by Colin Harper | Mar 7, 2024 | Announcements, Events, News, Trade Shows
BPM Microsystems, Inc. will display its 10th Generation programming technology platform and the BPM310 Automated Programming System at the IPC APEX Expo, from April 9-11, 2024, in Anaheim, California at the Anaheim Convention Center. BPM’s 10th Generation offers the industry’s fastest programming times for UFS, eMMC, Flash, and MCUs with twice as many sockets per site as its predecessor. The BPM310 offers a capacity of up to 48 sockets, automotive-level quality, and reliability in a small footprint. 10th Gen delivers the fastest UFS programming performance in the industry achieving up to 440MB per second Read and 201MB per second Write. First-part time is accelerated owing to the fact that UFS programming can commence without pausing for data to download.
Set Appointment for One-on-One Demo
IPC APEX ’24
IPC APEX Expo is the largest event for electronics manufacturing in North America, attracting more than 9,000 professionals from 45 countries. From the industry’s leading technical conference and application-focused professional development courses to the innovation-driven exhibit floor, IPC APEX EXPO 2024 will be packed with seminars, awards, and amazing technology.
BPM is celebrating 23 years of exhibiting at APEX and has been a proud Member of IPC for 25 years. Make plans now to attend IPC APEX Expo ’24 April 9-11, 2024 at the Anaheim Convention Center. (view event page here).
BPM310 APS
The BPM310 is positioned to outperform higher-priced systems and includes advanced features such as WhisperTeach™, on-the-fly vision alignment, CSP support, serialization, encryption, and JobMaster while providing true universal technology. 10th Gen supports the broadest range of devices including MCUs, eMMC, NAND, Serial Flash, UFS, and others. Highly configurable, the BPM310 provides options for Tape I/O, Tray I/O, Tube I/O, laser marking, and 3D inspection.
“We’re anticipating another great show at APEX 2024, and we’re looking forward to meeting customers in this fantastic setting.” says Penny Santhanam, Sr. Director of Customer Success at BPM. “The market has really responded positively to our 10th Generation technology. The flexible configurability of the BPM310 with scalable socket density has been a game changer for our customers. The small footprint, amazing productivity, and ease of use set it apart in the industry.”
The BPM310 leverages much of the socket adapter and algorithm development currently available on BPM’s 9th Generation systems. And like 9th Gen automated programmers, the BPM310 continues to offer ease of operation and fast setup with award-winning BPWin process control software and patented WhisperTeach™. WhisperTeach™ automatically teaches the critical Z-height of each pick/place location with 15-micron accuracy. Accurate automated teaching is vital for small packages due to fundamental human limitations. In addition, WhisperTeach™ saves an average of 83% of the time required for the job setup compared to traditional methods while increasing quality and yield
BPM manufactures 10th Generation systems in their ISO 9001:2015 certified plant located in Houston, Texas, and their products carry the CE Mark. BPM continues to offer 9th Generation programmers for manual and automated programming. If you are attending APEX 2024, please visit booth 2720 and we will be happy to discuss your programming requirements and demonstrate our BPM310 Automated Programming System. For more information on the BPM310, go to www.bpmmicro.com/BPM310.
Set Appointment for One-on-One Demo |
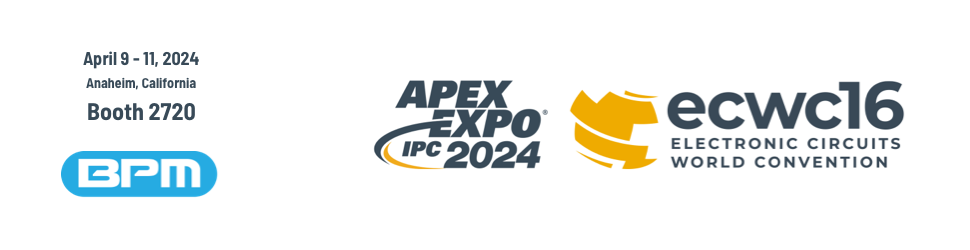
by Colin Harper | Feb 28, 2024 | Cybersecurity, News
In the age of interconnected devices, the significance of cybersecurity within the Internet of Things (IoT) ecosystem has never been more paramount. As these devices permeate every aspect of our lives—from healthcare to automotive, home automation to industrial control systems—their security implications scale correspondingly. The exponential growth of IoT devices has brought forth not only convenience and efficiency but also a myriad of security challenges, making it crucial for stakeholders to prioritize robust security measures to protect sensitive data and maintain device integrity.
The regulatory landscape for IoT security is rapidly evolving, with jurisdictions around the world establishing frameworks to safeguard these technologies. The European Union’s Cybersecurity Act and the United States’ IoT Cybersecurity Improvement Act of 2020 exemplify legislative efforts aimed at setting a baseline for cybersecurity practices. These regulations not only mandate security standards but also encourage manufacturers and developers to adopt security-by-design principles, ensuring that devices are secure from the outset.
In the EU, the General Data Protection Regulation (GDPR) that became effective on May 25, 2018, focuses on data privacy, which impacts IoT devices that collect personal data. The EU Cybersecurity Act, effective June 27, 2019, strengthens the EU’s cybersecurity framework by establishing a certification framework for ICT products, services, and processes, including IoT devices. Furthermore, the EU introduced the NIS Directive 2, requiring EU countries to pass laws by October 2024 to enhance national cybersecurity. The Cyber Resilience Act, proposed in 2022 and expected to be formally approved in 2024, introduces specific obligations for products with digital elements, aiming to embed cybersecurity throughout their lifecycle.
The Cyber Resilience Act is particularly noteworthy as it represents the first EU-wide legislation to impose cybersecurity rules on IoT manufacturers and developers. This legislation requires IoT device makers to inform authorities and consumers about attacks and mandates quick fixes to problems. Moreover, it establishes significant penalties for non-compliance, up to €15 million or 2.5% of the previous year’s global turnover, and gives the EU powers to recall and ban non-compliant products. The Act emphasizes the importance of security by design, mandating that IoT products meet “essential” cybersecurity requirements before they can go to market. Manufacturers will need to start incorporating security at the design stage to ensure that devices are compliant with the upcoming regulations.
In the US, the landscape is more fragmented, with no comprehensive federal law specifically targeting IoT security. However, the IoT Cybersecurity Improvement Act of 2020, signed into law on December 4, 2020, represents a significant step toward regulating IoT security at the federal level. This law mandates the National Institute of Standards and Technology (NIST) to develop and manage IoT cybersecurity standards for federal government devices. Additionally, California has taken a proactive stance with its own IoT cybersecurity law, SB-327, effective January 1, 2020, which requires manufacturers of connected devices to equip them with reasonable security features.
These regulatory efforts in the EU and US illustrate a growing recognition of the need for robust cybersecurity measures to protect the increasing number of connected devices. The emphasis on security by design and the requirement for manufacturers to be more transparent about the cybersecurity of their devices are critical steps towards ensuring that IoT devices are secure from their inception and throughout their lifecycle.
BPM Microsystems emerges as a leader in this challenging environment, with its pioneering role in device programming emphasizing its commitment to security and innovation. Specializing in the development of programming technologies for microcontrollers, flash memories, and other components, BPM Microsystems understands the criticality of secure device programming in the IoT ecosystem. Its solutions are designed to cater to the pressing need for secure programming practices, ensuring that devices are safeguarded against unauthorized access and tampering from the manufacturing stage.
A testament to BPM Microsystems’ dedication to cybersecurity is BPM.NCRYPT, a feature that underscores the company’s comprehensive approach to encryption and secure programming. BPM.NCRYPT provides an extra layer of security by ensuring that data remains encrypted throughout the programming process, minimizing the risk of interception or tampering. This feature is integral to BPM Microsystems’ efforts to meet and exceed the security requirements in device programming, offering manufacturers a reliable solution for securing their devices.
The BPWin software further amplifies BPM Microsystems’ commitment to security through its support for encryption. For years, BPWin has facilitated secure programming processes, enabling manufacturers to program devices with the assurance that their data is protected. This software is pivotal in enhancing the security of device programming operations, underscoring BPM Microsystems’ role in addressing the evolving cyber threats facing the IoT landscape.
BPM Microsystems’ adoption of the security-by-design principle is emblematic of its proactive approach to cybersecurity. By integrating security features early in the device development cycle, the company ensures that its products are not only compliant with current standards but also equipped to mitigate future risks effectively. This principle is fundamental to developing secure, reliable IoT devices that can withstand the complexities of the modern cyber environment. By adhering to these guidelines, BPM Microsystems not only reinforces its position as a thought leader in secure device programming but also contributes to the overall safety and reliability of IoT technologies.
Looking ahead, the challenges in IoT security are set to grow in complexity and scale. However, BPM Microsystems is well-positioned to address these challenges through continuous innovation and adherence to best practices in cybersecurity. The company’s commitment to developing secure programming solutions is vital to the future of IoT security, ensuring that devices remain protected against an ever-evolving landscape of cyber threats.
In conclusion, the imperative for secure device programming in safeguarding IoT devices cannot be overstated. As regulations within the IoT landscape continue to expand, the role of industry leaders like BPM Microsystems in navigating the complexities of IoT security becomes increasingly critical. Through its pioneering solutions and commitment to cybersecurity, BPM Microsystems exemplifies the importance of a proactive and comprehensive approach to securing IoT devices. Stakeholders across the IoT spectrum would do well to recognize the value of partnering with companies that prioritize security, ensuring a safer and more secure future for IoT technologies.
by Scott Bronstad | Nov 7, 2023 | Announcements, Events, News, Trade Shows
BPM Microsystems, a global leader in device programming and cybersecurity solutions, is set to exhibit at Productronica 2023. The event will take place from November 14-17 in Munich, Germany. BPM Microsystems can be found in Hall A1, Stand 357.
Unveiling Revolutionary Products
The company will showcase its groundbreaking BPM310 Automated Programmer and the highly versatile 2900 Manual Programmer. These state-of-the-art solutions feature modular designs, weekly algorithm updates, and a high-capacity queue system, designed to meet the highest programming and cybersecurity standards. “Our attendance at Productronica 2023 marks a significant milestone in advancing the programming industry,” says Penny Santhanam, Senior Director of Customer Care at BPM Microsystems. “The BPM310 and the 2900 Manual Programmer are engineered to provide unprecedented reliability and scalability, addressing the ever-growing challenges of device programming.”
Experience the Future with Hands-On Demos
Attendees have the opportunity to schedule one-on-one demos for an in-depth look at the company’s latest innovations. The demos will be overseen by Pierce Weiss, Executive Account Manager, who will be representing BPM Microsystems at the event. “In an industry where technology is constantly evolving, it’s crucial to stay ahead of the curve. Our one-on-one demos at Productronica will show how our solutions do just that—setting new benchmarks in efficiency, flexibility, and reliability,” says Pierce Weiss.
Celebrating Partnerships and More
BPM Microsystems also takes this opportunity to celebrate the 20th anniversary of their distribution partner in the UK, Germany, and France, Adaptsys. In honor of the occasion, a series of special offers and exclusive giveaways are planned for attendees. Event-goers can enjoy a juice bar in the mornings, a beer tap in the afternoons, and an exclusive cocktail party on November 15.
Interactive Contests
Adding to the excitement, BPM will also feature a prize wheel and a chipping contest. Attendees who spin the prize wheel will be entered into a drawing for a drone, providing multiple avenues for engagement and wins.
About BPM Microsystems
Founded in 1985, BPM Microsystems serves more than 2,000 companies in over 49 countries. With a focus on modular design and an ability to release new programming algorithms weekly, the company has become a trusted supplier to customers in various industries including automotive, aerospace, medical, industrial, and mobile devices. For media inquiries, please contact Scott Bronstad.
Learn More | Schedule One-On-One Machine Demo | Request a Free Exhibit Pass (first 50)
by Scott Bronstad | Oct 12, 2023 | Events, News, Trade Shows
BPM Microsystems Makes an Impact at SMTA International Trade Exhibition
BPM Microsystems, the industry leader in high-performance device programming and cybersecurity solutions, showcased its pioneering technologies at the recently concluded SMTA International Trade Exhibition, held on October 10-11 in Minneapolis.
BPM Microsystems’ booth attracted a diverse group of professionals, underscoring its wide-reaching appeal in the industry. Among the attendees who engaged with BPM were Process Engineers, Strategic Planning Managers, and Product Development Specialists from globally recognized electronic component suppliers and manufacturers. Senior Engineers from top automotive manufacturers and technology giants also expressed keen interest in BPM’s state-of-the-art solutions. It was noted that women were strongly represented, reflecting the inclusive nature of the industry and the event.
Colin Harper, Director of Product Management at BPM Microsystems, remarked, “We’re thrilled with the positive feedback and strong interest from a broad range of industry specialists. Participating in SMTA International not only allowed us to showcase our innovative solutions but also gave us the opportunity to engage and understand the evolving needs of our clients.”
In an exciting side event, BPM Microsystems also conducted a giveaway where attendees at the booth had a chance to win a drone. The winner will be announced soon, adding an element of fun to what has been a productive exhibition for BPM.
The company looks forward to building on these connections and continuing to drive innovation in device programming and cybersecurity solutions.
by Scott Bronstad | Oct 9, 2023 | Announcements, Events, News, Trade Shows
BPM, an established leader in device programming solutions, is excited to announce its participation in the SMTA International Trade Show on October 10-11 in Minneapolis. Focusing on its proven 2900 Manual Programmer, BPM will be stationed at Booth 1215 to demonstrate how the device excels at programming complex and data-dense products.
Representing BPM are Colin Harper, Director of Sales and Product Development, and Pierce Weiss, Executive Sales Manager. Both will be on hand to explain the numerous benefits and efficiencies gained by bringing device programming in-house, particularly for complex and data-rich devices.
“SMTA International offers a vital platform for BPM to showcase how the 2900 Manual Programmer, a cornerstone in our product line for several years, solves the unique challenges posed by complex and data-heavy devices,” states Colin Harper.
What to Expect at Booth 1215 Event Page
- Targeted demonstrations of the 2900 Manual Programmer’s capabilities in programming complex and data-dense devices
- Hands-on experiences allow attendees to familiarize themselves with the 2900
- Exclusive previews of forthcoming advancements in BPM’s device programming solutions
- Special promotions and giveaways exclusively for booth visitors
“The SMTA International Trade Show provides an invaluable chance for one-on-one, live conversations about how to advance capabilities in the rapidly evolving field of device programming,” adds Pierce Weiss, Executive Sales Manager.
Attendees interested in discussing how to elevate their device programming capabilities, particularly for complex and data-dense devices, are encouraged to schedule a one-on-one meeting with Colin Harper or Pierce Weiss. For appointment bookings, please schedule using Calendly here.
Schedule One-On-One
About BPM
With more than three decades of experience, BPM is a global authority in device programming solutions. Known for innovating reliable, quick, and adaptable products like the 2900 Manual Programmer, BPM has long been the go-to choice for industries ranging from automotive and aerospace to healthcare and consumer electronics. With a global footprint spanning over 50 countries and a robust network of partners and distributors, BPM remains committed to delivering top-notch, scalable solutions suited for programming complex and data-rich devices.
by Scott Bronstad | Sep 22, 2023 | Announcements, News
Since their launch in the mid-2000s, BPM Microsystems’ 7th Generation programmers have been an instrumental part of the company’s award-winning lineup. With a legacy spanning close to two decades, these programmers have fulfilled a variety of roles in industries ranging from automotive to aerospace. However, every legacy has its finale, and BPM has recently announced the last buy for its 7th Generation programmers. Driven by supply chain constraints, this move is not just a product life-cycle decision, but a strategy to focus on support and future technologies. As of today, BPM will no longer sell 7th Gen programmers and sites*. In this article, we’ll dive deep into the why, the how, and the what-next of this pivotal moment.
*Contact Inside Sales for more details.
Why End Production Now?
The decision to cease the sale of 7th Generation programmers comes against a specific backdrop:
Supply Chain Constraints
Due to the unavailability of critical devices essential for the manufacture of 7th Generation programmers, the decision was made to focus on supporting existing products rather than producing new units. These supply chain constraints played a crucial role in determining the timing of the last buy.
Resource Re-Allocation
With these supply chain issues in mind, BPM made a calculated decision to divert its resources towards service, support, and the development of new technologies like their 9th Generation programmers.
Continued Commitment to Support
Unlike some in the industry, BPM is committed not to leave its user base in the lurch. Even with the halt in production, BPM assures ongoing support for existing 7th Generation programmer users:
- Device Algorithms: BPM will continue to roll out new programming algorithms to ensure the programmers remain functional.
- Technical Support: Expertise is just a call or an email away, thanks to BPM’s technical support team.
- Parts and Accessories: Despite supply chain constraints affecting new unit production, essential parts will still be supplied for repairs and maintenance while the components last.
The Way Forward: Spotlight on the 9th Generation
These state-of-the-art 9th Gen programmers come with several enhancements:
- Faster Programming Speeds: Utilizing parallelism to a greater extent, these new models offer speed advantages that can significantly cut down production times.
- Advanced Cybersecurity: Newer security protocols align with the increasing cybersecurity demands of industries such as automotive and medical devices.
- Greater Versatility: The 9th Generation models are designed with modular architecture, making them incredibly adaptable to the rapidly changing technological landscape.
- On-board Memory: 7th Gen sites come standard with .5 GB (512 MB) of on-board memory. 9th Gen sites are configured with 256 GB of on-board memory, and can be upgraded to twice that amount. (1 Gigabyte is equal to 1000 megabytes)
Why Transition to the 9th Generation?
Given the discontinuation of the 7th Generation, here’s why transitioning to the 9th Generation might be a prudent choice:
- Future-Proofing: With more modular components and an architecture designed for adaptability, these models are geared for the future.
- Cost-Efficiency: The improved speed and reduced cycle times result in cost benefits in the long run.
- Training and Support: BPM’s robust training services ensure that the transition to newer technology is smooth, minimizing any potential downtime.
Socket Adapter Compatibility:
|
|
Manual
|
Automated |
Adapter Prefix**
|
Example
|
7th Gen
|
9th Gen
|
7th Gen
|
9th Gen
|
WSM |
WSM32PA |
No |
No |
No |
No |
LSM |
LSM2S676FGMSSOCB |
No |
No |
Yes |
Limited Support * |
LXSM |
LXSM28FLPZA |
No |
No |
Yes |
Limited Support * |
LX2SM |
LX2SM28FLPZB |
No |
No |
Yes |
Limited Support * |
LX4SM |
LX4SM40DIPLT |
No |
No |
Yes |
Limited Support * |
LASM |
LASM324BGV |
Yes |
Limited Support * |
Yes |
Limited Support * |
LXASM |
LXASM484BGAV |
Yes |
Limited Support * |
Yes |
Limited Support * |
LX2ASM |
LX2ASM473BGA |
Yes |
Limited Support * |
Yes |
Limited Support * |
LX4ASM |
LX4ASMR64QFPTB |
Yes |
Limited Support * |
Yes |
Limited Support * |
WASM |
WASM20MLFA |
Yes |
Limited Support * |
Yes |
Limited Support * |
WXASM |
WXASM100QE |
Yes |
Limited Support * |
Yes |
Limited Support * |
WX2ASM |
WX2ASML48UBG |
Yes |
Limited Support * |
Yes |
Limited Support * |
WX4ASM |
WX4ASMR08SJA |
Yes |
Limited Support * |
Yes |
Limited Support * |
Limited Support *: Replacement D-Card for Legacy Socket Module: Check BPWin to confirm device and adapter compatibility. 9th Gen does support a limited number of legacy d-cards.
Daughter Cards (D-Cards)**: 6th and 7th Gen Programmers require a socket module base. D-Cards plug into the base. 9th Gen programmers do not require a base.
Vector Engine BitBlast Program and Verify Time Comparison:
SanDisk SDIN5C2-8G (8GB)
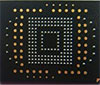
-
Without BitBlast- 2091 Seconds
-
With BitBlast- 933 Seconds
-
Without BitBlast- 1070 Seconds
-
With BitBlast- 469 Seconds
Micron MTFC4GGQ-DI-WT (4GB)
-
Without BitBlast- 1083 Seconds
-
With BitBlast- 469 Seconds
Toshiba THGBM1G5D2EBAI7 (4GB)
-
Without BitBlast- 959 Seconds
-
With BitBlast- 460 Seconds
Samsung KLM2G1DEHE-B101 (2GB)
-
Without BitBlast- 488 Seconds
-
With BitBlast- 398 Seconds
Conclusion
The last buy of the 7th Generation programmers might signify an end, but it’s also a starting point for new opportunities and advancements. The decision, dictated by supply chain constraints and a strategic focus on future technologies, brings us to the cusp of a new era with BPM’s new Generation of programmers. Existing users of the 7th Generation need not worry, as BPM continues its commitment to exceptional service and support.
Additional Resources