able to easily connect programming systems with their MES, enhancing process visibility and overall efficiency.
Complex and rigid software in device programming doesn’t just create technical challenges; it can impede an OEM’s agility, efficiency, and competitiveness. BPM Microsystems’ approach to software design addresses these pain points by emphasizing user-friendliness, customization, and seamless integration through its API. Connecting to the company MES becomes a straightforward process, breaking down barriers and fostering a more cohesive and efficient manufacturing environment. From reducing training time to enabling real-time data flow, BPM’s solutions transform what could be a constraint into an enabler of success in the ever-evolving manufacturing landscape. Whether an OEM is a large multinational corporation or a nimble startup, BPM’s focus on flexibility and integration offers tangible benefits that align with modern manufacturing needs.
Conclusion
BPM Microsystems has emerged as a problem-solver in the device programming industry by offering solutions to some of the most persistent challenges. Through automation, cost-efficient systems, extensive device support, quality assurance, and user-friendly interfaces, BPM is making device programming not just fast and affordable, but also more reliable and efficient. By aligning solutions with industry needs, BPM Microsystems is helping OEMs enhance their competitiveness and achieve greater success in today’s dynamic and demanding electronics manufacturing environment.
by Scott Bronstad | Aug 18, 2023 | Case Study, Service, Technology
Device programming machines and associated components are critical in the manufacturing and testing process of most electronic products. While it may seem tempting to initially save costs by opting for low-cost providers, several drawbacks often make these choices a wrong solution for most applications. This article will focus on five key ways low-cost providers can lead to poor service and lower quality.
1. Limited Technical Support and Customer Service
In the intricate and precision-driven domain of electronics manufacturing, technical support, and customer service play pivotal roles in ensuring smooth operations. High-quality service is not just about addressing issues, but proactively preventing them and optimizing processes. As businesses evaluate cost-effective options, they must consider the long-term implications of partnering with providers who may compromise on support and service. Unfortunately, low-cost providers might prioritize immediate cost savings over robust customer service, resulting in potential operational hiccups, frustrations, and inefficiencies. In this section, we shed light on some challenges associated with limited technical support and the absence of customer-centric solutions.
Delayed Response Times: The Domino Effect of Inadequate Investment in Support
When considering low-cost providers, businesses often focus on immediate monetary savings, overlooking the long-term implications of subpar customer support. In the electronics industry, even minor equipment malfunctions or technical glitches can translate into downtime and significant losses, making swift and expert technical assistance paramount.
Low-cost providers, in their bid to cut costs, might not adequately invest in customer support infrastructure. This can manifest in several ways:
Insufficient Staffing: A thinly stretched support team can result in delayed responses to queries and complaints. Every moment a company waits for a resolution, it accumulates losses in terms of halted production, wasted resources, and potential missed deadlines.
Lack of Expertise: Not all support is created equal. Having a support team that lacks in-depth knowledge about the equipment they’re supposed to troubleshoot can lead to longer resolution times. Instead of a quick, informed fix, companies might find themselves in prolonged back-and-forth communications, trying to explain the problem and waiting for the support team to catch up.
Reactive Instead of Proactive Approach: Ideally, a robust technical support team not only addresses issues but anticipates potential problems, offering solutions before they escalate. With low-cost providers, this proactive approach is often missing, making businesses perpetually reactive to arising issues.
Lack of Customized Solutions: The Challenge of One-Size-Fits-All Approaches
The electronics manufacturing world is characterized by its diversity in terms of needs, specifications, and operational complexities. What works seamlessly for one setup might be entirely unsuitable for another. This makes the ability to offer tailored solutions not just a nice-to-have, but a critical need.
However, low-cost providers, in their endeavor to streamline operations and reduce costs, often adopt a one-size-fits-all approach, which presents several challenges:
Integration Difficulties: With generic solutions, businesses might find themselves facing integration issues when attempting to incorporate products into their unique setups. This can lead to additional costs in terms of both time and resources, as teams try to work around these integration challenges.
Compromised Efficiency: Customized solutions are designed keeping specific needs in mind, ensuring optimal efficiency. Generic solutions, on the other hand, might require workarounds or manual interventions, leading to reduced operational efficiency and increased chances of human error.
Future Scalability Concerns: As businesses evolve and scale, their needs change. Tailored solutions often come with the flexibility to adapt and scale with the business. Generic solutions from low-cost providers might lack this adaptability, leading to future bottlenecks and potential needs for entirely new or alternative solutions.
In the electronics industry, where precision, efficiency, and adaptability are key, the shortcomings associated with delayed response times and the lack of customized solutions can have far-reaching implications. The initial savings from opting for low-cost providers might soon be overshadowed by the cascading costs and challenges arising from these limitations.
2. Hidden Costs of Maintenance & Scalability with Low-Cost Providers
When initially considering low-cost providers for semiconductor device programming machines and socket adapters, the upfront savings can seem alluring. However, beneath the surface lie hidden costs, primarily arising from maintenance issues:
Sparse Availability of Parts: A frequent issue with budget providers is the scant availability of essential components for repairs, especially when parts are sourced internationally. This isn’t merely a question of waiting a few extra days. The prolonged downtime incurred as you hunt for third-party replacements can lead to operational delays or worse, your production line down, driving up costs. Moreover, when forced to rely on non-original parts, there’s no guarantee of compatibility or quality, potentially compromising the overall efficiency and lifespan of the machine.
Purpose-Built Versus Universal Capabilities: Low-cost providers often lean towards offering purpose-built solutions, designed for a limited set of applications. While these might work adequately within their confined scope, they lack the adaptability and scalability that comes with universal-capable equipment. Such purpose-built systems might seem cost-effective initially, but they soon reveal their limitations when businesses need to adapt or scale their operations.
In contrast, universal-capable systems are designed to be flexible, catering to a wider range of operational needs. With a one-size-fits-all solution, businesses are frequently entangled in manual interventions, making constant adjustments and devising workarounds. This not only amplifies maintenance efforts and costs but also introduces inefficiencies, subjecting the equipment to undue stress and potentially shortening its operational life.
In the long run, investing in universally capable systems provides a holistic solution, ensuring adaptability, efficiency, and longevity, unlike the narrow confines of purpose-built equipment.
3. Inferior Quality of Materials and Components
Substandard Materials: Low-cost providers often use inferior materials to keep prices competitive. While appearing functional in the short term, these subpar materials can degrade at an accelerated rate. This not only means more frequent replacements but also compromises the reliability of semiconductor programming.
Component Sourcing and Supply Chain: The supply chain strategy of budget providers can be riddled with pitfalls. They might not prioritize sourcing high-quality components, leading to inconsistent performance. Furthermore, a fragile supply chain can pose problems during times of global disruptions, potentially halting your operations due to a lack of essential components.
Respecting Industry Standards and Conflict Sourcing: A grave concern with low-cost providers is their potential non-adherence to industry norms. This can involve using parts sourced from conflict zones, presenting both ethical and legal dilemmas. There’s also a risk of these components being subpar in quality or even counterfeit, which can jeopardize the functionality of the machines.
Spare Parts Availability: Beyond the immediate purchase, machines require ongoing maintenance and occasional part replacements. With budget providers, finding genuine spare parts can become a Herculean task, forcing companies to resort to potentially incompatible or substandard third-party alternatives.
4. Non-compliance with Quality and Safety Standards
In the intricate landscape of device programming and electronics manufacturing, compliance with recognized quality and safety standards isn’t merely a badge of honor—it’s a fundamental requirement. These standards, developed after rigorous research and consensus from industry leaders, ensure that equipment is not only efficient but also safe for both operators and end-users. When manufacturers opt for low-cost providers who overlook these essential standards, they not only jeopardize the functionality and reliability of their products but also expose themselves to potential legal liabilities and reputational damage.
CE Mark: This mark is a certification that the product meets EU safety, health, and environmental requirements. Low-cost providers might skip this crucial certification to cut corners, posing potential safety risks and non-compliance issues in the European market.
ESD Compliance: Electrostatic Discharge (ESD) compliance ensures that equipment is safe from sudden electric shocks. Non-compliant machines can lead to data loss and damage, or even pose fire risks.
CSA: The Canadian Standards Association (CSA) mark indicates that the product has been tested and meets applicable standards for safety and performance. Without this, the equipment’s safety and reliability in the Canadian context remain uncertain.
5. Limited Investment in Innovation
In a realm where the pace of technological change is relentless, continuous innovation becomes the lifeblood of success. Companies at the cutting edge recognize the imperative of constant evolution, committing resources to research, design, and refining processes. However, by opting for low-cost providers, businesses may inadvertently partner with entities more focused on short-term returns than on the future’s transformative possibilities. Such providers often neglect to prioritize the latest technologies, best practices, or attain necessary certifications, potentially hindering the progress of those they serve.
ISO 9001:2015 Certified Design and Manufacturing Process: This certification speaks to an organization’s commitment to quality and continuous improvement. Low-cost providers might not invest in such recognized certifications, raising questions about their dedication to quality and innovation.
Design and IP Ownership: Depth of knowledge, intellectual property ownership, and having a vested interest in the product design can be a game-changer. It ensures that the provider is invested in the long-term functionality, support, and improvements of the equipment.
Product Life Expectancy: Budget providers often lack the foundational research and robust design principles underpinning their products. This can lead to equipment significantly reduced operational life expectancy, requiring replacements much sooner than with quality alternatives.
Conclusion
While the appeal of saving costs with low-cost providers of semiconductor device programming machines and socket adapters is evident, the risks associated with poor service and lower quality are significant. Compromises in materials, craftsmanship, technical support, compliance with standards, warranties, and innovation can lead to unexpected costs, delays, and failures. Therefore, when considering a supplier for these critical components, it is vital to consider not just the price but also the long-term value, reliability, and support that align with your specific needs and industry standards. Investing in quality products and providers might seem more expensive upfront but can pay off in the long term by ensuring smooth operations, compliance, and adaptability to future technological advances.
by Scott Bronstad | Aug 10, 2023 | Case Study, How To, Technology
Accelerating Progress: Transitioning from 7th to 9th Generation BPM Programmers – A Comprehensive Guide
Sun Sets on 7th Generation BPM Programmers
In an era of transformative technological advancement, it’s a common occurrence for some components to become obsolete due to scarcity or the evolution of technology. The same fate has befallen the 7th Generation BPM Programmers. These units, launched in 2003, have provided steadfast service for two decades. However, due to the critical parts necessary for their manufacture becoming unavailable, it’s no longer feasible to continue their production.
Despite the discontinuation of selling 7th Generation Manual Programmers, BPM Microsystems will continue to service existing 7th Generation programmers for as long as our stock of critical parts allows. BPM will continue to offer software updates, algorithms, and socket module development. Existing socket modules and replacement daughter cards will still be available for purchase.
Much like the Space Shuttles, which utilized 70’s technology well into the 2000s, the 7th Generation BPM Programmers have served far beyond their expected lifecycle. But as technology advances, so too must our tools and processes. To stay competitive, and to offer the best for our customers, an upgrade is more than necessary – it’s an inevitable part of technological evolution.
Turbocharging Efficiency: Vector Engine Technology
With the advent of the 8th Generation BPM Programmers, a significant leap was made in the form of Vector Engine™ with BitBlast technology. BitBlast offers the fastest programming speeds in the industry, vastly increasing throughput for high-density managed NAND devices that utilize the eMMC interface. The introduction of this feature resulted in drastically reduced programming times, similar to how a jet engine revolutionized travel times compared to a propeller-driven aircraft. The vector engine technology heralded a new age in programming efficiency, offering better service to our clients.
Vector Engine– Program and Verify Time Comparison:
SanDisk SDIN8DE4-64G (with DDR)
-
Without BitBlast- 2,699.0 Seconds
-
With BitBlast- 1279.8 Seconds
SanDisk SDIN8DE4-32G (with DDR)
-
Without BitBlast- 1,399 Seconds
-
With BitBlast- 618.5 Seconds
SanDisk SDIN8DE4-32G (with DDR)
-
Without BitBlast- 706.0 Seconds
-
With BitBlast- 329.5 Seconds
The Adapter Continuity: Seamless Transition from 7th to 9th Gen
One of the key considerations during any upgrade process is compatibility. The good news for users of 7th Generation BPM Programmers is that many 7th Gen adapters are forward-compatible with the 9th Gen units, usually requiring only minor algorithmic adjustments. This ensures a smooth transition and enables our customers to continue using their existing socket adapters, maximizing their investments.
|
|
Manual |
Automated |
Adapter Prefix**
|
Example
|
7th Gen
|
9th Gen
|
7th Gen
|
9th Gen
|
WSM |
WSM32PA |
No |
No |
No |
No |
LSM |
LSM2S676FGMSSOCB |
No |
No |
Yes |
Limited Support * |
LXSM |
LXSM28FLPZA |
No |
No |
Yes |
Limited Support * |
LX2SM |
LX2SM28FLPZB |
No |
No |
Yes |
Limited Support * |
LX4SM |
LX4SM40DIPLT |
No |
No |
Yes |
Limited Support * |
LASM |
LASM324BGV |
Yes |
Limited Support * |
Yes |
Limited Support * |
LXASM |
LXASM484BGAV |
Yes |
Limited Support * |
Yes |
Limited Support * |
LX2ASM |
LX2ASM473BGA |
Yes |
Limited Support * |
Yes |
Limited Support * |
LX4ASM |
LX4ASMR64QFPTB |
Yes |
Limited Support * |
Yes |
Limited Support * |
WASM |
WASM20MLFA |
Yes |
Limited Support * |
Yes |
Limited Support * |
WXASM |
WXASM100QE |
Yes |
Limited Support * |
Yes |
Limited Support * |
WX2ASM |
WX2ASML48UBG |
Yes |
Limited Support * |
Yes |
Limited Support * |
WX4ASM |
WX4ASMR08SJA |
Yes |
Limited Support * |
Yes |
Limited Support * |
The Rise of 9th Generation BPM Microsystems
The 9th Generation site technology from BPM Microsystems continues the legacy of backward compatibility, supporting many socket adapters from the 6th, 7th, and nearly all 8th generations. It provides comprehensive support for over 40,000 devices, extending the useful lifespan of previous-generation programmers. This extensive backward compatibility provides peace of mind to our clients, ensuring their investments continue to provide value for a longer period.
Embracing the Future: eMMC Devices and HS400 Programming Mode
With the technological landscape constantly shifting towards higher density and smaller package devices, the 9th Gen technology is ready to meet the challenge. It supports eMMC devices and the HS400 programming mode, capable of handling 400 MB per second. This allows manufacturers to keep up with the pace of modern production environments and meet market demands without compromising efficiency or throughput.
The transition from 7th to 9th Generation programmers signifies more than just an upgrade. It represents a transformative improvement in programming performance, ensuring our clients are well-equipped to navigate the challenges of the future. This commitment to progress and client satisfaction fuels our ongoing innovation and sets the stage for future advancements in BPM technology.
Navigating the Upgrade Path: Ensuring a Smooth Transition
Transitioning to newer technology often raises questions about compatibility, continuity, and support. To facilitate a smooth upgrade from 7th to 9th Generation BPM Programmers, we have established a well-defined upgrade path.
Firstly, users are asked to provide BPM with a list of their devices and legacy socket adapters. This allows us to evaluate which adapters can be reused and which ones, due to different pin interfaces, will no longer be compatible.
Once we’ve assessed your current setup, BPM will provide a detailed report, highlighting which socket adapters can still be used (possibly requiring a simple algorithm update) and which will need replacement (adapters with “old” pin connectors). We aim to maximize the use of your existing equipment where possible, ensuring your transition is both cost-effective and efficient.
Alongside this report, BPM will also provide a quote for 9th Gen socket and algorithm support, detailing any necessary purchases or services you may need. In an effort to help ease the transition, we’re offering up to 12 hours of algorithm development with the purchase of 4 socket adapters. This not only ensures you’re fully supported during the transition but also maximizes the efficiency of your new 9th Gen Programmers.
Despite ceasing sales of the 7th Generation Programmers, BPM remains committed to supporting our customers. We will continue to service, calibrate, and repair 7th Gen Programmers until they are officially declared end of life. Socket adapters and algorithms will also continue to be supported and developed, ensuring your operations can continue smoothly even during the upgrade process.
The transition from 7th to 9th Gen Programmers is more than just an upgrade– it’s a commitment to technological evolution, designed to ensure our clients are always ahead of the curve. We’re here to guide you through every step of this journey, ensuring the move is as seamless as possible.
Example Workflow for 7th to 9th Gen Transition
Time |
Event |
0.5 – 1.5 hours |
Customers list their devices and legacy socket adapters |
2 working days |
BPM evaluates the customers’ lists and provides a detailed report |
0.5 – 1 hour |
Customers review the report and decide on necessary purchases |
1-2 hours |
Customers place orders for necessary socket adapters and algorithm support |
2 – 4 weeks |
BPM conducts algorithm development (12 hours of development is complementary with the purchase of 4 socket adapters) |
1 working day |
BPM provides full support to customers during the transition |
3 working days |
The upgrade process is completed; customers are fully transitioned to 9th Gen Programmers |
by Scott Bronstad | Jul 19, 2023 | Case Study, How To
In an electronics manufacturing production environment where a factory has automated machines and people, how would you calculate the cost if the process stops, including lost profit and losses due to unproductive people, equipment, and overhead?
Calculating the cost of a process stoppage in an electronics manufacturing production environment requires considering various factors, including lost profit, unproductive labor costs, equipment downtime, and overhead expenses. Here’s a breakdown of the critical elements to consider when estimating the cost of a process stoppage:
- Unproductive Labor Costs: When the process stops, the labor force becomes unproductive, which leads to additional costs. Calculate the labor cost per hour or day, including wages, benefits, and other associated expenses. Multiply this by the number of employees affected by the stoppage and the duration of the stoppage. For example, if you have 50 employees and the labor cost is $25/hour, and the stoppage lasts for 16 hours, the unproductive labor cost would be $25/hour * 50 employees * 16 hours = $20,000.
- Calculating the cost of a process stoppage: The stoppage will likely result in equipment downtime, causing losses in terms of missed production output and potential repair or maintenance costs. Calculate the average revenue generated by the equipment per hour or day, and multiply it by the duration of the stoppage. Additionally, consider any repair or maintenance expenses incurred during the downtime. For example, if the equipment generates $2,000/hour and the stoppage lasts for 16 hours, the equipment downtime cost would be $2,000/hour * 16 hours = $32,000.
- Overhead Expenses: Overhead expenses, such as facility rental, utilities, administrative costs, and other fixed costs, continue even during a stoppage. Calculate the average daily overhead cost and multiply it by the duration of the stoppage. For instance, if the daily overhead expenses amount to $5,000 and the stoppage lasts for two days (16 hours), the overhead cost would be $5,000/day * 2 days = $10,000.
To calculate the total cost of the process stoppage, sum up the unproductive labor costs, equipment downtime costs, and overhead expenses. In the above examples, the total cost would be $20,000 (unproductive labor) + $32,000 (equipment downtime) + $10,000 (overhead expenses) = $62,000.
Example: 2 Days (16 hours) Down
Cost Category |
Description |
Calculation |
Cost Estimate |
Unproductive Labor |
Cost of unproductive labor during the stoppage |
Labor cost per hour * Number of employees * Duration of stoppage |
$20,000 |
Equipment Downtime |
Lost revenue and potential repair/maintenance costs |
Revenue generated by equipment per hour * Duration of stoppage |
$32,000 |
Overhead Expenses |
Fixed costs incurred during the stoppage |
Average daily overhead cost * Duration of stoppage |
$10,000 |
Total Cost |
The sum of all the cost categories |
|
$62,000 |
Remember that these calculations provide an estimate and may vary depending on the specific circumstances of the manufacturing environment. Adjust the calculations as needed to accurately reflect the costs associated with a process stoppage in your particular scenario.
As a rule of thumb support subscriptions or extended warranty agreements are 10% or more of the original value of the equipment. Given our realistic scenario above, having a complete support package in place for equipment with an initial purchase price of $200,000 is easily justifiable, considering a single downtime event can more than pay for the support.
How Much is Downtime Costing Your Electronics Manufacturing Business? | How Automated Programming Aligns with Your Vertical Manufacturing Strategy
by Scott Bronstad | Jul 14, 2023 | Case Study, How To, Service, Technology
The Importance of a Production-Level Support Agreement in Electronics Manufacturing
The rapidly evolving world of electronics manufacturing requires not only cutting-edge technology but also comprehensive support systems. Today’s advanced production environments hinge on precision, efficiency, and continuous uptime. A robust production-level support agreement is one of the most essential components of this streamlined operation. In essence, these agreements ensure that production operations receive the highest support possible, mitigating downtime and enhancing efficiency.
Industry leaders like BPM Microsystems offer support agreement subscriptions designed specifically for customers running critical operations. This approach allows for swift, efficient support while minimizing potential disruptions. Let’s delve deeper into why these support agreements are vital for electronics manufacturing and the potential consequences of neglecting this crucial component.
The Imperative Need for Production-Level Support
Today’s electronic devices have transformed from mere functional entities into complex systems of interconnected components. These innovations have led to increased demand for electronic manufacturing services. However, with this increased complexity, the need for expert support and swift troubleshooting has never been more significant.
Several reasons underline why a production-level support agreement is crucial in today’s fast-paced electronic manufacturing landscape:
- 24/7 Hotline: In an industry where downtime can lead to considerable losses, having immediate access to expert technical support is critical. BPM Microsystems, for instance, offers a hotline where customers can report device production issues outside of normal business hours, enabling the immediate commencement of debugging steps or case creation for resolution.
- Priority Case Handling: Production-level support agreements ensure that customers’ cases receive priority, reducing the time to resolution and minimizing potential disruptions to operations.
- Spare Parts: Rapid access to spare parts is another benefit of a robust support agreement. When a device fails, having the right parts available quickly can mean the difference between a minor hiccup and a significant production delay.
- On-Site Support: Some issues require expert attention on the spot. Having on-site support as part of your agreement can result in significant savings and more rapid issue resolution.
- Annual Preventative Maintenance: Regular, professional maintenance can catch potential problems before they result in downtime, keeping equipment up to date and performing optimally.
- Software Support: Keeping equipment up to date with the latest software and algorithms helps ensure the highest quality production yield.
The Potential Consequences of Downtime
Even a small glitch in the manufacturing process can have significant ramifications. It can not only halt production but also negatively impact delivery schedules, customer relationships, and, ultimately, profitability. For instance, consider a manufacturing plant that produces 5,000 electronic assemblies per hour. If the average profit per component is $1.00, even a half-day downtime can result in a loss of $60,000. (See Exhibit 1 below)
In addition to financial losses, extended downtime can strain customer relationships and potentially harm a company’s reputation. A production-level support agreement can help mitigate these risks by enabling more rapid problem resolution and minimizing downtime.
In conclusion, a production-level support agreement is a necessity in today’s complex and fast-paced world of electronics manufacturing. By partnering with a company like BPM Microsystems, manufacturers can receive a tailored production support structure that meets their specific needs, ensuring smooth operation and the timely delivery of high-quality products. Such proactive approaches can save manufacturers from the significant costs and stress of unexpected downtime and disruptions. To learn more about BPM’s production-level support, click here.
Exhibit 1: Cost of Downtime
Cost of Component ($) |
Hours Down |
Loss in Dollars ($) |
1.00 |
4 |
20,000 |
1.00 |
8 |
40,000 |
1.00 |
16 |
80,000 |
2.00 |
4 |
40,000 |
2.00 |
8 |
80,000 |
2.00 |
16 |
160,000 |
5.00 |
4 |
100,000 |
5.00 |
8 |
200,000 |
5.00 |
16 |
400,000 |
The ‘Loss in Dollars’ is calculated similarly to before by multiplying the cost of the component by the number of components produced in the specified number of hours. For instance, if the component costs $2 and the downtime is 4 hours, the loss would be $2 * 5,000 * 4 = $40,000.
Production-Level Support
by Scott Bronstad | Jun 28, 2023 | Case Study, Technology
Part 6 – Unveiling the Power of Offline In-Socket Programming
In the grand finale of our series examining offline in-socket programming, we delve into its profound impact on maximizing assembly line uptime, enhancing inventory management, reducing cost per device, and offering higher first-pass yield. Offline programming has the potential to avert issues that could halt the assembly line, prevent faulty devices from reaching assembly, and reduce rework, thereby ensuring continuous operation and efficient inventory management.
Maximizing Assembly Line Uptime
Offline programming separates the programming process from the assembly line, ensuring that any issues arising during programming don’t impact the assembly line directly. By preventing faulty devices from reaching the assembly process and reducing rework due to programming errors, offline programming allows the assembly line to run more smoothly. This separation enables the assembly line to continue operations even if programming needs to pause, buffering against fluctuations in demand and maximizing productivity.
Efficient Inventory Management
Offline programming allows common “blank chips” to be purchased in bulk and programmed in just-in-time to meet production requirements. If a buffer is desired, devices can be produced in advance and stored; and if necessary, to be reprogrammed for code changes. This ensures a steady supply of programmed devices, smoothing production flows, and reducing the amount of work-in-progress inventory. By guaranteeing each chip is correctly programmed before it enters assembly, offline programming also mitigates the risk of having to scrap or rework finished goods.
Reducing Cost Per Device
The cost per device, a key metric in the programming and manufacturing industries, evaluates the efficiency and cost-effectiveness of programming methods. Offline programming often allows for higher throughput, better equipment utilization, energy efficiency, minimized downtime, and reduced dependency on skilled labor, all contributing to a potentially lower cost per device.
Superior First-Pass Yield
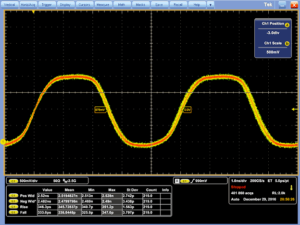
High-quality signals, Examples: Free-Running Clock (200MHz)
Programming in-socket on a dedicated system using clean waveforms leads to very high first-pass yields, reducing scrap and lowering cost per device. Bad devices can be identified upstream and returned to component suppliers for replacement or credit.
A Contract Manufacturer programming microcontrollers for an automotive client can benefit from offline programming. Preprogramming and storing chips enable them to maintain assembly line uptime, manage inventory efficiently, and buffer against sudden demand surges. The parallel programming feature also allows them to reduce the cost per device by programming multiples of the same devices concurrently.
The superior first-pass yield of offline programming can be crucial for an OEM manufacturing advanced drones. These drones use sophisticated chips that need to function perfectly. By programming in-socket on a dedicated system, they ensure very high first-pass yields, reducing the chance of scrapped units and lowering the overall cost per device.
In conclusion, this six-part series has comprehensively explored the multifaceted benefits of in-socket programming. From superior quality assurance, flexibility, and ease of troubleshooting to notable efficiency gains, exceptional versatility, and impacts on assembly line uptime and inventory management, offline programming offers significant advantages. These benefits, along with the potential for reduced costs and improved first-pass yield, make offline in-socket programming a powerful tool for electronics manufacturing.
Read Part I | Read Part II | Read Part III | Read Part IV | Read Part V