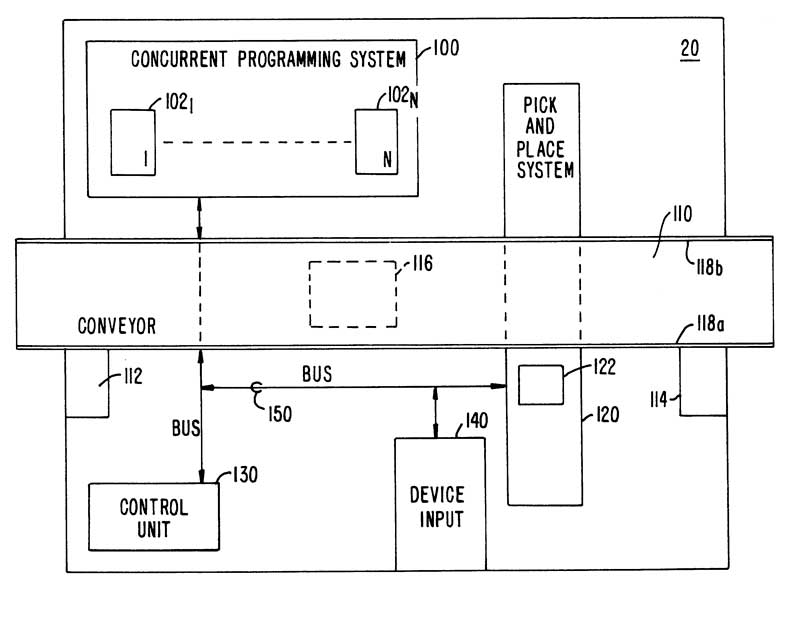
US Patent: In-line programming system and method
Patent No: 6,230,067 (B1)
- Inventor: William H. White
Abstract
Description
CROSS-REFERENCES TO RELATED APPLICATIONS
This application is related to U.S. Provisional Patent Application Ser. No. 60/117,873, filed Jan. 29, 1999, entitled “IN-LINE PROGRAMMING DEVICE WITH SELF-TEACHING CAPABILITY,” the disclosure of which is hereby incorporated by reference in its entirety.
BACKGROUND OF THE INVENTION
The present invention generally relates to concurrent automated programming of programmable electronic devices, and more particularly to programming and testing multiple device types and patterns and performing circuit board assembly simultaneously in a single in-line programming device.
In the semiconductor industry, a considerable number of electronic devices such as programmable integrated circuit (PIC) devices are provided by vendors in the programmable form with blank memories or unspecified connections between arrays of logic. Users can then custom configure or program the electronic devices to perform their intended function by programming them, transferring or “burning in” a sequence of operating codes into the memory, or by specifying a particular arrangement of gating logic connections.
Numerous manufacturers have developed automated machinery for handling and programming such devices. Such machinery moves blank devices from a source medium (e.g., trays, tubes, tape) to one or more programming sites, carry out the programming operation on each device, and moves programmed devices from the programming sites to an output medium (e.g., trays, tubes, tape). Typical users of automated programming equipment are highly sensitive to system throughput, which is typically measured incorrectly programmed devices per hour, and yield, which is typically defined as the percentage of devices that are correctly programmed.
Before any printed circuit board assembly (PCBA) containing a programmable integrated circuit (PIC) can be used, the PIC must be configured or programmed, so that it may perform its intended function. During programming, a pattern is loaded into the unprogrammed PIC. These patterns may be changed from time to time as the requirements of the function of the PCBA change over time. Also, in some applications, the pattern may be individualized for each PCBA that is assembled.
For years, PICs have been programmed before being assembled onto a printed circuit board using a methodology called off-line programming (OLP). This, however, created some problems in that OLP of the PICs has to be performed prior to assembly. Specialized equipment must also be obtained to perform OLP. Further, OLP has to be scheduled, which may delay the manufacture of PCBAs and create scheduling problems and bottlenecks in the process. Moreover, once the PICs are programmed, they must be stored until the assembly process begins. This storage and related delay typically create an inventory of programmed PICs. Not only does this inventory cost money, but in the event that a pattern change is required immediately, the inventory of programmed PICs may have to be destroyed, which adds to the cost and creates an additional delay before the assembly of more PCBAs can commence.
To solve these problems, a technique called in-circuit programming (ICP) was developed. ICP allows for a PIC to be programmed after it is placed on a printed circuit board, i.e., after the PCBA is assembled. Thus, the need for an inventory of programmed devices was eliminated, and individualized PICs no longer needed to be matched with the corresponding PCBA because all the PICs are identical (unprogrammed) at assembly time.
However, new problems arose. For example, because it is not feasible to program all PICs in-circuit, the designers of the PCBA must choose only devices that are ICP compatible. ICP compatible PICs cost more than similar non-ICP compatible PICs in many cases, so the cost of the PCBA may be higher when using ICP. Additionally, the PCBA design may be more complex to accommodate ICP, so the time to market may be negatively impacted. Furthermore, specialized equipment is required, and software must be written, perform the programming operation, which also may impact time to market for the PCBA. Since the programming operation may take a number of minutes to perform, a production line may be slowed down waiting for programming to complete. To address this throughput problem, some users may set up several ICP programming stations to service a single PCBA assembly line. However, this solution requires additional equipment, floor space in the factory, and capital outlay. Additionally, if the application for the PCBA requires that the PICs be programmed with individualized patterns, it may be necessary to match the individual PICs with their corresponding individual PCBAs. This additional complication adds additional cost and complexity to the assembly operation. Finally, in the event that the PIC fails to program, the entire PCBA will have to be reworked to replace the PIC.
Accordingly, what is needed in the art is a system and methodology for programming PICs and assembling PCBAs without the drawbacks associated with the off-line programming and in-circuit programming techniques.
SUMMARY OF THE INVENTION
Briefly, the invention provides in-line programming techniques for programming and testing any combination of devices and patterns. The techniques of the present invention are useful for programming a variety of types of programmable integrated circuit devices (PICs), including, for example, flash memories, EEPROMs, microcontrollers, PLDs, PALs, FPGAs, and the like. According to the invention, in-line programming (ILP) system programs and tests PICs and performs the assembly of printed circuit board assemblies (PCBAs). Printed circuit boards enter and leave the ILP system on a conveyor system. PICs are loaded into the ILP system, and the ILP system automatically programs and tests the PICs and places them onto the PCBs as the PCBs arrive on the conveyor.
The present invention addresses all of the above problems (e.g., costs, complications, and delays) by performing the programming and testing operations with the same piece of equipment that performs the assembly operation. Using the techniques of the present invention, PICs are programmed on demand so the need for an inventory of programmed PICs is eliminated, and changes to the program pattern may be incorporated immediately without waste. Any PICs that fail to program are rejected by the ILP system so that bad PICs are never placed onto a PCBA. Because the PCBA does not have to be designed to accommodate an in-circuit programming technique, the PCBA designer is unconstrained in the choice of PICs. The ILP system generally programs PICs faster than PICs can be programmed using the in-circuit programming methodology. The ILP system is also able to program a number of devices simultaneously, allowing a PCBA assembly line to produce PCBAs at a faster pace than that at which a single PIC can be programmed. Thus, an assembly line incorporating an ILP system may be smaller and produce PCBAs faster, with higher quality and less expense than an assembly line incorporating an in-circuit programming system. Further, the use of an ILP system in an assembly line allows for PCBAs to be produced less expensively than in an assembly line incorporating programmed PICs from an off-line programming system.
According to an aspect of the present invention, a method of automatically assembling a printed circuit board assembly (PCBA) in an assembly apparatus is provided. The method typically comprises the steps of a) receiving, in the assembly apparatus, a programmable electronic device to be programmed, and b) automatically programming the electronic device in the assembly apparatus. The method also typically includes the steps of c) receiving a printed circuit board in the assembly apparatus, and d) assembling the PCBA in the assembly apparatus by automatically placing the programmed electronic device on the printed circuit board so as to form the PCBA.
According to another aspect of the present invention, an assembly apparatus capable of automatically assembling a printed circuit board assembly (PCBA) is provided. The apparatus typically comprises a means for receiving, in the assembly apparatus, a programmable electronic device to be programmed, and a means for automatically programming the electronic device in the assembly apparatus. The apparatus also typically includes a means for receiving a printed circuit board in the assembly apparatus, and a means for automatically placing the programmed electronic device on the printed circuit board so as to form the PCBA.