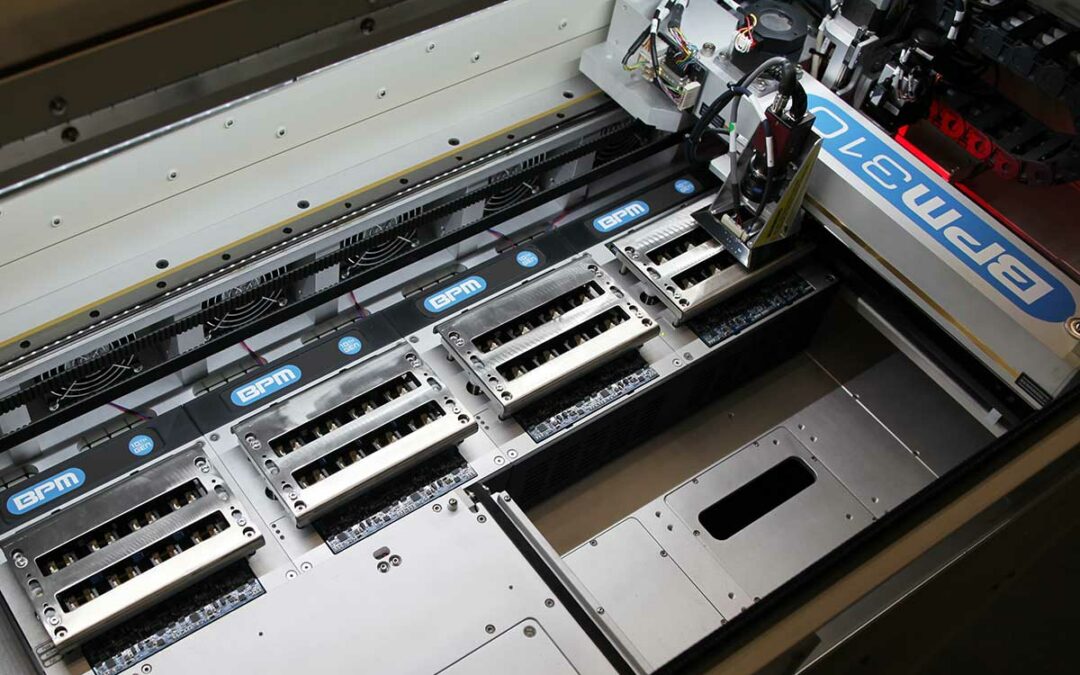
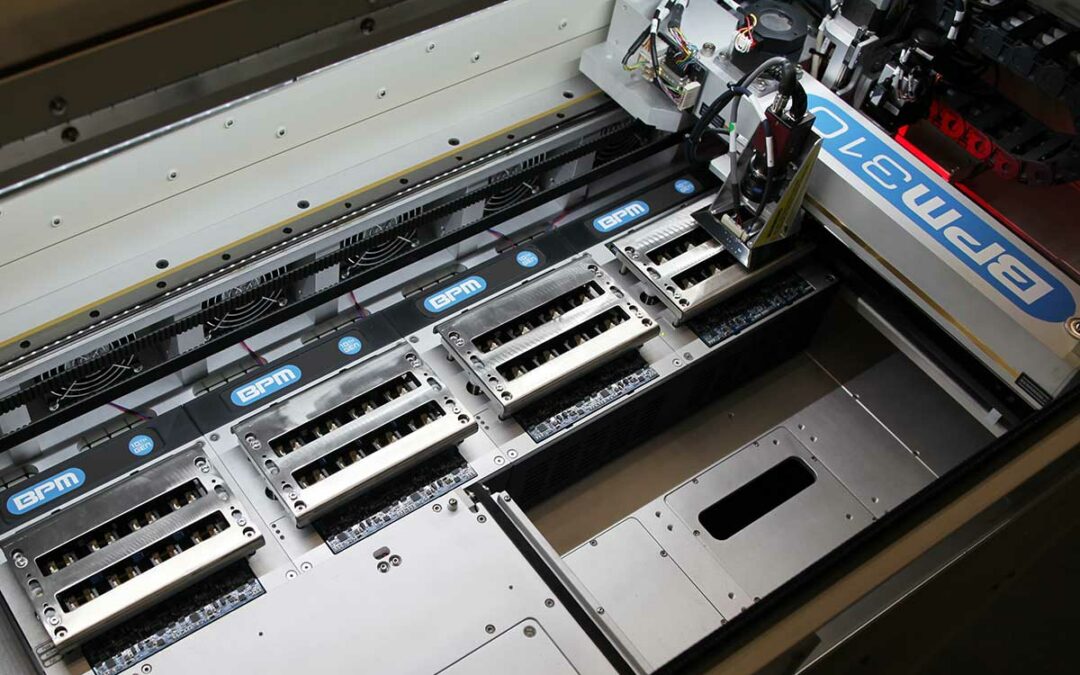
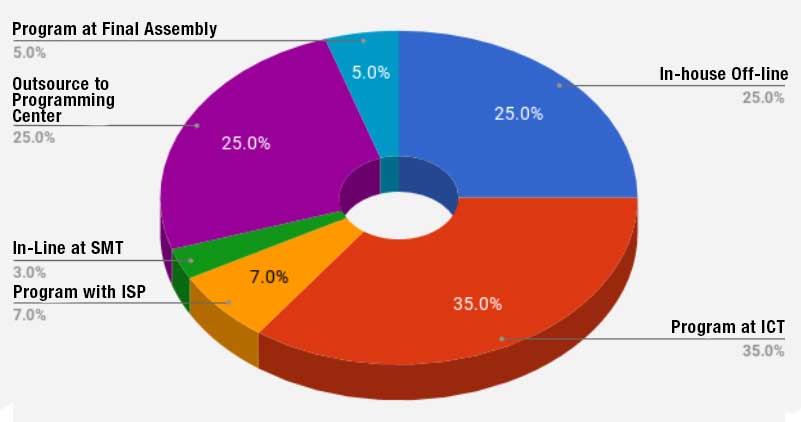
What is the Best Way to Get Devices Programmed?
What is the Best Way to Get Devices Programmed? There are lots of ways to get your data on devices, and there’s no one “Best” programming that is always better than another. Options that are available today: In-House Off-Line Programming Program at ICT...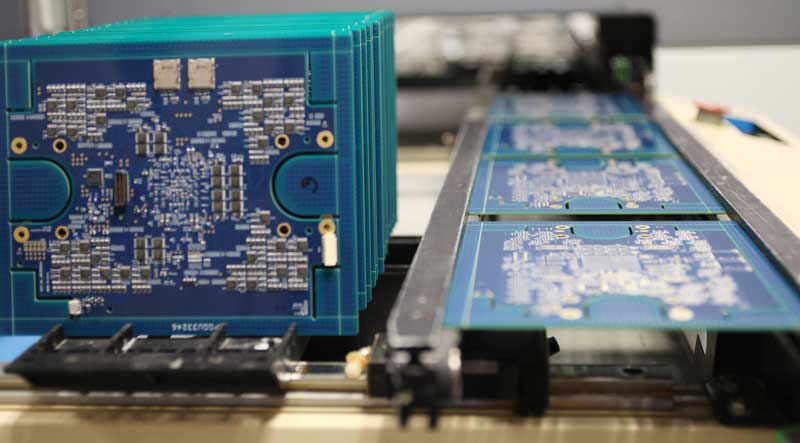
Best Method for Device Programming:
Which is best for your application?
Programming semiconductor devices is a crucial step in ensuring their proper functioning in electronic devices. There are several methods available for programming these devices, each with its own advantages and disadvantages. In this article, we will discuss three popular methods: in-system programming (ISP), offline programming, and Inline SMT Programming.
ISP Device Programming
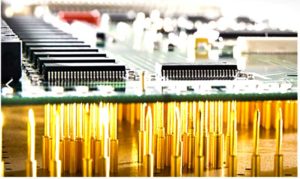
Bed-of-Nails fixture connects the PCB to the final test
In-system programming (ISP) is a method that involves programming the device while it is still in the final application or system. This can be done by connecting the device to a computer or other programming device through a specialized interface, such as a JTAG or SPI interface. ISP is a more cost-effective option for high-volume production as it eliminates the need for a separate device programmer. However, it can be more complex and time-consuming to set up and use. IPS programming is more difficult to scale production. As volumes and/or programming memories increase, the line may turn into a bottleneck.
Off-Line Device Programming
The most common method for programming semiconductor devices is “offline.” This method involves the use of a specialized piece of equipment called a device programmer that is used to transfer data or code to the device. The programmer or development kit connects to the device either directly or by a socket and writes the code or data to the memory of the device. This method is relatively simple and straightforward, but may not be suitable for high-volume production.
To overcome the limitations of manual device programming, automated device programming systems can be used for high-volume production. These systems typically include multiple device programmers that are integrated into a single robotic platform, which can be controlled by a computer and a central controller. Automated device programming systems can significantly increase the efficiency and speed of programming semiconductor devices. They can also improve the accuracy and consistency of the programming process by automating repetitive tasks. Additionally, automated systems can be equipped with advanced features such as data logging, monitoring, and testing to ensure the quality of the programming process. Marking and media transfer are also possible.
A gang programmer has multiple sockets to program multiple devices at once. It can program a wide range of devices, from small microcontrollers to high-density flash memories. This makes it a versatile option for high-mix production environments where different types of devices need to be programmed.
Inline SMT Programming
Yet another method for programming semiconductor devices is through the use of Inline SMT Programming method. The process involves programming the devices during the Surface Mount Technology (SMT) assembly process. This method is suitable for high-volume production as it allows for the simultaneous programming and assembly of the devices. It is also cost-effective as it eliminates the need for a separate device programmer or ISP process. However, it requires specialized equipment and knowledge to execute properly; in addition, changes to existing workflows are expensive, time-consuming, and require testing to ensure everything is working correctly, delaying production until everything is checked and ready.
Which Method is Best?
There are several methods available for programming semiconductor devices, each with its own advantages and disadvantages. ISP is a cost-effective option for high-volume production but can be complex to set up and use. Off-line manual device programming is straightforward and easy to use but is not a good candidate for high-volume production. Automated device programming systems can significantly increase the efficiency and speed of programming semiconductor devices, improve the accuracy and consistency of the programming process and ensure the quality of the programming process. Inline SMT Programming is a cost-effective option for high-volume production with no changes to the boards, eliminates the need for a separate device programmer or ISP process, but requires specialized equipment and knowledge. The choice of method will depend on the specific requirements of the application and the resources available.
Learn more:
- White Paper: Semiconductor Device programming
- CSP Programming Strategies for the C-Suite
- BPM White Papers and Case Studies
- BPWin API (Application Programming Interface)
- Integrate your ERP to BPM Programmers with API
- BPM API Delivers Quality and Traceability
- Device Programming for the Technical Buyer
- Ease of Use(Opens in a new browser tab)
- Sweat the Details: Up-Time, Accuracy, and Waveforms
- Up-Time, Accuracy, and Waveforms
BPM’s Automotive Programming Solutions
BPM’s Automotive Programming Solutions Programming for the Automotive Market As data density, device complexity and the sheer number of devices in a car continue to increase, reducing programming costs is critical. In-system, in-circuit and in-line programming...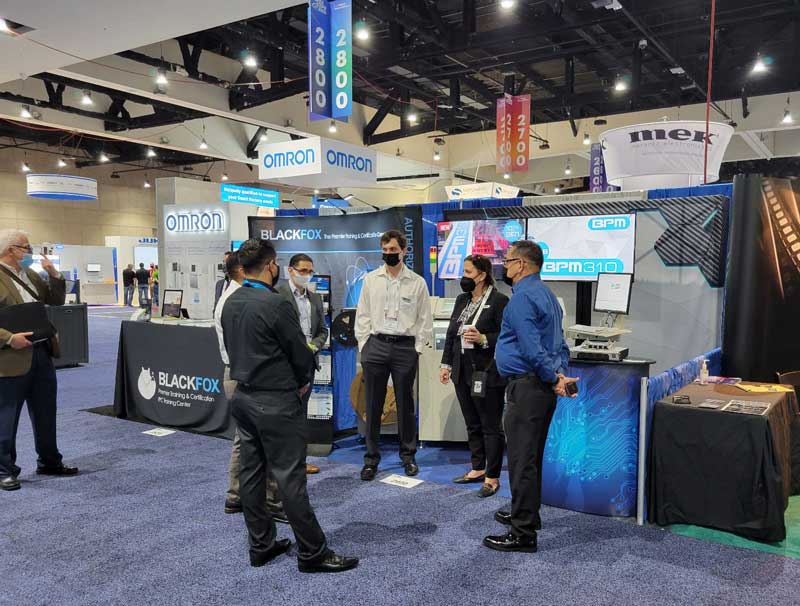